A material resembling small glass beads will serve as a critical ingredient to heating up the first melter at Hanford’s Waste Treatment and Immobilization Plant (WTP) set for later this year.
Office of Environmental Management
September 21, 2021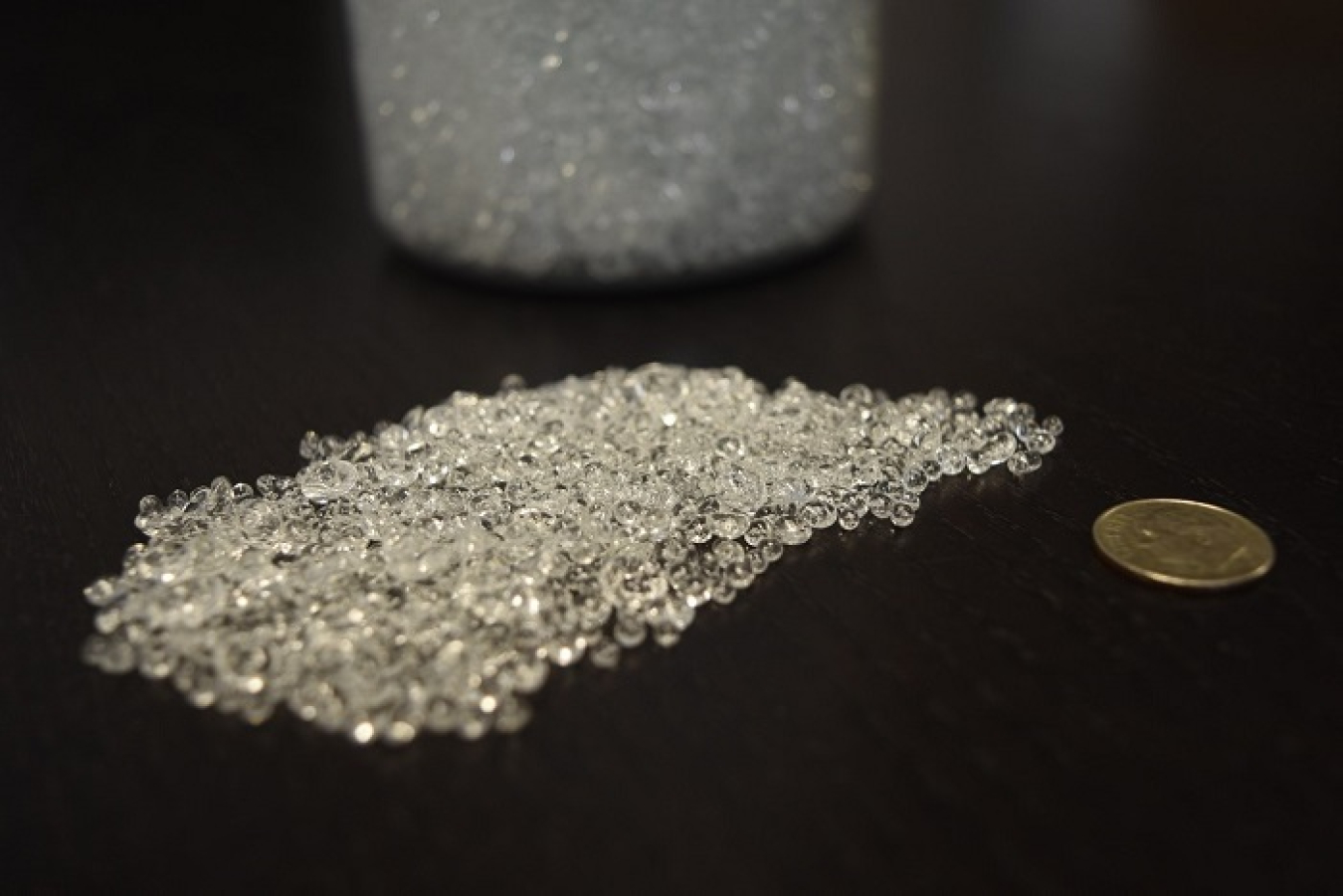
RICHLAND, Wash. – A material resembling small glass beads will serve as a critical ingredient to heating up the first melter at Hanford’s Waste Treatment and Immobilization Plant (WTP) set for later this year.
Glass frit is a mixture of chemicals that will mimic waste materials during the melter heatup process in the Low-Activity Waste (LAW) Facility. The melter is at the heart of the vitrification process that transforms radioactive and chemical waste into an immobilized glass form safe for disposal through the Direct-Feed Low-Activity Waste (DFLAW) Program. The DFLAW Program is a system of interdependent projects and infrastructure improvements, managed and highly integrated, that must operate together to vitrify the waste.
Richland-based company Fluids Controls and Components Inc. (FCCI) was contracted by Bechtel National Inc. (BNI), the prime contractor designing, building, and commissioning the plant, to provide 108,000 pounds of the frit. FCCI has also provided valves, piping, and piping components for plant construction.
“It was the first time we dealt with frit,” said Russ Watson, FCCI vice president. “The chemistry and physical profile of the frit were very complex. The specifications were strict, and the monitoring process was extensive.”
During vitrification, waste treated near large underground tanks to remove radioactive cesium and solids will be mixed with glass-forming materials, then fed to the LAW Facility’s melters. The mixture will be heated to 2,100 degrees Fahrenheit and poured into specially designed stainless-steel containers for disposal at the nearby Integrated Disposal Facility.
The frit will be used only during melter heatup. It mimics waste by dissolving into a solid form at high temperatures. During the heatup process, the glass frit will be flushed out of the melter with a simulated feed.
“Partners like FCCI are crucial to the success of the project,” said Frank Salaman, procurements and subcontracts manager for BNI. “We rely on them to meet the complex specifications the project requires.”
The project team is scheduled to initiate heatup of the first melter by the end of 2021. Information on the commissioning process, including a loss-of-power test and melter heatup, is available on the Journey to Melter Heatup website.
The plant facilities can be viewed using the self-guided Hanford Virtual Tour.
To receive the latest news and updates about the Office of Environmental Management, submit your e-mail address.