Pennsylvania State University has manufactured and validated a novel hydropower turbine-generator which can be deployed at various low-head sites.
Water Power Technologies Office
January 13, 2021After four years of comprehensive analysis and testing, Pennsylvania State University (Penn State) successfully manufactured and tested a rapidly deployable, high-efficiency hydropower turbine-generator system prototype. This modular and scalable turbine-generator was developed for energy generation at a variety of low-head sites and has the potential to significantly reduce levelized cost of energy. The university’s design uses a condition-based health monitoring system to reduce the cost of O&M and to enable advanced control of the turbine-generator system performance. A combination of condition-based maintenance and optimized control could potentially result in increased reliability and operational availability across a fleet of hydropower units.
Supported by WPTO, PSU’s project focused on producing a device that could be flexibly deployed at reduced costs. The 0.2-meter-diameter prototype was designed for scalability across a wide number of low-head hydropower applications, ranging from 10‒30 meters of head, with a power output between 100 kilowatts (kW) and 1 MW. Low-head hydropower sites tend to display higher variability of flow rates than higher-head locations, and Penn State developed its variable-speed permanent-magnet generator system to allow for high efficiencies over wide operating ranges. Using conventional and additive manufacturing techniques, Penn State produced several blades before opting for 316L—a type of stainless steel—as the prototype blade alloy due to its material strength, corrosion resistance, weldability, and cost.
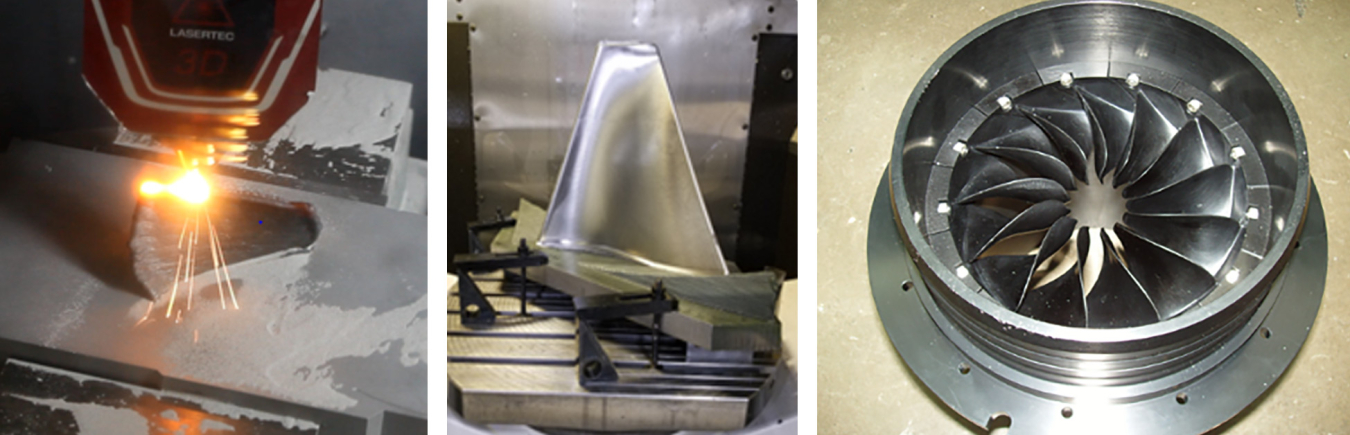
The turbine prototype was fabricated and tested at the university’s Applied Research Laboratory water tunnel. The team simulated representative fault conditions during the tunnel testing to generate realistic fault data and verify the system’s ability to identify issues. Results demonstrated the initial capital costs for Penn State’s design were competitive with existing commercial solutions, with hydraulic efficiencies approaching 90% over a broad range of flows. The team was also able to demonstrate the key advantages of additive manufacturing‒such as additional design freedom, minimization of initial material purchase, minimal postprocess machining, and elimination of fixed tooling. Future work will focus primarily on commercializing the device for wider applications.
For additional information, contact Nicholas A Jaffa.