EERE Success Story—Performance Improvements for Factory-Built Homes
December 22, 2015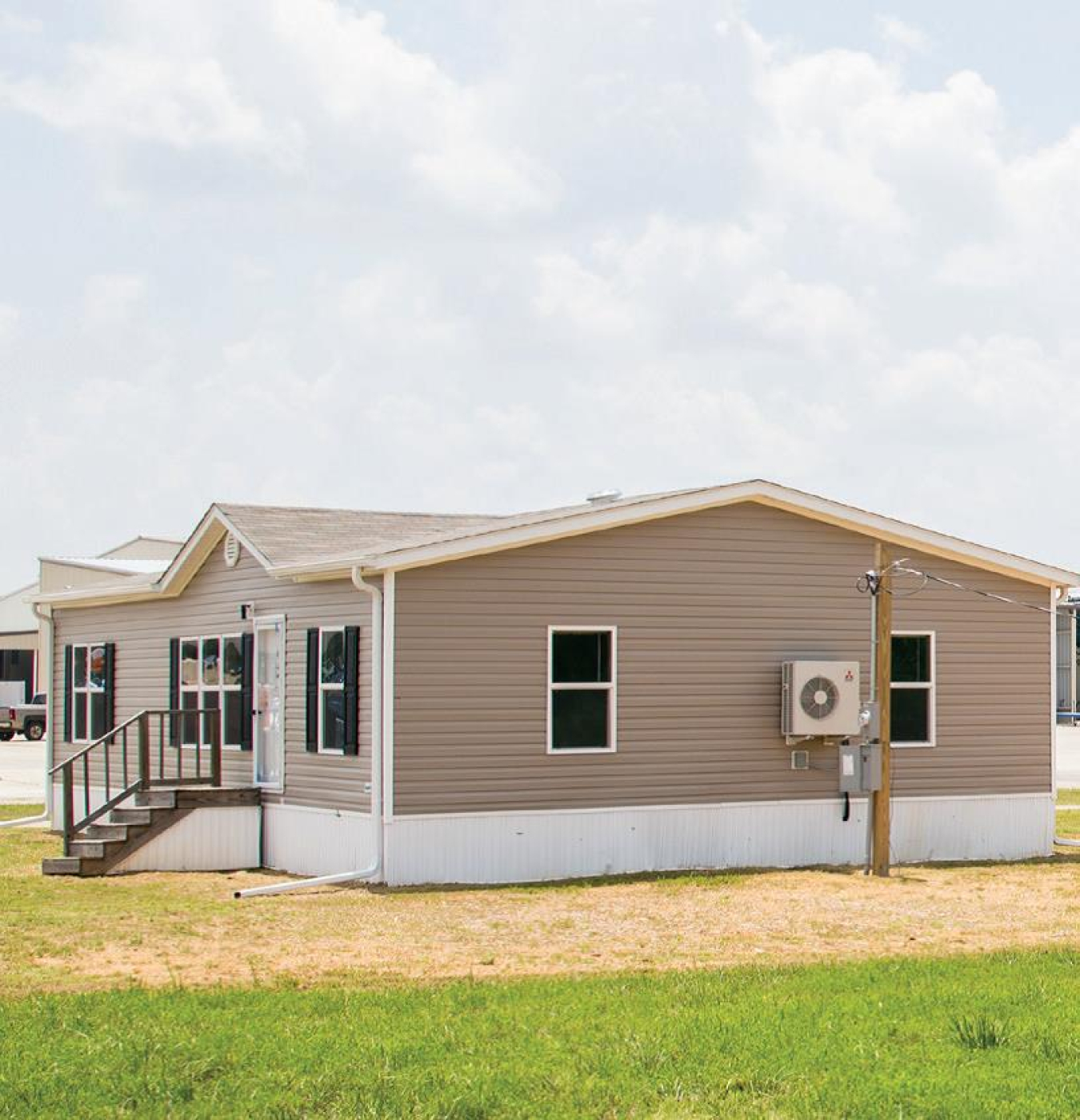
Highly efficient Building America test house in Russellville, AL. Photo Courtesy: Levy Partnership
The ARIES Collaborative, a U.S. Department of Energy (DOE) Building America research team, recently developed and evaluated methods to reduce energy use in factory-built housing, as compared to best practice HUD-code construction. The results of this research prove that it is technically feasible to construct factory-built homes to be up to 50% more energy efficient for nominal increased cost.
This approach is important to our nation’s energy use, as on average one in every six new homes built each year within the United States are factory built, and the technical approaches applied in this project are ready and available for widespread use.1
Manufactured homes are built entirely in a factory before being transported to the site for installation. The U.S. Department of Housing and Urban Development (HUD) has strict, nationally-preemptive construction and safety standards for these homes. DOE is currently engaged in the process of recommending changes to the industry’s energy standards. The work, in part, will identify technologies and approaches for meeting the new standards that have only a modest impact on home first cost, reduce monthly home operating costs (key considerations for builders in the affordable housing space), and can be readily implemented in the fast paced, production-oriented factory building environment.
To gain a better understanding of how approaches to improving design and construction practices actually impact energy use, the ARIES Collaborative compared the performance of three homes built to different technical solutions designed to three distinct levels of energy performance: Best practice HUD-code; ENERGY STAR for Manufactured Homes; and DOE’s Zero Energy Ready Home program performance levels.
Three homes were built (one for each level) using the same floor plan and building configuration. The homes were set side-by-side in Russellville, Alabama (IECC Climate Zone 3) and tested under controlled conditions. These tests compared actual whole house energy use and demand, focusing on the impact that changes in envelope construction and HVAC selection and distribution systems have on space conditioning energy use.
Distinct features of the houses include:
- House A built to the HUD standards was equipped with typical electric furnace and split system air conditioner and had climate region typical insulation levels;
- The ENERGY STAR house (House B) had enhanced insulation levels, low-E double paned windows and a conventional split system heat pump; and
- House C was a next-generation design that qualified for Zero Energy Ready Home designation and included a high efficiency, single point, ductless, mini-split heat pump with a transfer fan distribution system in place of the traditional duct system for distribution.
The insulation levels and equipment were carefully balanced to provide superior performance at the lowest possible cost. Houses A and B used a standard duct system for air distribution.
The ARIES team is putting the lessons learned from this project to work building and testing a second generation design based on House C. The current effort will also provide a guidance based on the test results for designing homes using the technologies demonstrated in House C.
The Office of Energy Efficiency and Renewable Energy (EERE) success stories highlight the positive impact of its work with businesses, industry partners, universities, research labs, and other entities.
[1] U.S. Department of Energy, “Cost-Optimized Attic Insulation Solution for Factory-Built Homes” (Washington, DC: U.S. Department of Energy, 2014), http://energy.gov/sites/prod/files/2014/12/f19/ba_innovations_2014_factory_attic_insulation.pdf.