While energy management information systems (EMIS) are extremely powerful tools, they should not be considered stand-alone energy efficiency equipment capable of producing results autonomously. They require regular use by a well-resourced site operations team to fully convert data to information to insights to action to verified results.
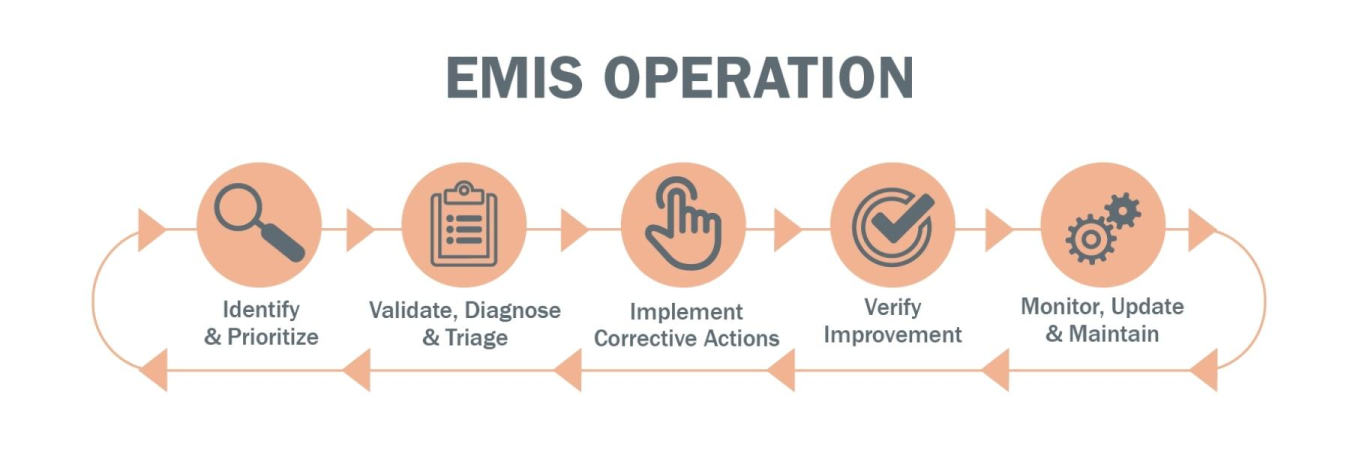
A Companion Energy Management System—Codification of Strategic Energy Management Processes
Generally, with the exception of automated supervisory controls, EMIS are human-in-the-loop tools. Ongoing EMIS activities should be integrated into the organization’s standard operating procedures, and preferably, a companion energy management system (EnMS)—the codification of strategic energy management processes as defined in International Organization for Standardization (ISO) 50001. An EnMS establishes and manages the human side of energy performance improvement and can utilize data from the EMIS to enact further energy improvements. A primary role of an EnMS is for management to create and empower an energy team and to prioritize energy improvements as a part of site operations. Creation of operational processes requires thinking through how the team will review the EMIS for improvement opportunities, take action to implement the improvements, and identify what coordination or authorizations are needed. Operational processes to be delineated should also include verification that the improvements were successful and communication of results to key stakeholders. Finally, the EMIS itself requires regular maintenance and improvements to remain effective, just like the underlying systems it is monitoring. The EnMS should manage and operate the EMIS and synergize human and data flows to optimize energy performance. The Department of Energy’s no-cost 50001 Ready program supports and provides recognition for EnMS implementation.
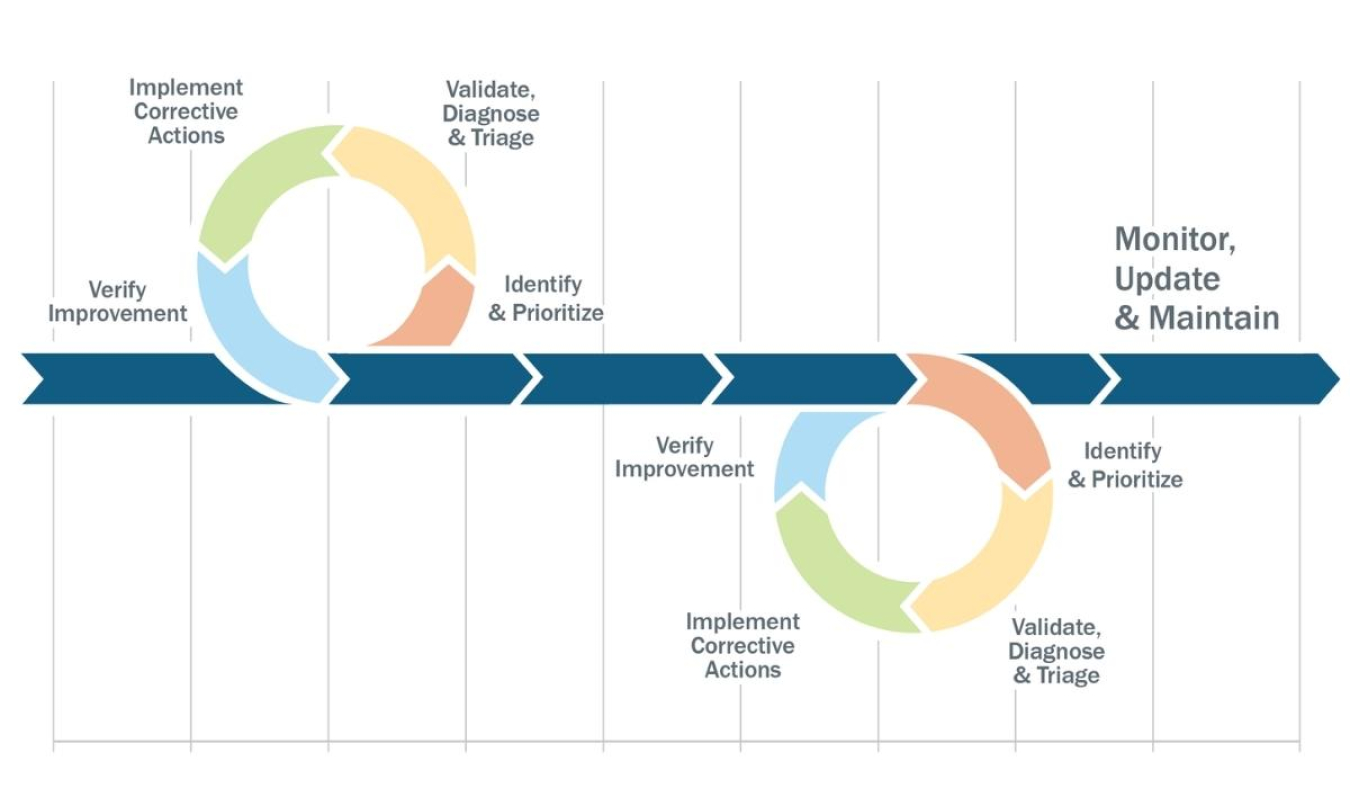
Learn how to plan an effective EMIS operational process
Download the Best Practices to Support EMIS Operation at Federal Facilities fact sheet.
Identify and Prioritize
The EnMS team can utilize the EMIS to identify improvement opportunities and prioritize them based on qualitative or quantitative metrics such as calculated energy savings and criticality. After issues are prioritized, EnMS teams can use an EMIS tracking system such as an issues log. The issues log can also be built into the EMIS software itself, allowing the EnMS team to track improvement opportunities through the implementation cycle.
It is most efficient for the EnMS team to use automated prioritization tools, if the EMIS software provides them, as the first phase of prioritizing opportunities that the EMIS uncovers. The team should perform manual prioritization only if needed. Lawrence Berkeley National Laboratory’s Monitoring-Based Commissioning Plan Template provides an example Monitoring Action Plan that can aid in this step. This document defines the metrics, views, and analytics that will be tracked to identify opportunities for performance improvement.
Validate, Diagnose, and Triage
The EnMS team then uses the EMIS and underlying systems to confirm the validity of improvement opportunities, determine root causes, and triage the opportunities into implementation categories. The data analysis and visualization tools within the EMIS can help validate issues and determine root causes. A survey of the underlying systems may be required as a second step.
Once the root cause is diagnosed, the complexity and effort involved in implementation will vary for different opportunities. Triaging the opportunities into predefined categories helps to streamline the implementation process. When creating implementation categories, consider:
- How will the criticality of opportunities be addressed? (e.g., is the improvement an emergency?)
- Who will implement the improvement? (e.g., in-house controls technician, contractor)
- Can the agency establish preapproved investment criteria to determine which performance improvement opportunities will be invested in? (e.g., preapproval for all measures with less than a one-year simple payback)
- How much will the improvement cost? (e.g., low- or no-cost, investment requiring preapproved budget, investment requiring budget that has not been approved)
- Can common measures and/or groups of similar measures be deployed across many sites in bulk to take advantage of economies of scale?
- How will improvements be transferred to or integrated with the agency’s work order system?
Finally, the EnMS team will likely uncover opportunities to improve the EMIS itself. These types of improvements should be included in the implementation process.
Implement Corrective Actions
The EnMS team then implements the prioritized improvement opportunities in each implementation category. If the improvement can be made from the EMIS or underlying control system workstation (e.g., changing a schedule), the EMIS operator can implement it right away without involving the rest of the team. For other measures, the team should develop clear recommendations for implementation.
Establish a regular EnMS meeting cadence to track system implementation, site performance, and findings from the EMIS. For example, teams can meet weekly to discuss low- or no-cost implementation opportunities, monthly for implementing energy conservation measure bundles, and quarterly for improvements to the EnMS and the EMIS itself.
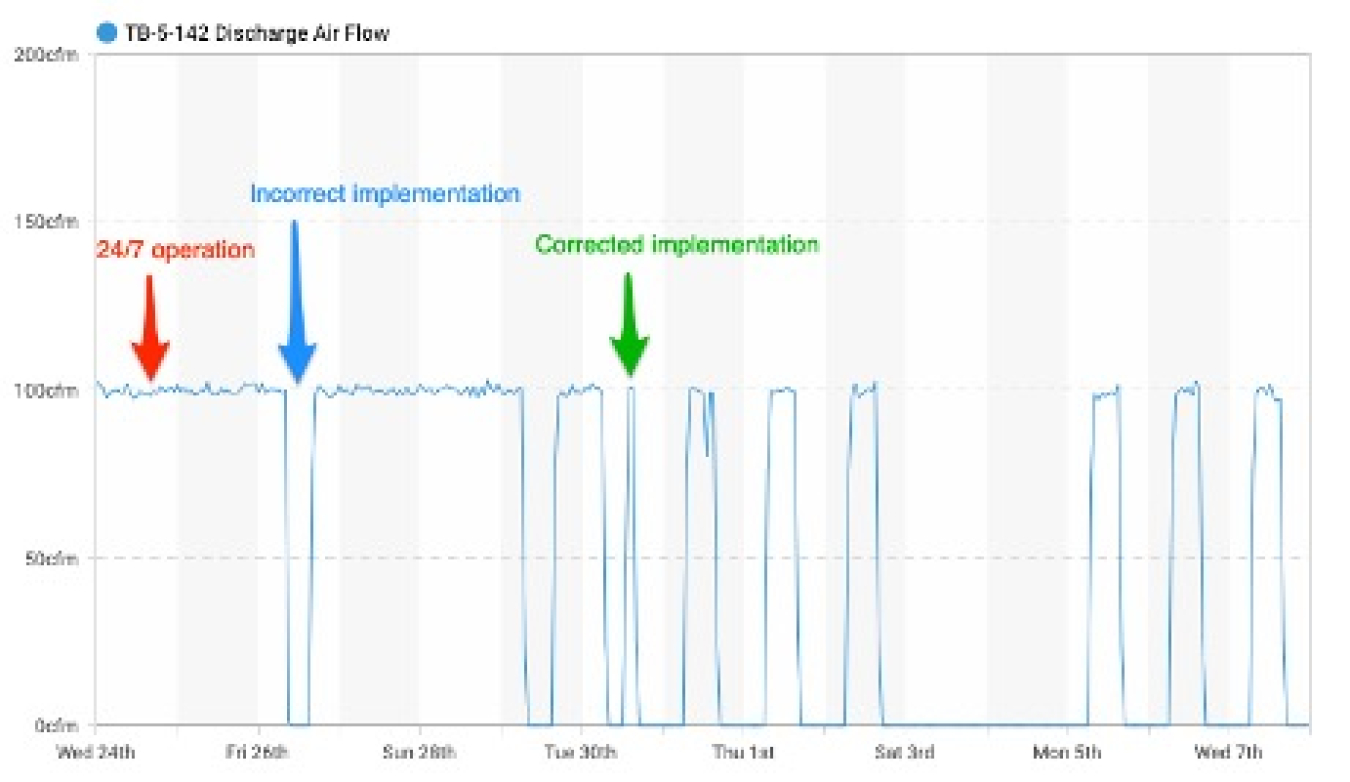
Verify Improvement
Once measures are implemented, the EnMS team can use the EMIS to ensure proper implementation. Ideally, the root cause of each issue can be reported back to the EMIS operator to improve the EMIS analytics, prioritization, and diagnosis processes. After the opportunity is verified, measurement and verification capabilities can be used to automatically or manually quantify energy and cost savings and create savings reports.
Monitor, Update, and Maintain
There are additional ongoing tasks required to support the overall process. The organization should keep team members trained on the EMIS itself. As improvements are made to building systems, building operators should be notified and trained on all changes or modifications. As the building itself changes, the building documentation (e.g., sequences of operations), standard operating procedures, cybersecurity protocols, and the EMIS itself should be updated to reflect the changes.