In the early months of 2020, researchers at the U.S. Department of Energy (DOE) were eager to address a range of technical challenges created by the COVID-19 pandemic.
June 14, 2022In the early months of 2020, researchers at the U.S. Department of Energy (DOE) were eager to address a range of technical challenges created by the COVID-19 pandemic. Vaccine distribution channels, especially for remote and rural communities lacking the necessary facilities to store the COVID-19 vaccine, became a particularly urgent point of emphasis.
To address this challenge, DOE’s Building Technologies Office (BTO) partnered with a leading American refrigeration company, Carrier Global Corp. Researchers at the Oak Ridge National Laboratory (ORNL) saw an opportunity to apply their latest research and development in refrigeration to the complex problem of vaccine distribution. By pairing an old container with a new, retrofitted system, these researchers achieved two major innovations: a new method for maintaining temperature thresholds using existing equipment, and, perhaps more valuable, a means to provide data on the experimental approach, methods, and results to other companies and scientists.
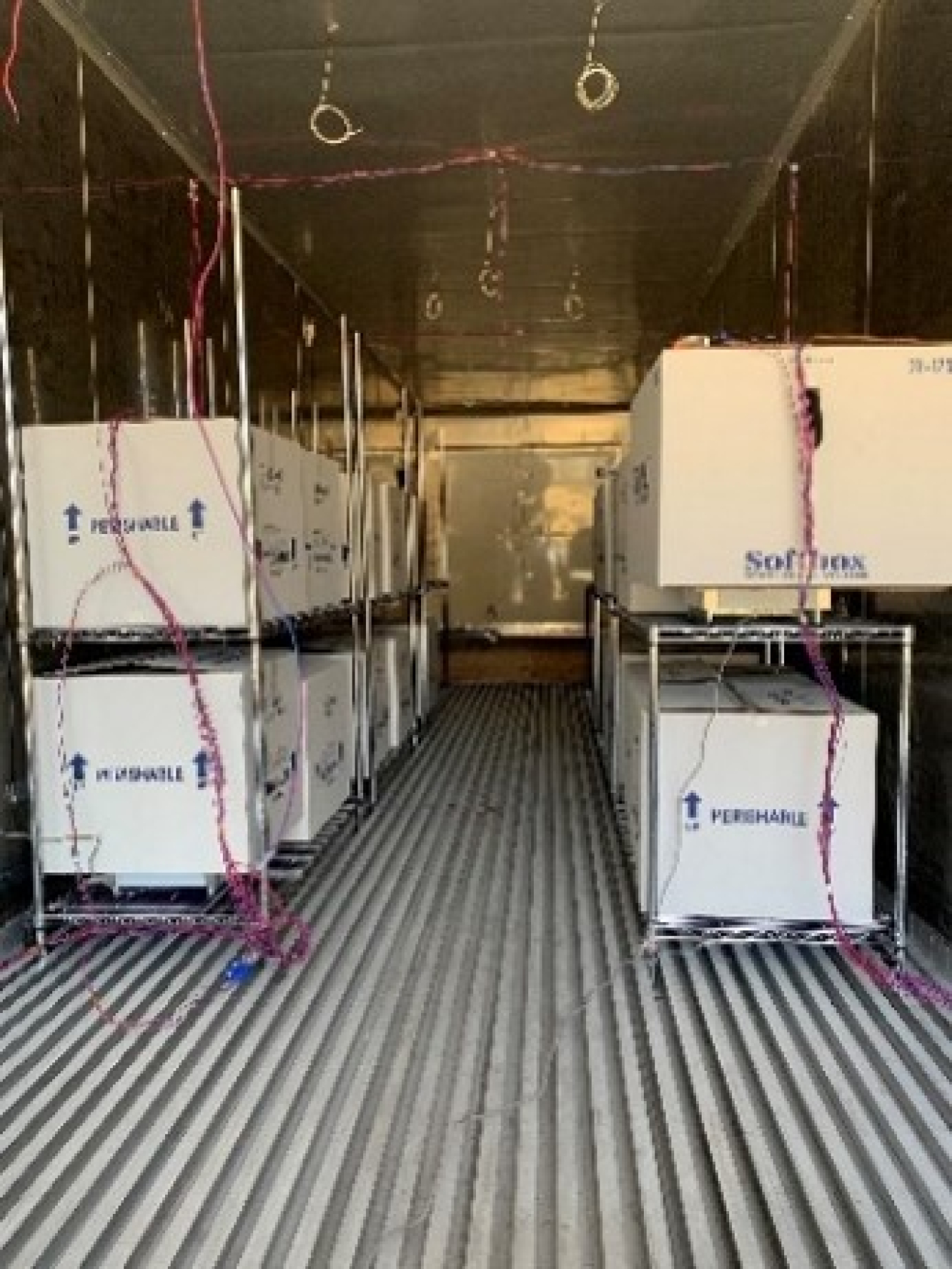
For six months, a team of ORNL researchers led by Brian Fricke and Jian Sun studied aluminum containers provided by Carrier. Founded in 1915, Carrier operates roughly 1 million of these products around the world. Carrier containers can maintain temperatures ranging from 30 to -35 degrees Celsius. The challenge for ORNL’s team was to learn whether they could extend this range to the ultra-low temperatures required to store and transport vaccine supplies without compromising the efficacy of the container.
“People had rough ideas, but nobody had the answer,” said Sun. “Simply filling a vaccine package with dry ice in a refrigerated container presented its own set of problems. It introduced safety hazards and technical challenges—particularly in the rebounding effects on the refrigeration system defrost operation, which could, in theory, impact the temperature control in the container, especially when the temperature gets very, very low. Not to mention, these are big containers, and the temperature may not be uniform inside them, which could impact the dry ice and the vaccine temperature.”
Even in ideal circumstances, a container of vaccine supplies could spend multiple days in transit across the United States. If the container arrives at a site that is ill-equipped to adequately refrigerate the delivery, handlers could be forced to store vaccine supplies in the same containers for weeks. Maintaining temperatures between -30 and -70 degrees Celsius inside the container for this length of time would require a technological breakthrough.
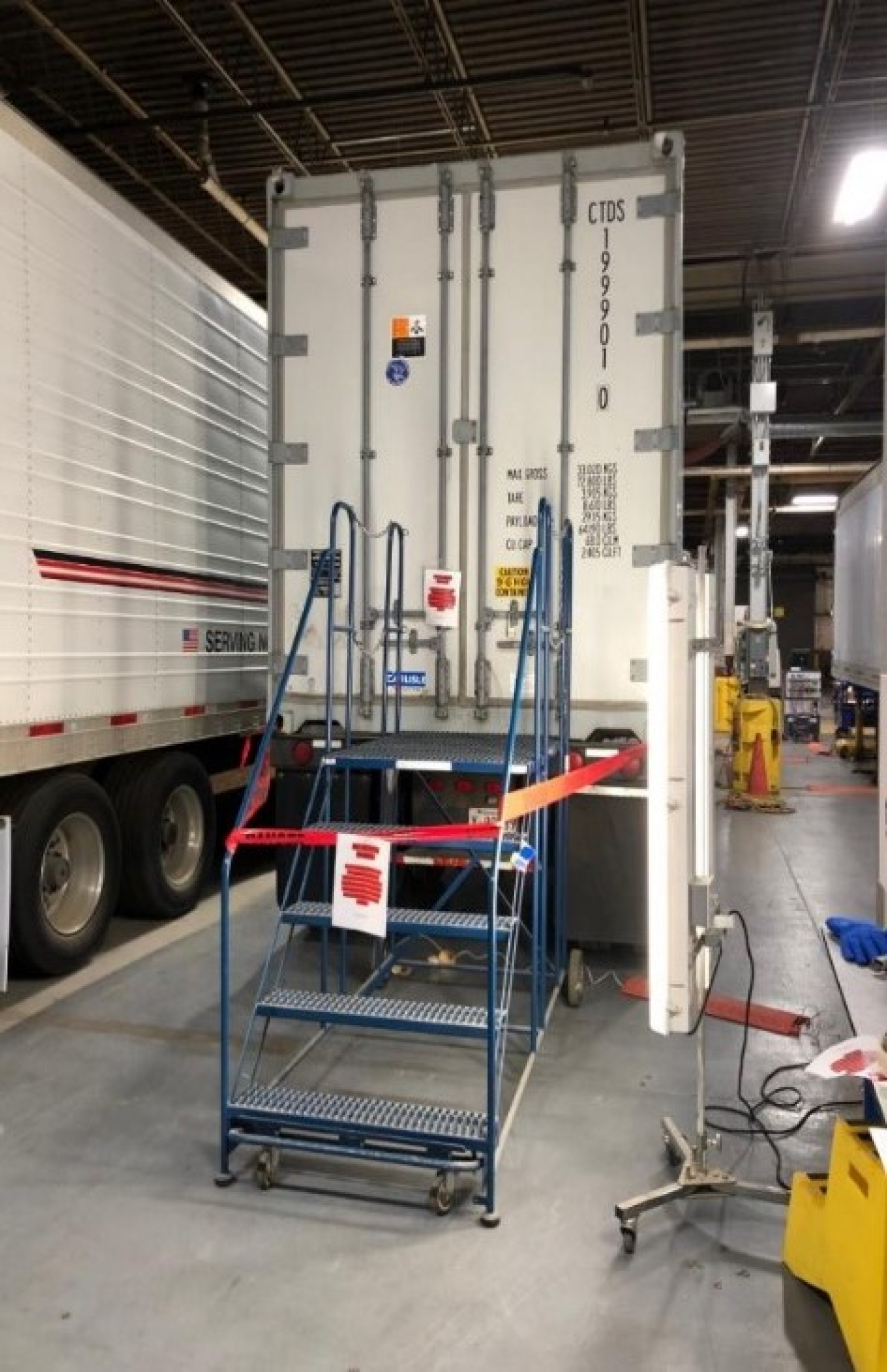
The ORNL team lab-tested two separate platforms in its attempt to achieve the lowest temperature for the longest period. This required careful evaluation of temperature distribution within the containers and the spatial arrangement of packages to calculate a thermal design optimization strategy for the indoor air temperature within the Carrier unit. The team set up instrumentation to consistently measure the temperature in the container, the package temperatures, and other useful data.
Ultimately, the ORNL team’s breakthrough took the form of an all-electric unit designed to provide precise temperature control of refrigerated container in the minus 30-to-35-degree range for maximizing the time of maintaining vaccines at required temperature. By optimizing package placements within the container (20 polystyrene foam packages, each with some 5,000 vaccines), one container is capable of carrying at least 100,000 refrigerated vaccines doses. The ORNL team’s findings will be made available through publications in two peer-reviewed journals.
This research is another example of the value of scientific creativity, critical sourcing, and timely coordination. As COVID-19 vaccines continue to proliferate around the world, the refrigeration system developed through the timely and diligent efforts of ORNL researchers will continue to keep cool.