Bioprose Blog: ORNL scientists researched the complexities of lignin structure to develop new bioadvantaged materials.
May 20, 2020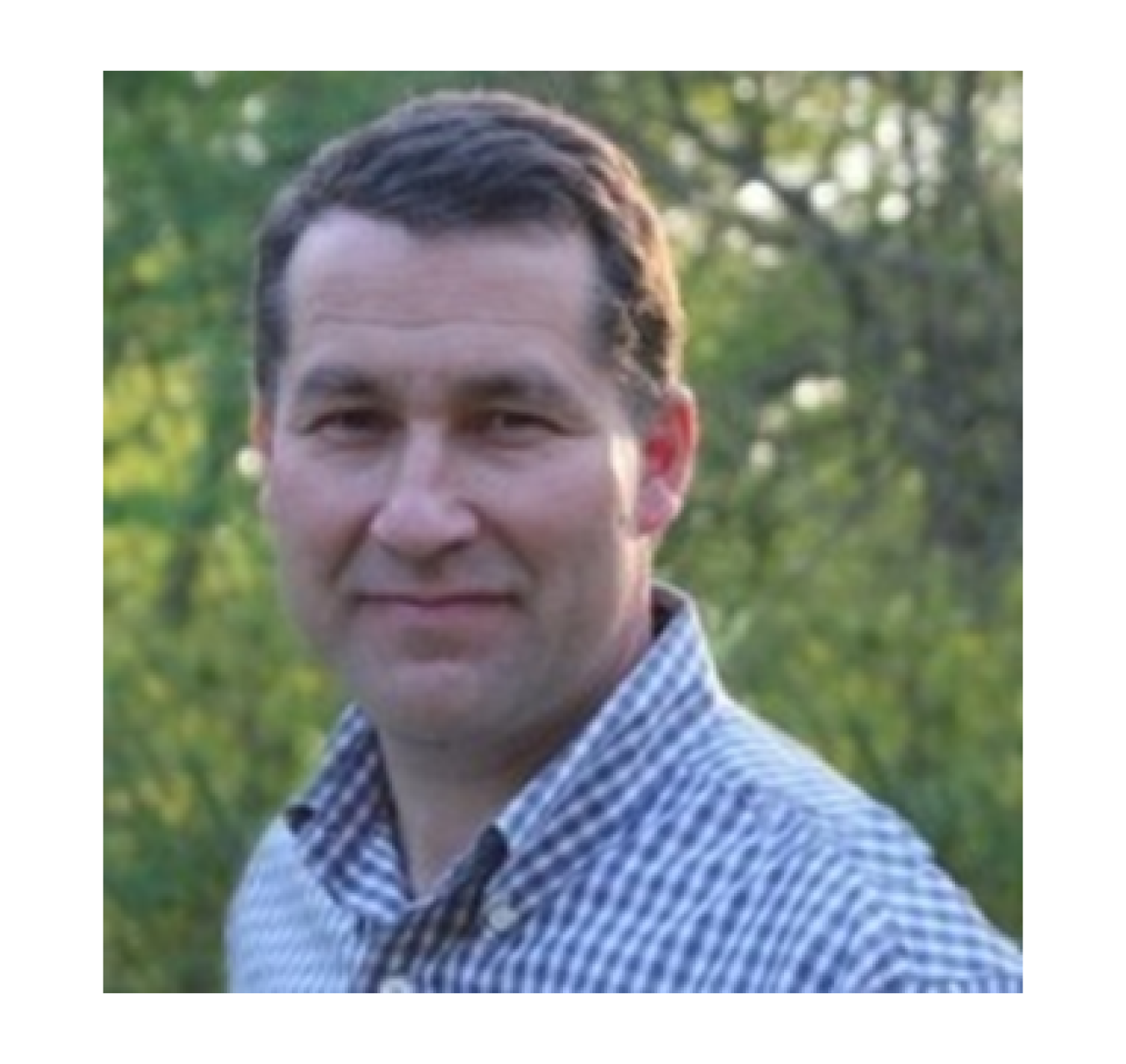
Author: Tim Theiss, Laboratory Relationship Manager, Oak Ridge National Laboratory
Read Tim's bio ►
Meet the other bloggers ►
Return to Bioprose blog ►
Bioprose Blog
ORNL Scientists Develop Plant-Based Materials to Grow Nation’s Bioeconomy
Scientists at Oak Ridge National Laboratory (ORNL) are developing new and valuable uses for lignin, a byproduct of biorefineries and the pulp and paper industry.
These new product streams can take advantage of the natural properties of lignin in biomass to create materials with unique performance advantages.
With the potential to produce a billion tons of biomass per year, the United States has vast resources to devote to production of bioenergy and bioproducts. Biomass harbors a substantial supply of lignin, a macromolecule found in the cell walls of woody plants and trees where it provides strength and rigidity.
For decades, companies have tried to use lignin—the second most abundant organic polymer in the world—as an ingredient in making new materials. But the complexity and the variability of lignin’s molecular structures has stymied most of these efforts, relegating lignin to use as a filler or as fuel to burn for heat in industrial processes.
But where others see complexity, researchers at ORNL see opportunity.
Materials scientist Amit Naskar and his team have leveraged the laboratory’s sophisticated microscopy and neutron scattering capabilities to better understand lignin structures. Their research has translated that knowledge into a series of new, bioadvantaged materials. These lignin-based inventions include:
- Composites for 3D printing
- Elastomers for coatings and glue
- Conductors for sensors and robotics
- Engineering material solutions
Renewable Composites for 3D Printing
ORNL researchers combined a melt-stable hardwood lignin with conventional plastic, low-melting nylon, and carbon fiber to create a composite with just the right characteristics for 3D printing. The composite heats up easily, flows fast for speedy extrusion through the printing nozzle, and shows significant weld strength or adhesion between layers during the printing process, as well as excellent mechanical properties.
The structural characteristics of lignin were critical to enhancing the performance of this new composite material. Scientists were able to mix in a higher percentage of lignin—40 to 50 percent by weight—than had previously been achieved for lignin-based printing material, resulting in a stronger and stiffer product.
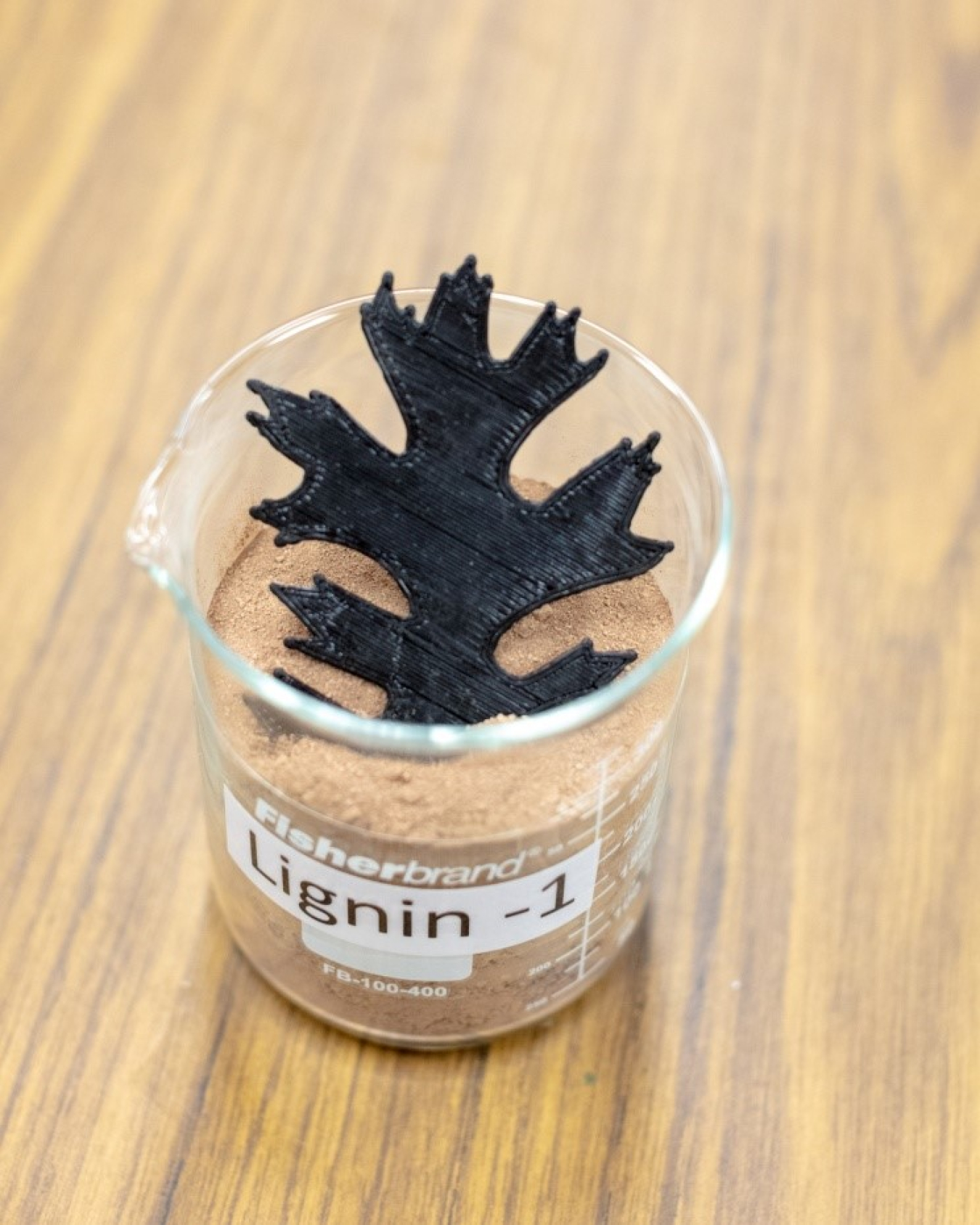
A research team at ORNL created new lignin-based composites for 3D printing. Photo credit: Carlos Jones, ORNL
Self-Healing Elastomers for Coatings and Glues
ORNL scientists developed a unique method to extract a specific form of lignin that is naturally rich in hydroxyl and carboxylic groups. Mixing this form of lignin with epoxy creates a self-healing material that can elongate up to 2,000%. The molecular structure creates a super-sticky, highly elastic material that can heal quickly, where broken, through hydrogen bonding.
This extracted lignin outperforms the adhesiveness of the natural chemical that gives mussels the ability to stick to rocks and ships. The new material shows promise to replace dopamine in a range of industrial applications including coatings, glues, and hydrogels.
Shape-Memory Conductors for Sensors and Robotics
Naskar and his team developed a solvent-free process that mixes rubber with lignin to make a renewable material programmed to remember its shape. The method includes stretching or curling the material and then freezing it to program the material to return to its intended shape, which occurs after the application of a little heat. Adding a thin layer of nanoparticles activates electrical conductivity, creating a low-cost alternative to conventional conductors for applications in sensors and robotics.
The performance of the polymer can be tailored further by using variations of lignin or different ratios and by including small quantities of salt additives. The amount and type of lignin determines the material’s pliability.
Engineering Material Solutions
From tougher plastics made with 50% renewable content to elastomers, surfactants, and composites, Naskar and his team are continually creating new uses for lignin. They have patented 15 inventions so far, with multiple companies licensing four of the materials and methods.
Prisma Renewable Composites, for instance, is using several of those inventions to engineer material solutions. According to CEO Adam McCall, working with Naskar as well as colleagues at the University of Tennessee has enabled Prisma to produce renewable, low-cost, high-performance materials for a wide range of applications.
With commercialization by industry and continued support from the U.S. Department of Energy’s Bioenergy Technologies Office, researchers at ORNL will keep exploring the many facets of lignin and the value it brings to the bioeconomy.
For more information on ORNL’s lignin work and collaboration with Prisma Renewable Composites, check out this video.
Tim Theiss
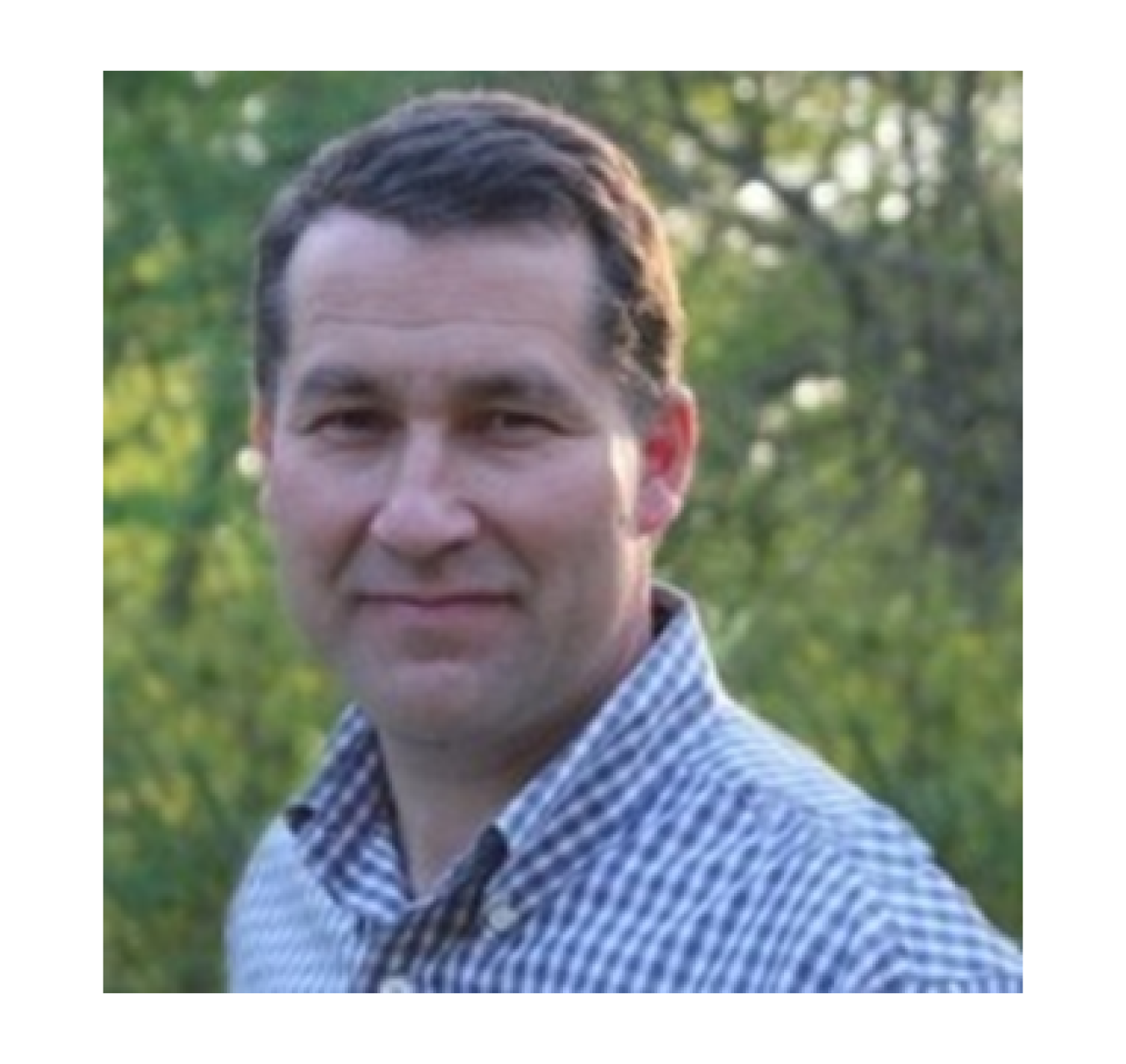
Tim has been on the staff at Oak Ridge National Laboratory (ORNL) since 1987 as a research development staff member, a program manager, and a group leader. He has over 20 years of experience in program development and program management at ORNL in various technical areas, primarily related to bioenergy and biofuels, power systems, and reciprocating engine-based power generation.
Since October 2011, Tim has been serving as the laboratory relationship manager or program manager for the U.S. Department of Energy (DOE) Office of Energy Efficiency and Renewable Energy’s Bioenergy Technologies Office. This applied bioenergy program includes research on feedstock supply and logistics, biomass conversion technologies, and the strategic analysis and viability of bioenergy.
From 2008 to 2012, Tim led ORNL’s Fuels and Engines Research Group, one of the larger comprehensive internal combustion engine research and development groups in the DOE system. He has a master’s degree in engineering mechanics from Virginia Tech and a bachelor’s degree in engineering science and mechanics from Tennessee Tech.
Meet our other bloggers ►
Return to Bioprose blog ►