Although cars have been around for more than a century, the material making them up has mostly stayed the same — steel. It’s only been in the l...
Office of Energy Efficiency & Renewable Energy
August 25, 2016Why Lightweight Materials Matter
Cars play a big part in our lives. They transport our kids to school, help grab the groceries, and even give us a lift home from a late night out on the town. That’s why it’s so important to maximize what these vehicles can do — especially when it comes to fuel economy.
Nearly one-third of U.S. carbon pollution comes from our transportation system. By reducing a car’s weight, we can cut down on oil consumption, combat climate change and extend the range of our cars. Did you know that a 10 percent reduction in vehicle weight can lead to an 8 percent improvement in fuel economy? Now you do!
Although cars have been around for more than a century, the material making them up has mostly stayed the same — steel. It’s only been in the last 25 years or so that advanced materials, ranging from aluminum and magnesium alloys to carbon fiber composites, have made their way into mass-produced passenger cars. These lightweight materials can cut a vehicle’s body and chassis weight in half, helping to increase fuel economy as well as the overall range of hybrids, plug-ins and all-electric cars.
Take the Ford F-150, for example. The world’s top-selling truck switched to an all-aluminum body and bed for its 2015 model and is now 700 pounds lighter than before. In addition, lightweight materials also allow cars to carry additional advanced emission control systems, safety devices, and integrated electronic systems without sacrificing performance.
The Vehicle Technologies Office (VTO), within the Office of Energy Efficiency and Renewable Energy, works with industry, the national labs and academia to improve these materials. Although all of them show promise in reducing vehicle weight, there are pros and cons to each advanced material, ranging from production costs to property deficiencies.
Pros and Cons of Advanced Lightweighting Materials
Magnesium (Mg)
Description: With the lowest density of all structural metals, magnesium alloys have the potential to reduce component weight up to 70 percent. Magnesium is presently used as castings for powertrains or sub-assembly closures. The increased use of magnesium for automotive applications is limited by several technical challenges.
Pros: High stiffness and strength, compatible with existing infrastructure for stamping.
Cons: Expensive, lack of availability from U.S. manufacturers in large quantities to meet automotive needs. Other challenges include ductility, joining and corrosion. Rare earth additives may also be needed to improve energy absorption to meet crash requirements by automotive markets.
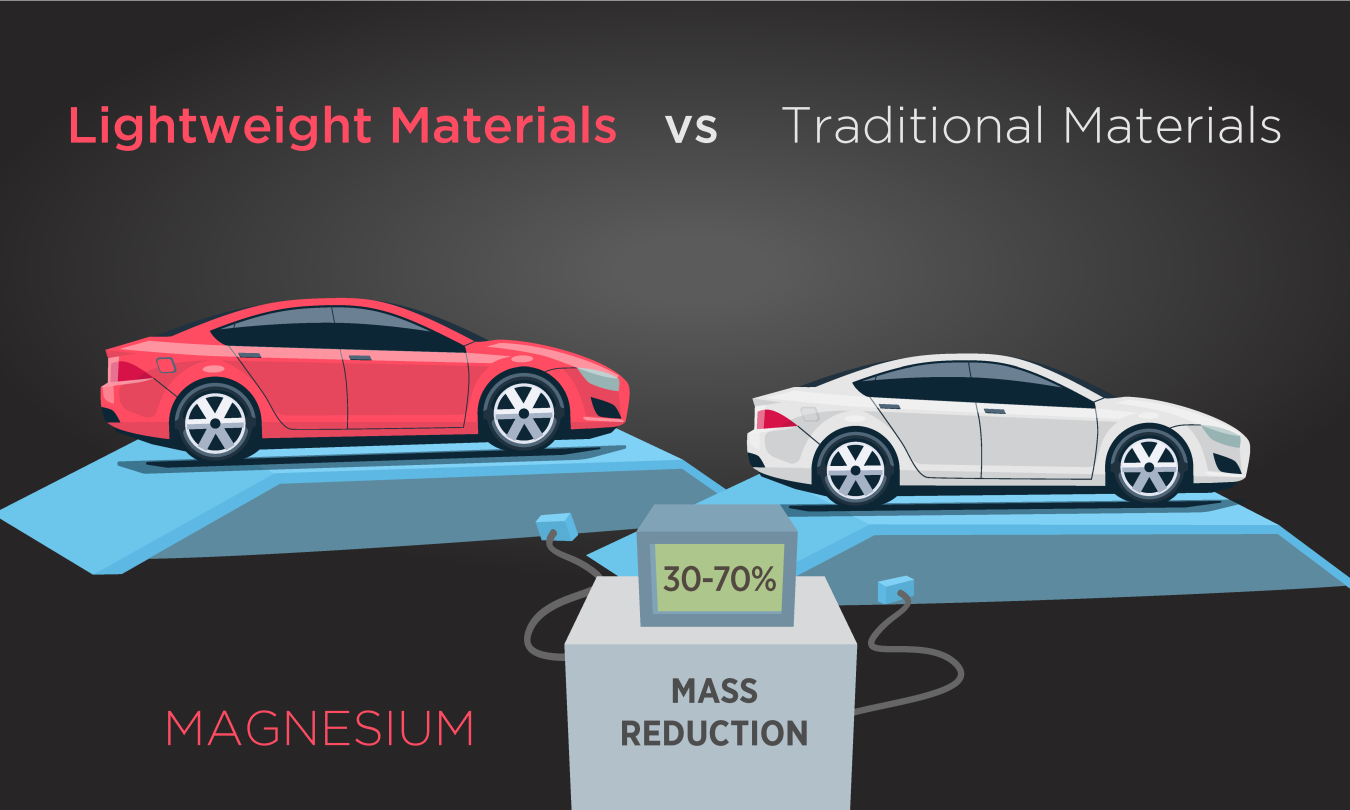
Carbon Fiber Composites
Description: Despite being half the weight of steel, carbon fiber composites are four times stronger and have the potential to reduce vehicle weight by up to 70 percent.
Pros: High stiffness, high strength, enables the manufacture of highly complex shapes, and offers tremendous weight savings.
Cons: High production cost of carbon fiber, difficulty joining into vehicles, along with associated challenges in modeling performance, infrastructure, and sufficient amounts of fiber to meet automotive needs.
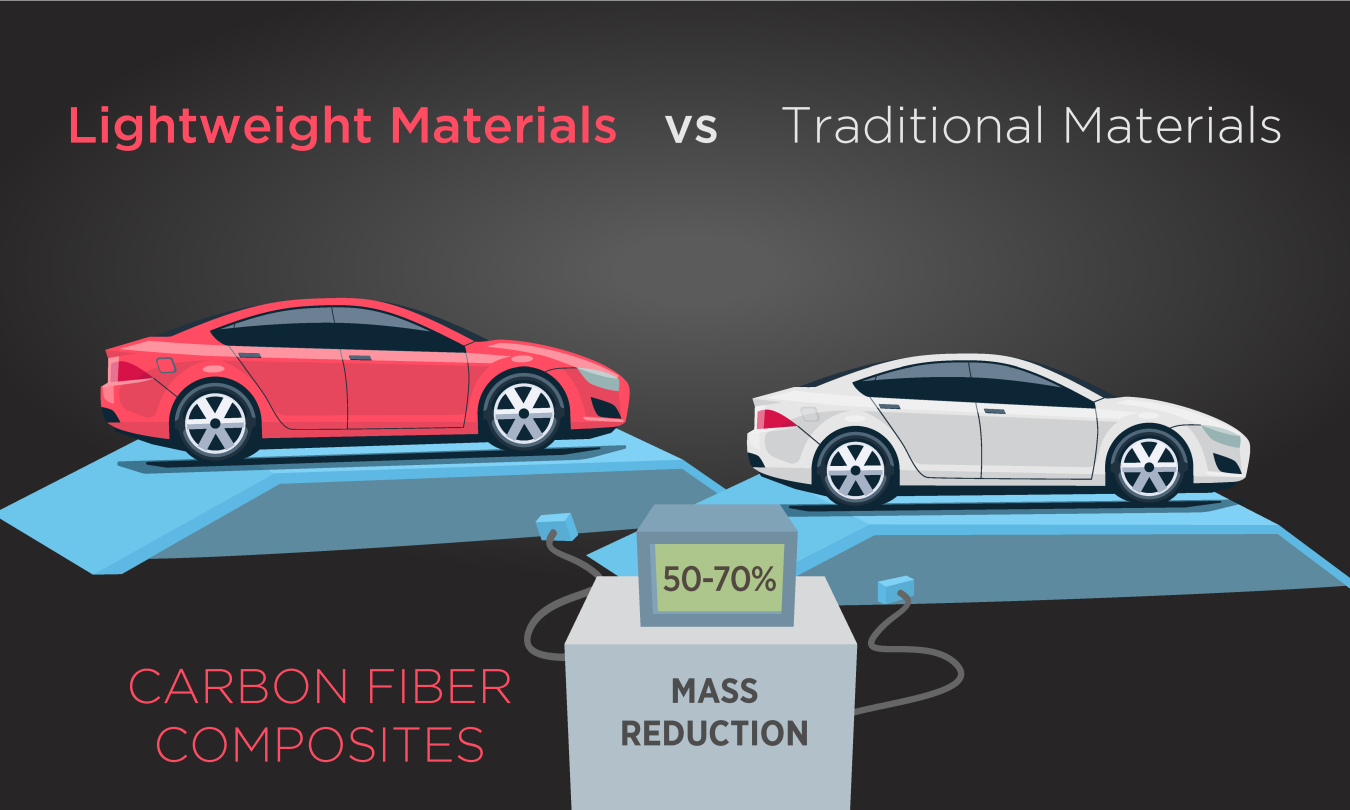
Aluminum
Description: A lighter, more expensive alternative to steel, aluminum is increasingly being utilized for hoods, trunk lids, and doors and has the potential to reduce weight by up to 60 percent.
Pros: Technology is fairly mature, good stiffness, strength and energy absorption.
Cons: Higher cost than steel, joining to other materials, and limited formability issues.
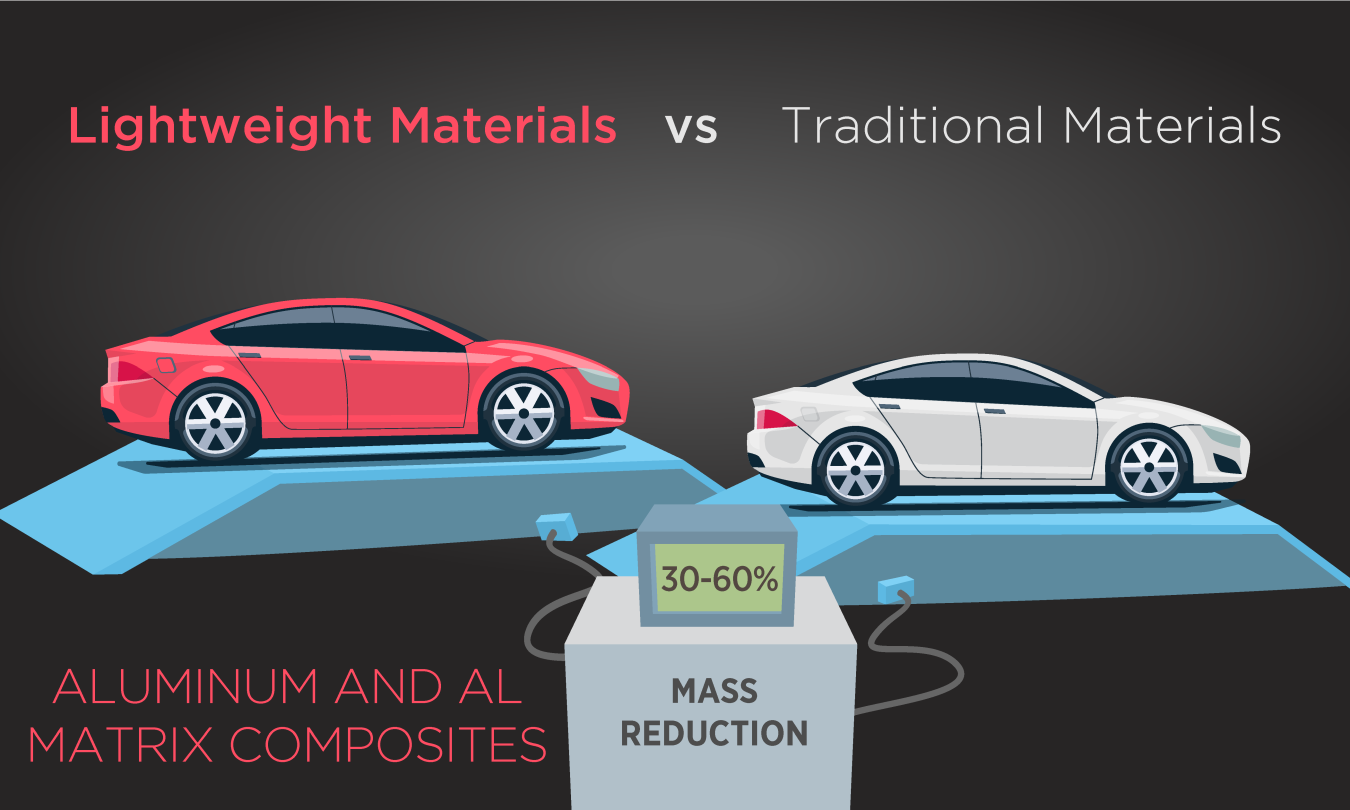
Titanium
Description: High temperature metals used in powertrain systems that can reduce weight by up to 55 percent.
Pros: High strength to weight ratio, can withstand high temperatures.
Cons: High cost of materials, formability challenges.
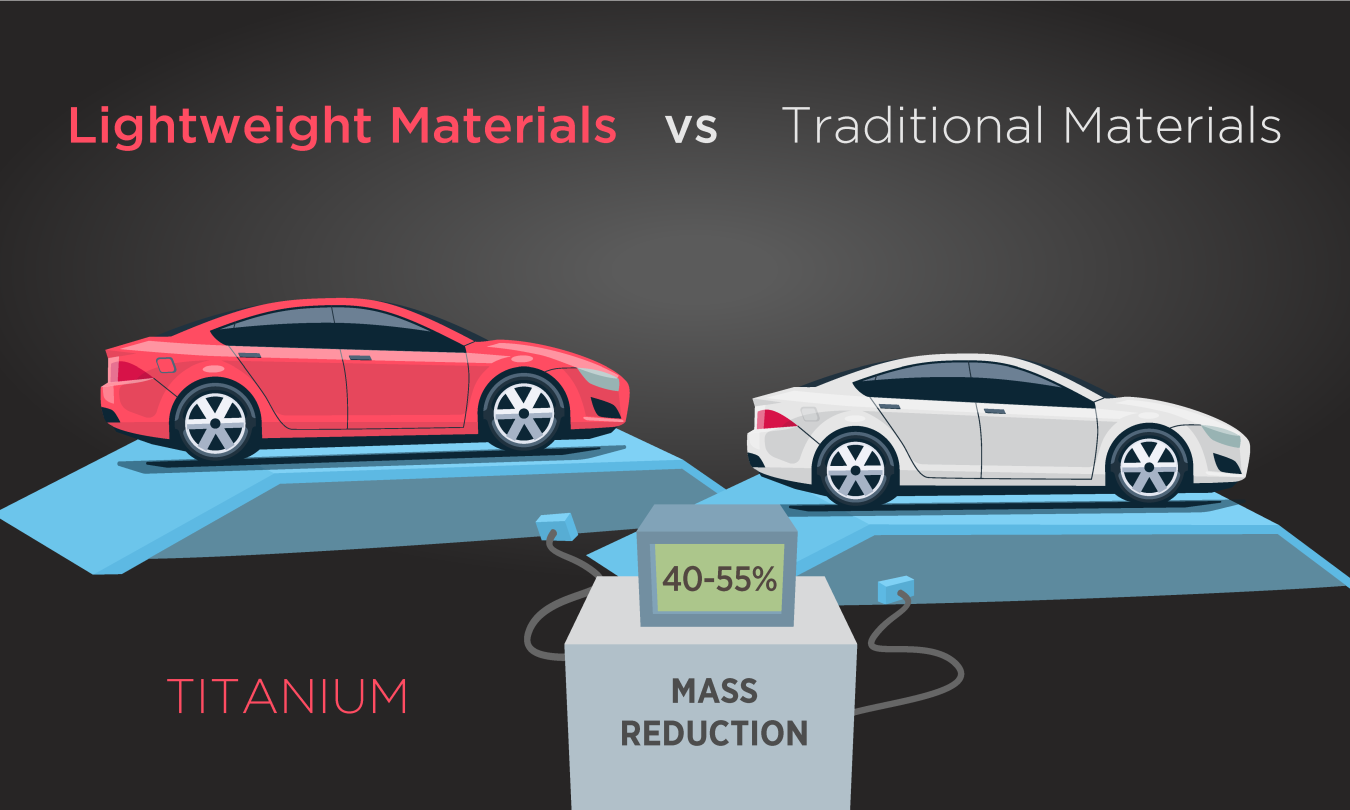
Advanced High Strength Steel (AHSS)
Description: Higher performance family of steels that enable greater weight reduction. AHSS has the potential to reduce component weight by up to 25 percent, particularly in strength-limited designs such as pillars and door rings.
Pros: High strength, stiffness and formability, corrosion performance, low cost.
Cons: Cost, wears out stamping molds faster than for lesser grades. Ductility decreases as strength increases adding issues in forming and joining. Challenges also include design, component processing, and behavior in harsh environments.
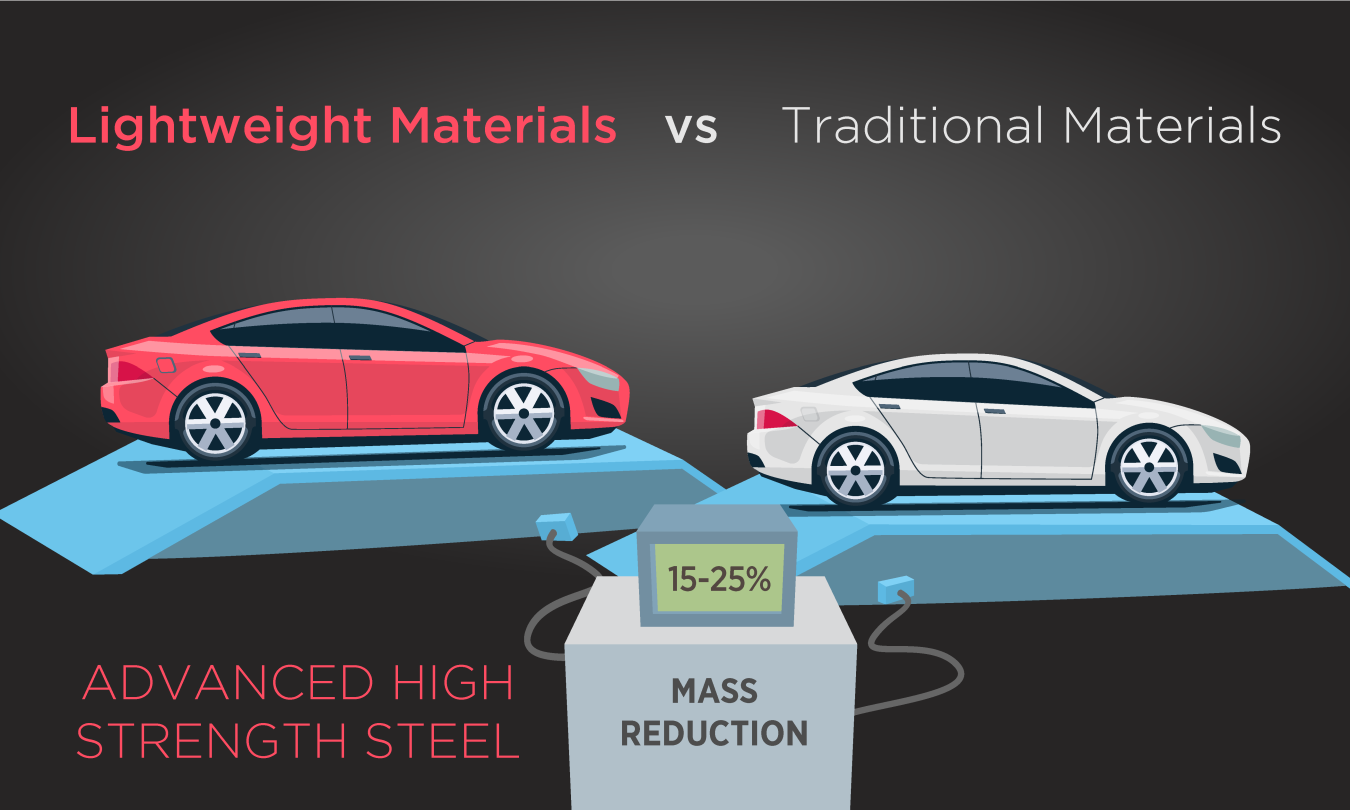
VTO invests in research and technologies to spur the development of lightweight materials for passenger and commercial vehicles through the use of computation materials science. In addition, the office also collaborates with industry leaders through partnerships like U.S. DRIVE and 21st Century Truck. Learn more about its lightweighting efforts through the Energy Materials Network — a program that supports the president’s Materials Genome Initiative to reduce the time it takes to accelerate the deployment of advanced materials to the marketplace.
What are the key facts?
- By reducing a car’s weight, we can cut down on oil consumption, combat climate change and extend the range of our cars.
- A 10 percent reduction in vehicle weight can lead to an 8 percent improvement in fuel economy.
- Lightweight materials can cut a vehicle’s body and chassis weight in half—helping to increase fuel economy as well as the overall range of hybrids, plug-ins and all-electric cars.
- Lightweight materials also allow cars to carry additional advanced emission control systems, safety devices and integrated electronic systems without sacrificing performance.
- VTO invests in research and technologies to spur the development of lightweight materials for passenger and commercial vehicles through the use of computation materials science.