A national lab technology that improves power plant carbon capture could also save money and energy for micobreweries.
Office of Energy Efficiency & Renewable Energy
June 13, 2017By Erik Hyrkas, a former EERE Communications team member
Could a national lab technology that improves power plant carbon capture also help other carbon dioxide (CO2)-emitting industries save energy and money? Colorado microbrewery owners think so.
Craft beer is a booming business in the United States. The number of craft breweries operating since 2009 has grown from nearly 1,600 to more than 5,200.
CO2 is a critical element for craft breweries, needed for both carbonization of the beer and final packaging. It's also a byproduct of the fermentation process. Every brewery, no matter its size, produces three times as much CO2 as is needed during the fermentation process. Companies with large operations often have CO2 recovery systems, like those currently used at power plants. But many microbreweries don't have the ability to capture and recycle the gas back into their operations. Because of this, the CO2 already produced is wasted, and small breweries must purchase additional CO2 from local suppliers, to meet their CO2 needs.
Unfortunately, transporting the CO2 from local suppliers is 80% of the cost. If smaller breweries had a way to capture their own gas and recycle or sell it, they could save up to 75% of that expense, increasing efficiency, saving money, ultimately making them more competitive.
From Power Plants to the Brew House
A group of researchers from Lawrence Livermore National Laboratory (LLNL) are using their microcapsule technology to help craft breweries potentially harness these savings.
This national lab technology, initially designed to capture carbon from power plants, uses microcapsules made of gas-permeable polymer shells. Those shells contain the base ingredient (sodium carbonate) of a popular household cleaning product—baking soda—to better absorb and react with carbon dioxide. The microcapsules are then suspended on a mesh structure to allow CO2 to move in and out of the shells—absorbing carbon dioxide about 10 times faster than encapsulated chemicals.
Watch as LLNL researchers talk about adapting their technology to craft beer making.
The idea that an improved power plant carbon capture technology, originally developed with support from the Office of Fossil Energy, could help other CO2-emitting industries wasn’t immediately clear to the LLNL research team. However industry engagements enabled by the Department of Energy’s Energy I-Corps program introduced the research team, MECS (Micro-Encapsulated CO2 Sorbents), to other viable markets for the national lab-developed technology.
“As we moved through the trainings and the customer interview sessions [during Energy I-Corps], we talked to different customers finding their pain points,” said Congwang Ye, the principal investigator of the MECS team. “We realized there was a market need for carbon capture beyond just power plants. Capturing CO2 from microbreweries during the fermentation process was one of those surprising needs.”
Through Energy I-Corps, the team also uncovered potential ways to transition their technology to this new market. One idea is to set up a simple system at a brewery that will capture carbon dioxide, bring it to a centralized hub operated by MECS to reclaim the CO2, and then redistribute it back into the market at a much lower rate than current CO2 distributers.
If successful, the process could potentially save breweries tens of thousands of dollars a year and prevent millions of pounds of CO2 produced during fermentation from escaping into the atmosphere.
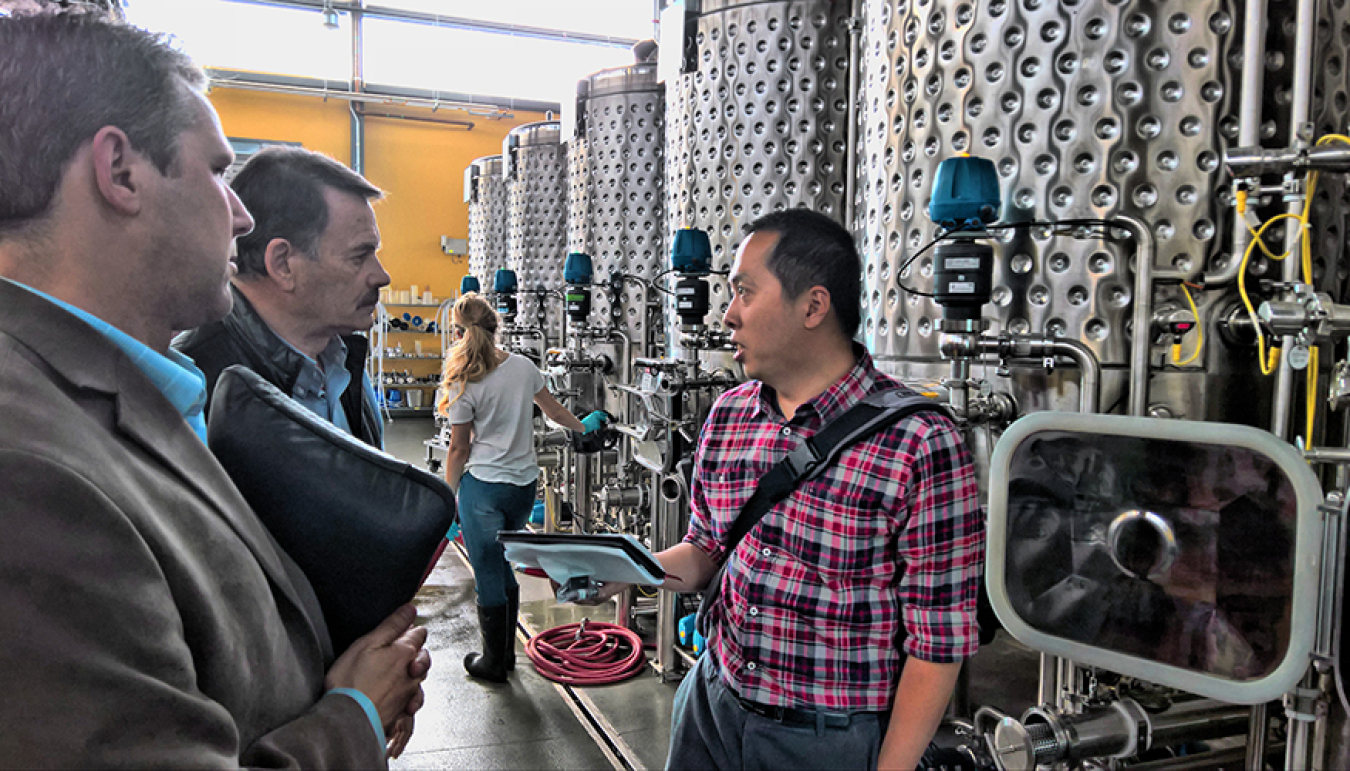
LLNL researcher Congwang Ye (right) visits with professors at UC Davis to see their pilot-scale winery and brewery and learn about fermentation tank operations.
For initial proof-of-concept, Ye’s team intends to install a carbon capture system at the University of California, Davis’ pilot winery and brewery. The team is also looking to further refine its research by performing more fermentation-related carbon capture studies.
“We would like to mature the idea with early evangelists and small breweries, so that we can eventually utilize it at the regional breweries, power plants, and other carbon emission sources.” Ye adds.
Energy I-Corps is administered by the Office of Energy Efficiency and Renewable Energy’s Technology-to-Market program. To learn more about Energy I-Corps and the MECS project visit the Energy I-Corps team website.