DOE partners with private companies and other organizations to develop unique approaches to improving building energy efficiency
Office of Energy Efficiency & Renewable Energy
April 19, 2023Today, U.S. homes and commercial buildings consume 39% of the country’s total energy, and to bring this number down, the Department of Energy (DOE) partners with private companies and other organizations to develop unique approaches to improving building energy efficiency. One such company is Hempitecture Inc, a company spun out from years of competitively earned DOE mentorship, that produces industrial hemp for use in buildings as insulation.
Hempitecture was founded in 2018 by current CEO Matthew Mead and Co-Founder Tommy Gibbons to replace synthetic insulation materials with plant-based resources. Hempitecture’s debut products, HempWool and HempCrete, are both biobased thermal insulation products that Hempitecture sells to construction companies and contractors to build and retrofit residential and commercial buildings with lower carbon footprints. Hempitecture has now completed over 20 hemp insulation projects, ranging from small buildings to more intricate projects.
“Hempitecture's partners within DOE and its Building Technologies Office have helped us evaluate and improve our product performance while accounting for greenhouse gas emissions and providing resources to commercialize the product to reach a nationwide scale of deployment,” said Hempitecture Cofounder Tommy Gibbons.
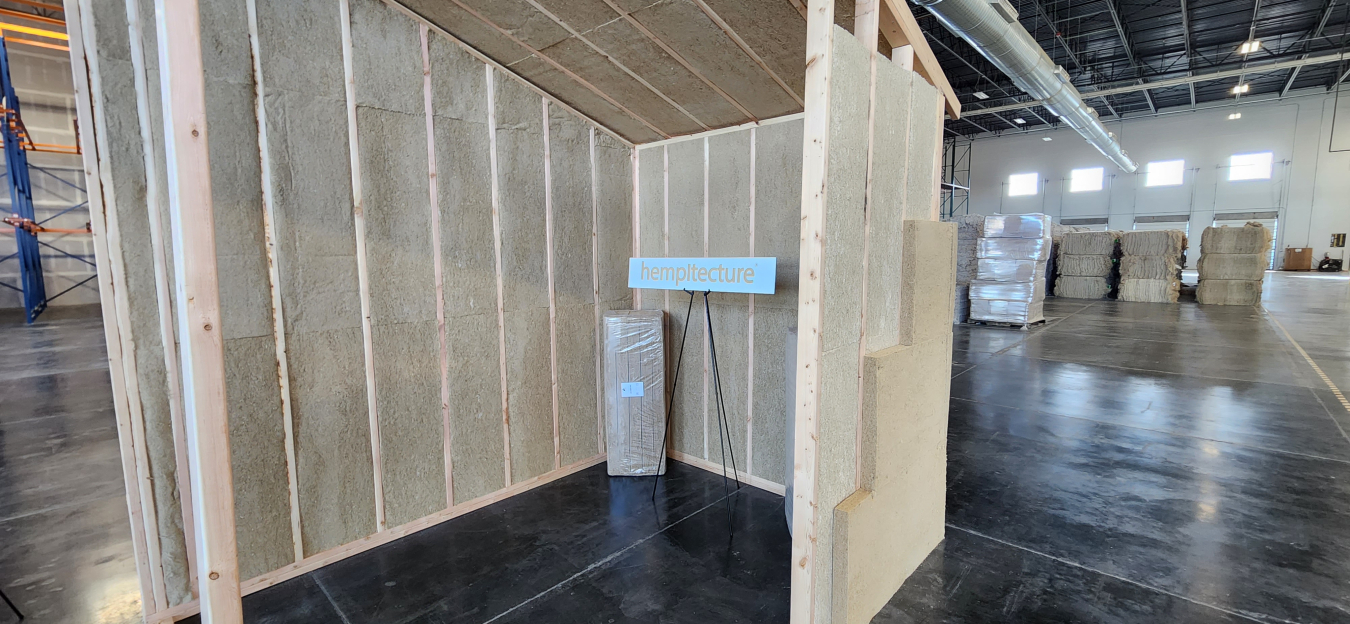
HempWool insulation.
In 2021, Tommy refined his hemp-based insulation concept as BTO’s first-ever Lab-Embedded Entrepreneurship Program (LEEP) fellow in Oak Ridge National Laboratory’s (ORNL) Innovation Crossroads team. Later in 2021, his Idaho-based company earned a competitively awarded Cooperative Research and Development Agreement (CRADA) from ORNL with Building Technology Office (BTO) funding, which brought expertise from ORNL and Argonne National Laboratory (ANL) to test, evaluate, and optimize Hempitecture’s prototype designs further in preparation for commercialization. Hempitecture was also competitively selected to join the 2021 cohort of BTO’s IMPEL+ (Incubating Market-Propelled Entrepreneurial Mindsets at the Labs and Beyond) at Lawrence Berkeley National Laboratory, a rapid innovation and deployment engine that helps early-stage innovators bring their technologies to market with business model and pitch trainings, access to private funding pipelines, and additional mentorship. Together, these three funding mechanisms gave Hempitecture access to four national labs to develop a sustainable and successful hemp-based insulation product that can increase building energy efficiency.
Testing at ORNL indeed showed a noticeable energy and humidity benefit from the HempWool versus traditional fiberglass insulation. This is due to HempWool’s higher density and better ability to absorb, store, and release heat while resisting heat transfer. This heat buffering effect lowers the home’s energy use when controlling indoor temperatures. HempWool’s ability to hold moisture also allows it to protect the integrity of wooden walls, as the testing at ORNL showed, there was more moisture on the wall using fiberglass insulation than the wall using hemp insulation.

Hempitecture’s first manufacturing facility ribbon cutting.
Hempitecture just opened its first manufacturing facility in the United States in February with a ribbon cutting ceremony that included BTO’s technology manager for building envelopes, Sven Mumme, and Nicholas Ryan, manager of BTO’s Technology to Market program. At this facility, Hempitecture will produce nonwoven materials composed of hemp fiber, which is able to create a wide range of products, including HempWool. Additionally, Hempitecture will utilize its nonwoven manufacturing technologies to produce sustainable liners for cold freight partners while using compostable packaging and pallet racks to reduce its own use of plastics in the manufacturing process. The hemp used for production in this facility is sourced locally from Hempitecture’s partner, IND Hemp, which is only roughly 60 miles from the facility, reducing Hempitecture’s carbon impact from transportation.
“The opening of Hempitecture's Jerome, Idaho facility marks an important milestone in Hempitecture's goal to bring high performing, carbon smart insulation to the United States. This goal of decarbonizing insulation has come into focus across the DOE as the emphasis on a building’s embodied carbon footprint matches the importance of a building's operational carbon performance,” said Gibbons.
At the event, Rudy Soto, the U.S. Department of Agriculture’s State Director for rural development in Idaho also highlighted the value of harnessing rural agriculture for manufacturing industries like insulation and how important resilient, healthy, and equitable rural housing infrastructure is.
“Hempitecture's new hemp manufacturing facility in Jerome is a testament to the power of harnessing rural agriculture for manufacturing industries. Not only will it create jobs and stimulate economic growth for the Magic Valley, but it also highlights the value of sustainable and resilient building materials. As we strive for healthier and more equitable housing infrastructure, it’s crucial that we prioritize using natural and renewable resources like hemp to reduce our carbon footprint and support local farmers. This facility represents a brighter and more prosperous future for Jerome and rural Idaho, where we can build stronger communities by preserving and leveraging the power of agriculture and sustainability to benefit current and future generations.”
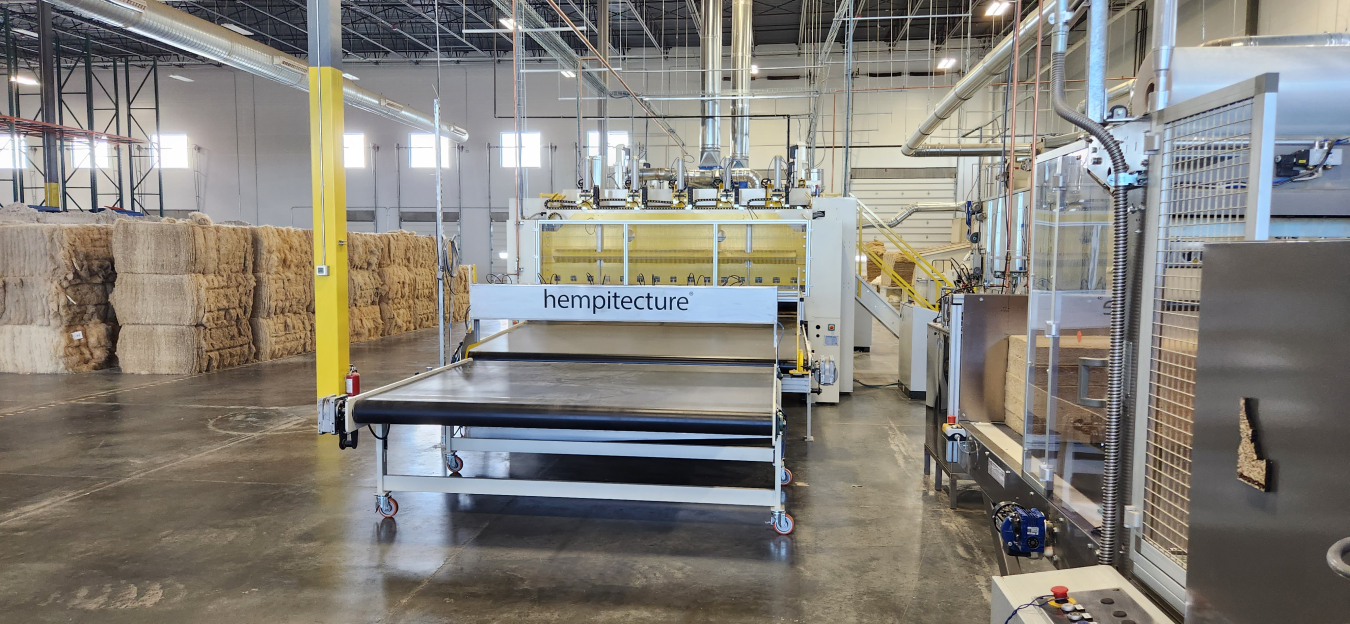
Hempitecture manufacturing facility.
Hempitecture’s new facility now enables its industrial hemp products to be produced entirely in the United States. The success of this company, from prototype to full-scale production, incentivizes the continuation of DOE competitive partnerships with private companies to encourage the development of unique approaches for improving building energy efficiency.
“For novel insulation materials to succeed commercially, or in this case, to ensure hemp is accepted as a viable insulation material once it’s reintroduced to buildings across the country, the public and private sectors must partner, pool their resources, and sustain that partnership over many years and funding cycles,” said Sven Mumme, Acting Program Manager of BTO’s Emerging Technologies program and technology manager of its Opaque Envelope and Thermal Energy Storage research portfolio. “Hempitecture is here today because DOE’s incubators helped them move their concept from drawing boards to board rooms through every stage of the R&D process through numerous competitive funding cycles. Hempitecture’s success, made evident by their new factory, is a testament to the rising demand we’re seeing for more sustainable building materials across the country that are as effective or even better than conventional technology.”