You wouldn't think an energy-intensive operation like the Scranton Army Ammunition plant would be determined to become as energy efficient as possi...
Advanced Manufacturing & Industrial Decarbonization
October 11, 2013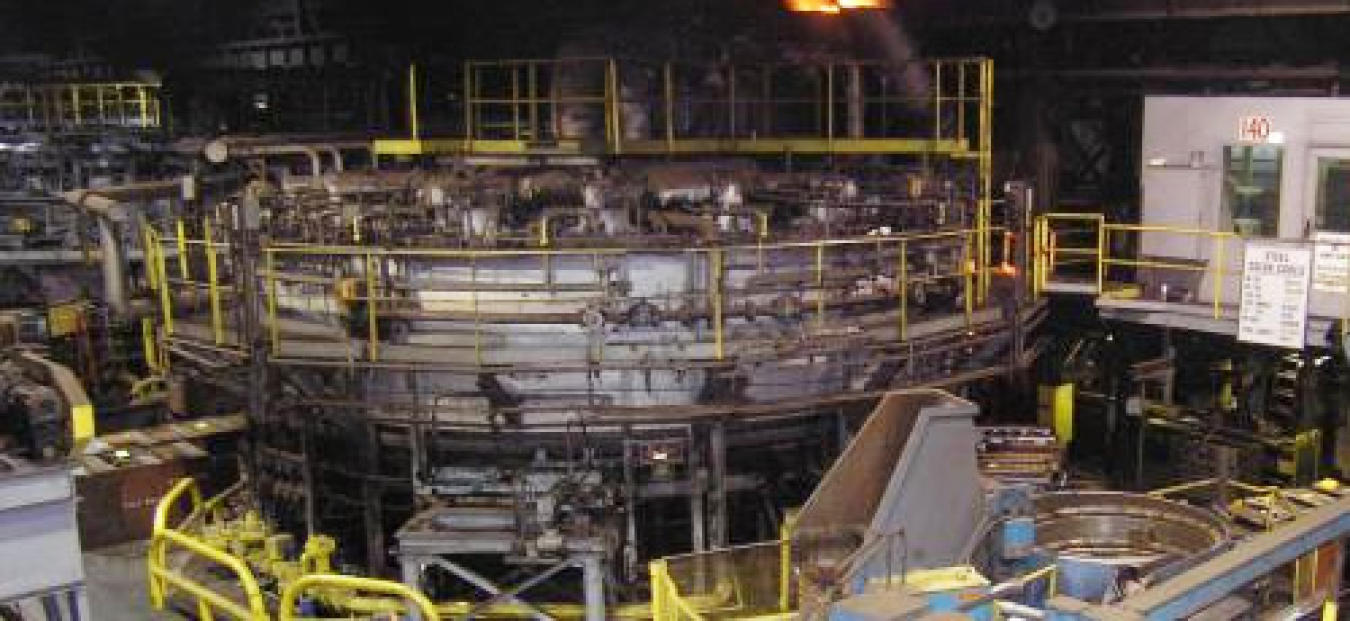
General Dynamics' Bliss Three Forge Furnace is a natural gas-fired rotary hearth furnace used to heat steel before forging. Refurbished with a new high performance refractory, high efficiency burner controls, and natural gas recuperators, the furnace improvements translated into a 25% reduction in natural gas consumption. Photo credit: General Dynamics.
You wouldn't think an energy-intensive operation like the Scranton Army Ammunition plant would be determined to become as energy efficient as possible, would you? But its Operating Contractor, General Dynamics Ordnance and Tactical Systems, is demonstrating its leadership in how U.S. manufacturers will operate in the future clean energy economy and is leading the way for U.S. Army contracting facilities to do just that. How? Through Superior Energy Performance (SEP) certification—a new business-based, internationally-recognized energy management implementation and certification process. With SEP, the Pennsylvania facility was able to improve its energy performance by almost 12%.
By using the globally recognized ISO 50001 energy management standard, as well as DOE measurement and verification tools that confirm energy performance improvements, SEP helped the Scranton facility integrate new forward-thinking processes into their business operations and create a rigorous energy management system.
Stephen Cannizzaro, Environmental Engineer at General Dynamics, and AMO's Paul Scheihing who leads the SEP program, recently discussed the benefits that the Scranton facility has discovered through SEP certification. Paul pointed out that what General Dynamics is doing is very important because the facility went out of their way to surpass typical energy efficiency implementation efforts. General Dynamics already had a foundation for using DOE resources—they've received two DOE-sponsored energy assessments in the past, "but now the SEP process was able to boost their energy efficiency to a much higher level of energy savings."
General Dynamics also used SEP to model energy intensity within the plant, as well as specific manufacturing processes, such as the plant's steam generation process. This allowed plant managers to analyze energy data around the plant's steam generation system in order to justify new and more energy efficient boilers. Steve explained, "With the SEP system in place, management is much more receptive to capital improvement proposals, and it is easier to defend new projects. SEP brought to light many energy intensity savings opportunities that were previously hard to identify and justify."
"ISO 50001 also provides the Scranton facility with an effective plan and framework to manage energy-intensive operations," Paul explained.
Overall, in the first year General Dynamics was able to identify an impressive $536,000 in savings, with a payback period of just six months. The facility implemented operational and management processes—weekend shutdowns, coordinated production schedules, employee cooperative programs, and cooling tower temperature set points—that had a significant impact on Scranton's energy performance.
Even though the Department of Defense requires ISO 14001, the international environmental management system standard that contains some energy-related components, Steve advises that other manufacturing facility managers also use SEP and ISO 50001 to get the most comprehensive energy results possible—"Do not just do the minimum to become more energy efficient; as you start to think about pushing outside ‘the box,' SEP can generate bigger energy savings than you first imagined."
DOE's Office of Energy Efficiency and Renewable Energy partnered with the U.S. Council for Energy-Efficient Manufacturing to develop SEP. Learn more by visiting the SEP program website.
<p><em>"We want to congratulate General Dynamics in Scranton, Pennsylvania for their hard work and leadership in improving energy performance by nearly 12%. They are the first Defense Department facility to receive a Superior Energy Performance certification."</em><br /><br /><strong>- Robert Ivester, Acting Director, DOE Advanced Manufacturing Office</strong></p>
<p><em>What is SEP?</em></p><ul><li><em>SEP is a comprehensive energy management system for industrial and commercial facilities.</em></li><li><em>SEP is based on a measurement and verification protocol for continual energy efficiency improvements.</em></li><li><em>SEP uses ISO 50001 – an energy management system standard – to increase energy efficiency, reduce costs, and improve environmental performance.</em></li><li><em>SEP can be used to set performance targets and quantify improvements at facilities that have adopted the ISO 50001 standard.</em></li><li><em>SEP uses a third party verification process to provide credible data for company management and external stakeholders.</em></li></ul>