On June 8, 2018, Secretary of Energy Rick Perry traveled to Oak Ridge National Laboratory (ORNL) to dedicate Summit...
Advanced Manufacturing & Industrial Decarbonization
June 28, 2018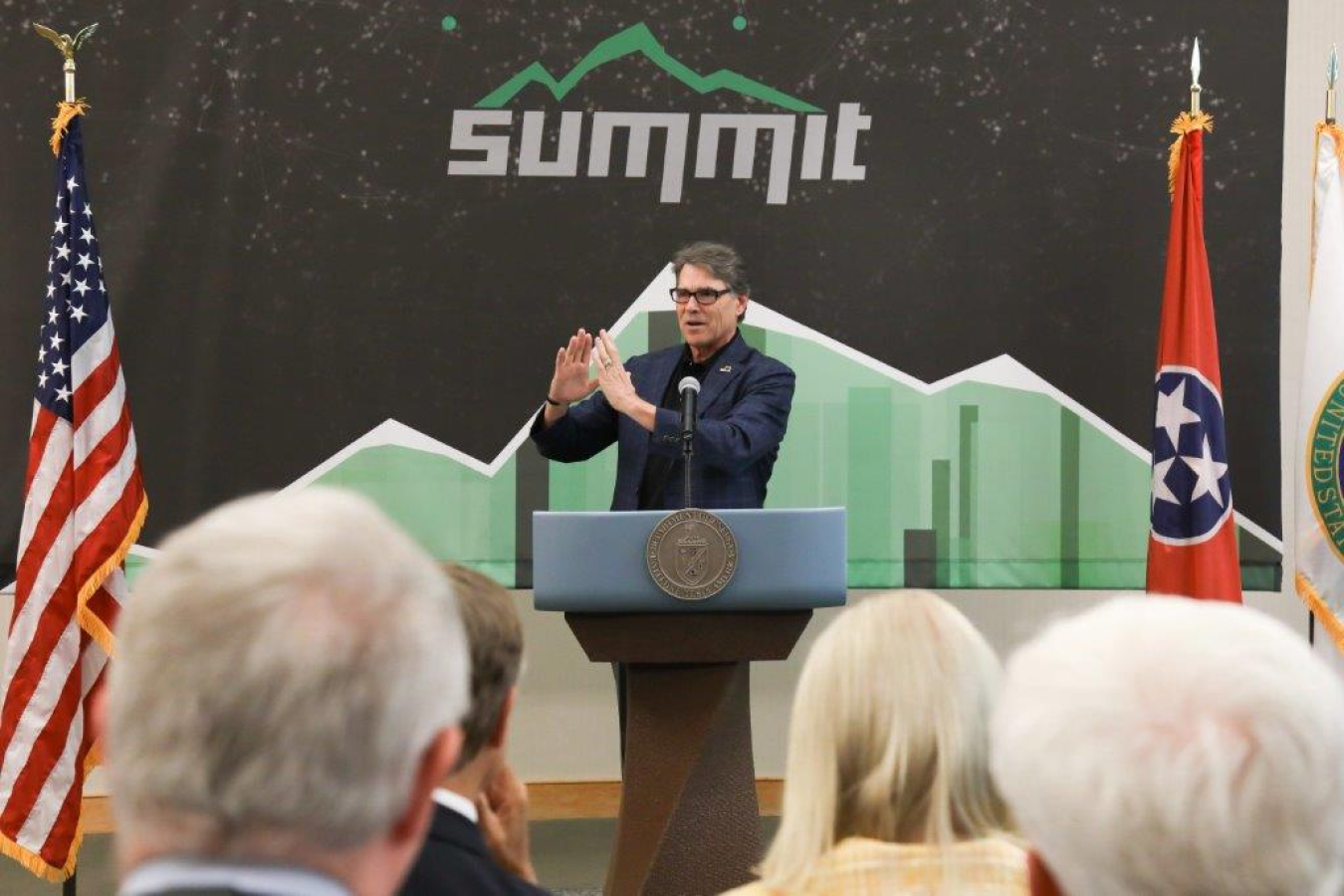
Secretary of Energy Rick Perry speaks from behind a 3D-printed podium at the dedication of the Summit supercomputer at Oak Ridge National Laboratory.
On June 8, 2018, Secretary of Energy Rick Perry traveled to Oak Ridge National Laboratory (ORNL) to dedicate Summit, the world’s fastest and smartest scientific supercomputer. Summit is the newest addition to the Department of Energy’s (DOE’s) fleet of world-class supercomputers. While Summit was the star of the show, other cutting-edge technologies from ORNL’s Manufacturing Demonstration Facility (MDF) were on display. Where a wooden podium would traditionally stand, a futuristic podium tied together the theme of the event.
Every component of the podium, with the exception of the microphone and wiring, was 3D-printed using technology developed at the MDF. The podium is comprised of three distinct pieces, which took less than a day to print using an array of unique materials and technologies. It showcases bio-derived feedstock materials, electron beam printing using metals, and carbon fiber composites. Additionally, the use of advanced coating materials on the base pedestal and top of the podium mean it can be used inside or outside without being adversely affected by the elements such as sun, wind, and rain.
Component | Material | Printing Technology | Coating | Print Time |
Top | 20% CF-ABS (carbon fiber Acrylonitrile Butadiene Styrene) | Blue Gantry large-scale polymer deposition system | TruDesign sand coat with clear paint and flattening agent | 6 hours |
Pedestal | 30% bamboo reinforced with 70% PLA (polylactic acid) | Blue Gantry large-scale polymer deposition system | TruDesign clear paint and flattening agent | 3 hours |
DOE Seal | Ti-6Al-4V (titanium alloy) | Arcam electron beam melting system | N/A | 9 hours, 44 minutes |
Table 1: The three components of the 3D-printed podium showcase a variety of materials, printing technologies, and coatings.
The production of the podium not only showcases the speed and efficiency of various 3D printing technologies, it also demonstrates the precision and flexibility of design available to manufacturers when they utilize additive manufacturing rather than traditional manufacturing methods. For example, traditionally the complex DOE seal would have to be cast. Instead, the Arcam electron beam melting system was used to deposit titanium additively without the use of a die. This podium is just one example of how advances in materials and process technologies can help manufacturers increase energy efficiency, reduce waste and cost, and rapidly test and validate new designs.
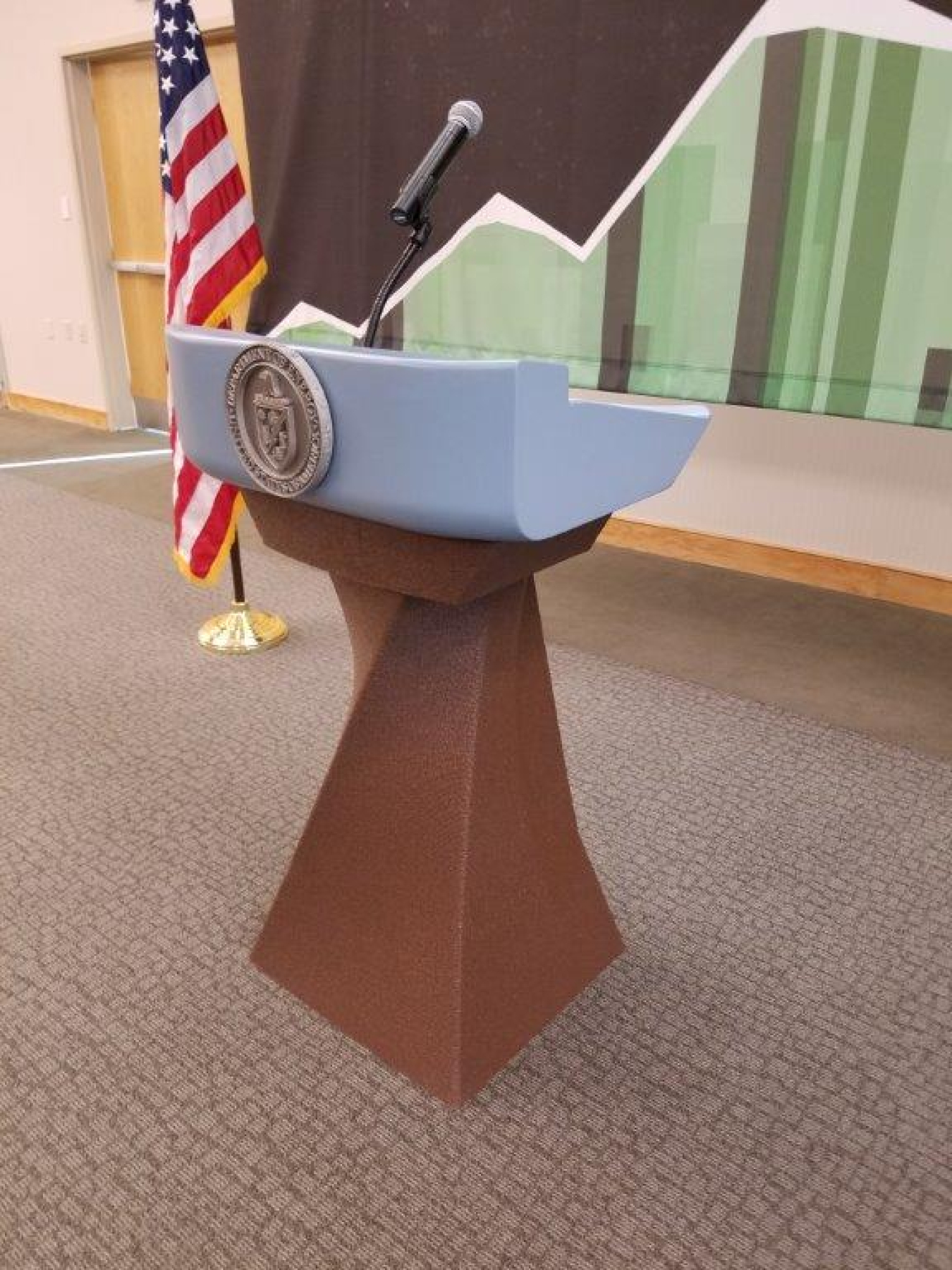
The 3D-printed podium is an example of numerous additive manufacturing technologies, materials, and coatings developed in partnership with the MDF and industry partners.
The Department of Energy’s Manufacturing Demonstration Facility is supported by the Advanced Manufacturing Office and helps industry adopt new manufacturing technologies to reduce life-cycle energy, lower production cost, and create new products and opportunities for high-paying jobs. Learn more about the MDF and its capabilities here.