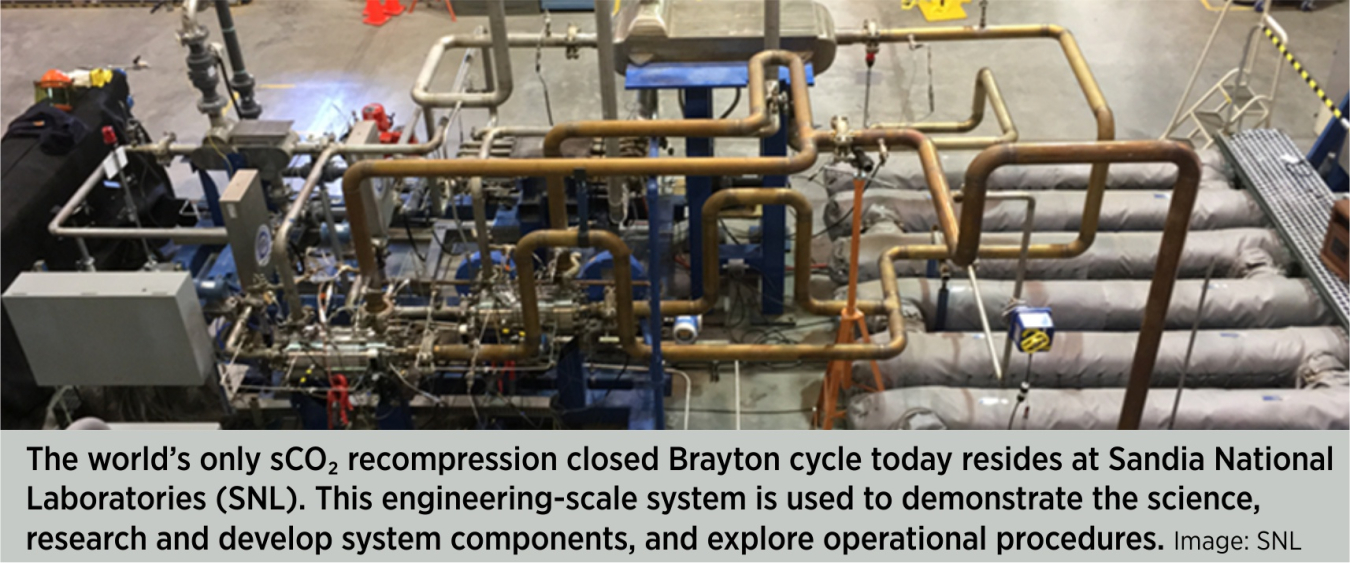
The Office of Nuclear Energy (NE) seeks to establish a commercial-scale recompression, closed Brayton cycle for optimizing the conversion of heat from a small modular reactor into electricity. Investments toward this goal leverage the most promising capabilities within private industry and the Department of Energy’s national labs to achieve relevant, near-term industry objectives and longer-term NE objectives.
Applications for Nuclear Plants:
The primary cycle of interest for application in small modular reactors (SMRs) is the recompression cycle, named for the flow split in which only a portion of the cycle fluid rejects heat while the other portion is recompressed. This cycle efficiently converts SMR-generated heat to electricity under either wet or dry heat rejection conditions, thus allowing the combined power plant to operate efficiently—virtually anywhere in the world.
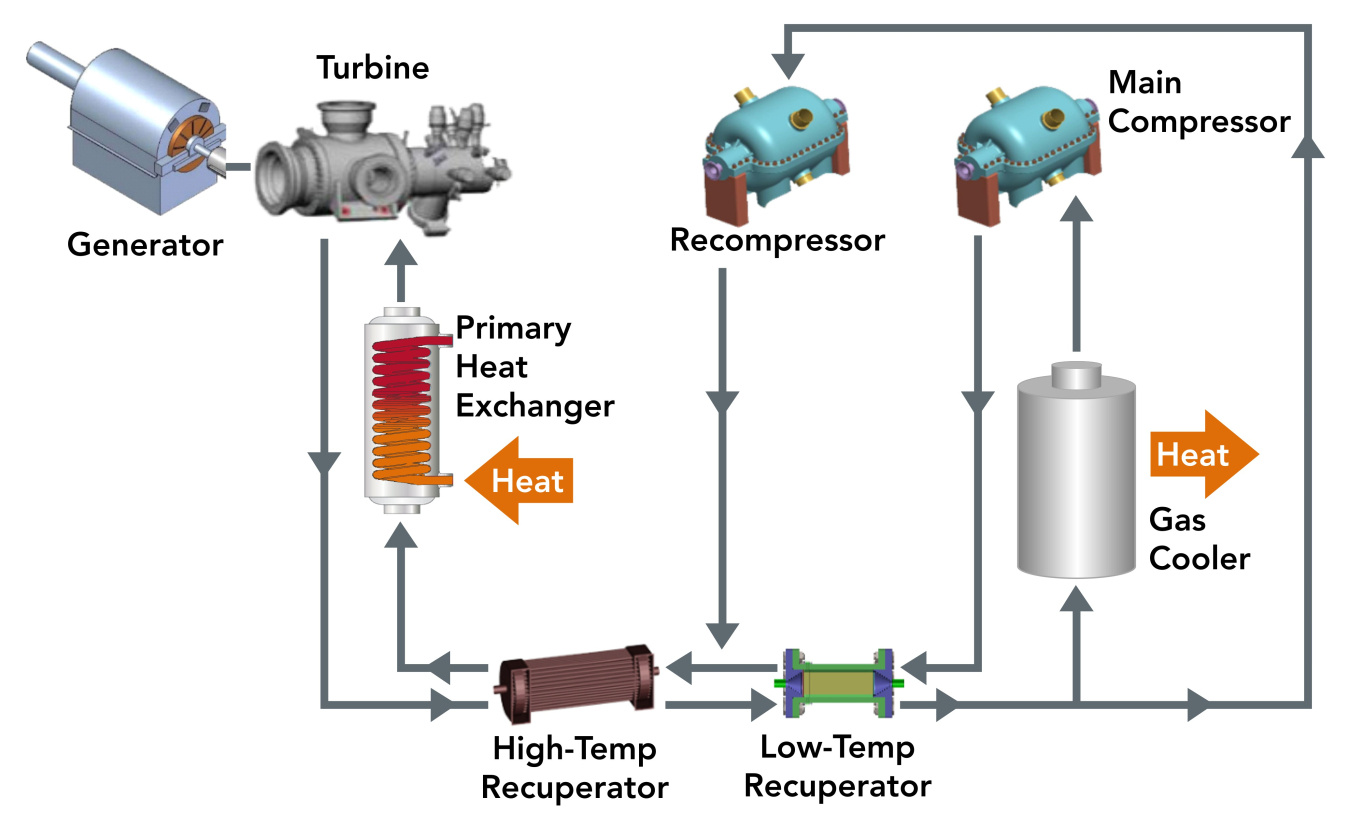
Advanced Reactors (envisioned as <300 MWe SMRs) have three general classes:
- Sodium Fast Reactors: This reactor uses the metal sodium as the reactor coolant, operating at 550◦C. Development of this reactor is the principal objective of DOE-NE.
- High Temperature Helium Reactors: Using helium as the reactor coolant enables operating temperatures of >650◦C, improves safety, and reduces nuclear waste.
- Molten Salt Reactors: Molten salt as a reactor coolant allows for temperatures up to 800◦C.
Benefits, R&D, & Goals for Nuclear Energy:
BENEFITS
- Intelligent thermodynamics for optimal efficiency
- Significantly reduced fuel usage
- Capability for greatly reduced water usage
- Very large range of scalability
- Compact system reducing costs and footprint
- Demonstrate performance at a commercial scale (currently moving a 550◦C lab-scale recompression closed Brayton cycle to the 10 MWe demonstration scale).
- Develop structural materials, qualified seals, and bearings; solve maintenance issues; develop effective and cost-effective heat exchangers; study erosion and corrosion mechanisms.
- Bearings and seals: Develop for turbomachinery operating in a high-temperature CO2 environment.
- High-temperature turbines: Continue to advance technology readiness level by demonstrating proof of performance, reliability, and durability.
- sCO2 compressors: Research parallel operation of two compressors, with one acting on a fluid very close to its critical point; develop designs and procedures to maintain stability in this challenging design.
- Turbomachine rotor shafts: Develop designs and procedures to minimize asymmetric thrusting forces while minimizing windage losses.
- Advanced materials: Test for erosion and corrosion in high-temperature, high-pressure CO2 environments.
- Working fluid additives: Assess their effects on performance factors under various operating conditions.
- CO2-to CO2 and CO2-to-other fluid heat exchangers: Research designs and manufacturing techniques to improve efficiency and reliability while lowering cost.
NEAR-TERM GOALS
- Develop operational procedures for parallel compression near the CO2 critical point.
- Develop system operational procedures for optimal performance under various conditions.
- Collaborate with industry to develop seals and bearings.
- Collaborate with industry to optimize heat exchanger designs for performance and cost.
- Develop the economic models for these systems.