Imagine this modern manufacturing challenge: Building colossal pieces of precision machinery, over 10 tons in weight. Manufacturers must build these pieces of machinery to operate precisely, so that they function properly when fully assembled.
Advanced Materials & Manufacturing Technologies Office
February 16, 2024Imagine this modern manufacturing challenge: Building colossal pieces of precision machinery, over 10 tons in weight. Manufacturers must build these pieces of machinery to operate precisely so that they function properly when fully assembled. The process must be completed as rapidly as possible, to prevent any delays in getting these crucial clean energy technologies up and running. Material waste needs to be minimized. Enter: advanced near net shape manufacturing!
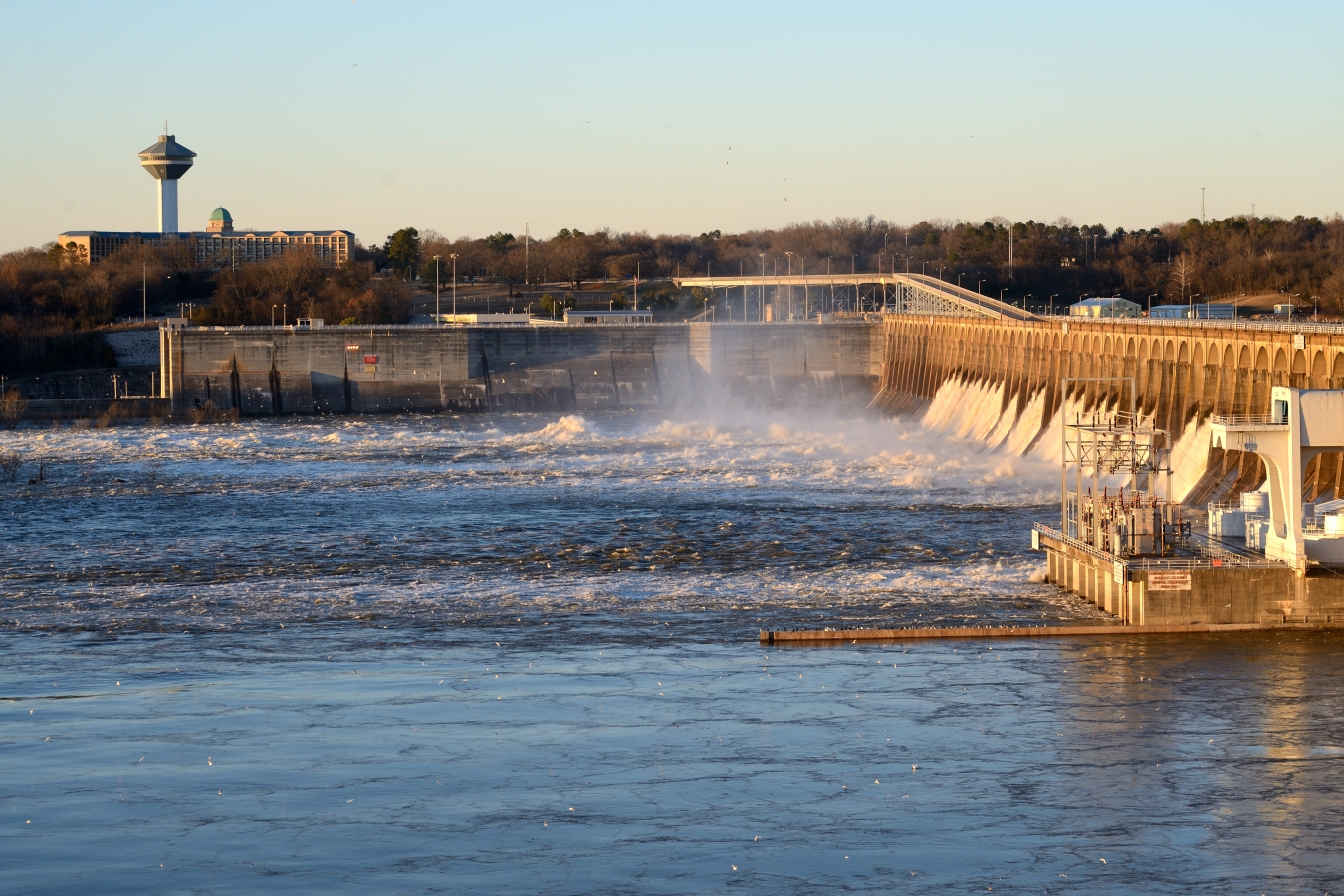
The Wilson Dam on the Tennessee River in northwest Alabama; The installation site of the newly announced robotic hybrid additive manufacturing project that will receive $15 million in federal funding from the Department of Energy.
What Problems Does This Technology Solve?
Currently, the domestic manufacturing sector is unable to competitively produce large metallic components using conventional methods of casting and forging. The inability to domestically produce these components has resulted in increased production costs, longer lead times, reliance on foreign supply chains, and, ultimately, an inhibited ability to manufacture large and complex systems. This reality affects a large cross-section of the manufacturing sector including clean electricity generation, transportation, industrial machinery, tooling, durable goods, and domestic infrastructure.
When these challenges are addressed through domestic manufacturing innovation—including new and innovative methods that allow for faster and more efficient production of components—renewable energy technologies can and will be manufactured faster and more affordably. Not only that, but America’s investments in the manufacturing of clean energy components will strengthen the entire domestic supply chain. This sets our nation on a clear path of achieving our ambitious clean energy goals of 100% clean electricity by 2035 and net-zero emissions by 2050.
What Exactly Is Near Net Shape Manufacturing?
Near net shape (NNS) manufacturing is a term given to processes, including traditional ones such as casting and forging, that aim for the initial fabrication of a component to be close in size and shape to the finished product. These manufacturing methods reduce the production costs and times associated with subsequent finishing steps, such as machining and initial raw material investment costs. Traditional casting and forging are workhorses for near net shape manufacturing of metallic parts, and there is an opportunity to help them deliver even more through integrating them with advanced manufacturing technologies, such as additive manufacturing (3D printing) and smart manufacturing.
Because it reduces waste, near net shape manufacturing is particularly appealing for components that are manufactured with high-value materials, such as those found in several types of renewable energy technologies including components of both wind and hydropower turbines.
AMMTO Commits to Advanced Casting Cell Innovation
In September 2023, the Advanced Materials and Manufacturing Technologies Office (AMMTO) awarded nearly $15 million to GE Research to fund the development, building, and refining of an advanced casting cell (ACC), which is a 3D printer specifically designed to print large (29.5ft x 23ft x 4ft) sand-casting molds for wind turbine rotor hubs and hydropower turbine components. Work also includes development of a robotic welding process to assemble the turbine blades, plate, and rotating shaft of a more than 10-ton Francis runner, which is currently the most commonly used model hydropower turbine. Once commercialized, this technology has the potential to reduce lead times by four months and overall hydropower costs by twenty percent. By using the ACC to create these enormous components, the project will reduce the time it takes to produce this pattern and mold, from around ten weeks to two weeks. The project aims to transform the casting industry through a new vision of the foundry of the future which leverages advanced 3D printing and smart manufacturing.
AMMTO Further Commits to Robotic Hybrid Additive Manufacturing
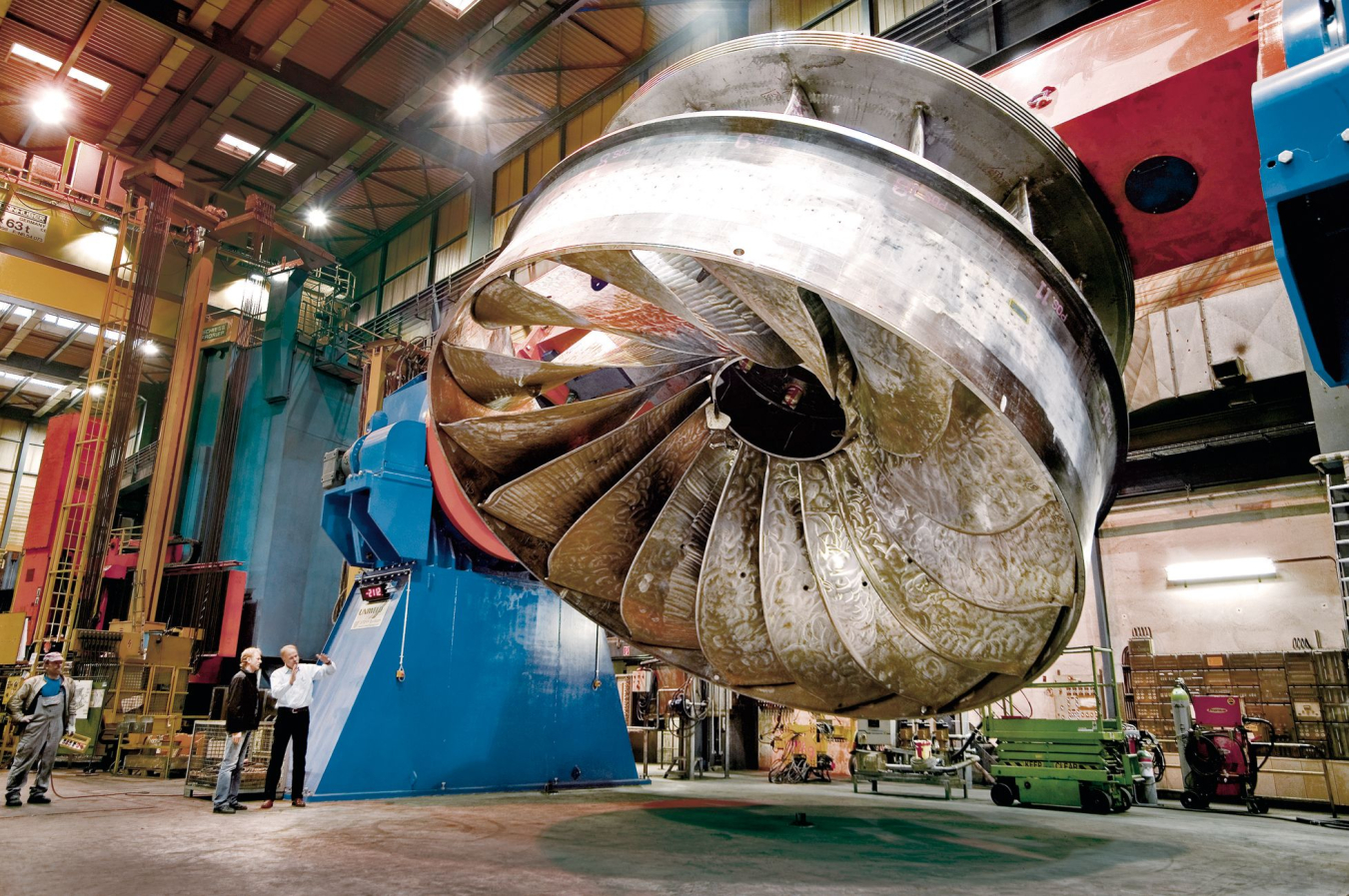
An example of a large-scale Francis turbine runner, the most common type of hydropower turbine used today.
In February 2024, AMMTO and DOE’s Water Power Technologies Office awarded $15 million in funding to a second project—this one based at and led by Oak Ridge National Laboratory (ORNL), in collaboration with the Tennessee Valley Authority (TVA)—to develop an innovative robotic hybrid additive manufacturing process. The project takes a fundamentally different approach to manufacturing via metal casting by focusing on direct 3D printing of large-scale metal structures. This manufacturing technique has the potential to cut the lead time of this existing process in half. The project will produce a full-scale Francis runner and will collaborate with TVA to install and demonstrate this innovative hydropower turbine at the Wilson Dam on the Tennessee River in northwest Alabama.
Why Are These Projects So Important?
These two projects are crucial to building domestic knowledge, capability, and capacity to produce large metallic components and strengthen America’s manufacturing sector for clean energy and beyond. These projects are aligned with the clean energy goals identified by the Biden-Harris Administration as well as with DOE’s Strategy to Secure America’s Supply Chains for the Clean Energy Transition, released in February of 2022. The inability to competitively manufacture large components domestically is emphasized as one of the common vulnerabilities in this strategy report. Lastly, these two projects address the national priorities outlined in the White House’s National Strategy for Advanced Manufacturing, released in October of 2022.
As the American manufacturing sector continues to develop methods to create renewable energy technologies here at home, the U.S. Department of Energy remains laser focused on modernizing and streamlining manufacturing. We’re not afraid to tackle 10-ton problems, and funding technological advancement in domestic near net shape manufacturing remains just one (heavy metal) example of how we’re working to actualize a clean energy future for our nation.