Success in Carbon Conversion to Building Materials
A University of California, Los Angeles (UCLA) technology, developed in partnership with National Energy Technology Lab (NETL) and U.S. Department of Energy’s (DOE) Office of Fossil Energy and Carbon Management (FECM), won the grand prize in the prestigious NRG COSIA Carbon XPRIZE global competition. They developed an eco-friendly process that infuses a revolutionary concrete with carbon dioxide (CO2) emissions directly captured from power plants and other industrial facilities.
UCLA’s CarbonBuilt team was awarded the grand prize and will receive $7.5 million. The team was recognized for having the best demonstration project, as well as for the product’s technology and market advantages. UCLA’s entry was one of 47 submissions from 38 teams in seven countries. “This outstanding project represents another example of how the U.S. Department of Energy’s (DOE) Office of Fossil Energy and Carbon Management and NETL collaborate with and support outstanding university researchers to advance carbon management solutions and reduce CO2 emissions,” said NETL Director Brian Anderson, Ph.D.
DOE’s Carbon Utilization Program, which provided funding for the winning project, supports development of technologies to convert CO2 into environmentally responsible, equitable, and economically valuable products. UCLA’s CarbonBuilt team successfully demonstrated a process to create concrete masonry units (CMUs, or concrete blocks) utilizing CO2 from power plant flue gas without the need for a carbon capture step through a unique carbonation process known as mineralization. The gaseous CO2 from power plant flue gas and other sources was transformed into stable carbonate solids that bind the components in the concrete. “The resulting blocks can be used in the same construction applications as traditional concrete blocks made with ordinary Portland cement (OPC),” said Andrew Jones, who has managed the project for NETL. According to Jones, more than 20 billion tonnes of concrete are produced each year. “Concrete is cheap, abundant and resilient, but the manufacture of OPC that traditionally binds the mixture creates approximately 10% of all global CO2 emissions,” Jones said.
UCLA completed field testing of its novel concrete production system at the Wyoming Integrated Test Center and National Carbon Capture Center (NCCC), a facility sponsored by DOE and NETL. During the NCCC testing, a total of six cement batches were produced (four using coal flue gas and two using natural gas flue gas) to produce more than 5,000 concrete blocks. In the competition’s demonstration at the Wyoming Integrated Test Center, the team successfully sequestered nearly three tonnes of CO₂ into more than 10,000 concrete blocks as they cured. According to researchers, each concrete block stores about three-quarters of a pound of CO2 — a significant amount considering an estimated 1 trillion concrete blocks will be produced annually by the year 2027.
Sourced From: https://netl.doe.gov/node/10675
Additively Manufactured High Temperature Centrifugal Impellers for Low Cost SOFC Recycle Blower-Mohawk Innovative Technology, Inc.
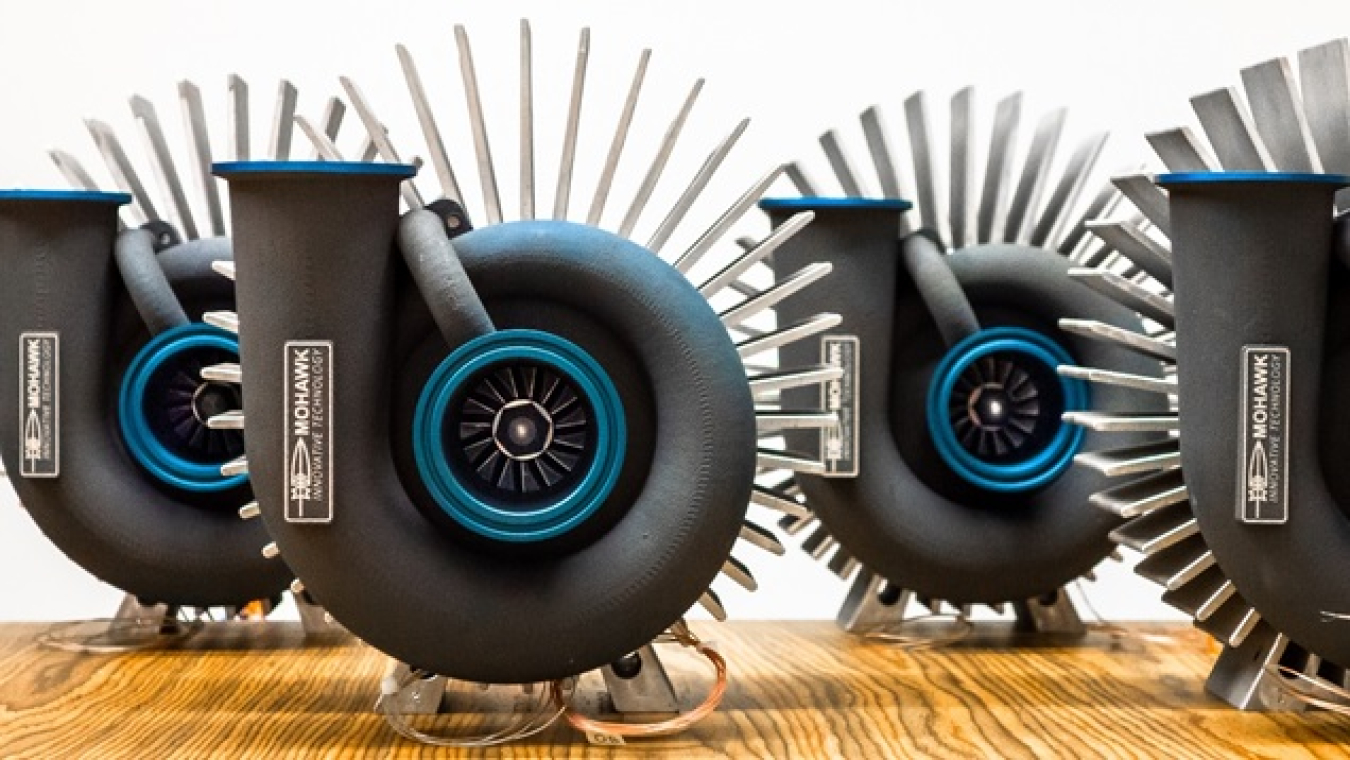
Mohawk Innovative Technology’s High Temperature Anode Recycle Blower (ARCB) is being tested in Fuel Cell Energy’s 100 kW Solid Oxide Fuel Cell (SOFC) Power system: Mohawk tested the High Temperature Anode ARCB under accelerated conditions for approximately 3.5 months, simulating approximately 12 months of normal operation under system operating conditions. The ARCB is a critical balance-of-plant component and its reliability and cost play a significant role in making progress towards cost-effective reliable SOFC and Solid Oxide Electrolyzer Catalyst (SOEC) systems. After stand-alone testing under operating conditions mentioned above, the Mohawk ARCB is being field tested in Fuel Cell Energy’s 100 kW SOFC Power system since August 2021. The original target test time of 1,000 hours was successfully met and exceeded, and the unit is now approaching 2000 hours of continuous operation in the fuel cell system. The ARCB is estimated to be 50% lower in cost than state-of-the-art after production of 100 units. Additive Manufacturing will be used to further reduce cost by as much as 20%. This test demonstrates collaboration between two projects in advancing SOFC and SOEC technologies towards the goal of commercial deployment of SOFC power systems and SOEC systems for hydrogen production.
Successful Design and Fabrication of PBI-CMS HFMs for Modular Air Separation- Los Alamos National Laboratory
With funding from the Department of Energy's Office of Fossil Energy and Carbon Management, Los Alamos National Laboratory (LANL) successfully designed and fabricated asymmetric polybenzimidazole (PBI)- derived carbon molecular sieve (CMS) hollow fiber membranes (HFMs) that are resistant to collapse and contain optimizable selective layer and porous support morphologies. Through rigorous controlled modification protocols, a PBI-CMS HFM having an oxygen permeance of 72 gas permeation unit and an O2/N2 selectivity of 11 was obtained. LANL will continue to optimize the selective layer thickness and porous support morphology to obtain a membrane that has a permeance of 100 and a selectivity of 15 during the upcoming fiscal year. Optimization of these PBI-CMS HFMs will enable the development of an energy efficient modular air separation unit that can be integrated into a cost-competitive, small-scale (1-5 MWe), near-zero emission gasification system.
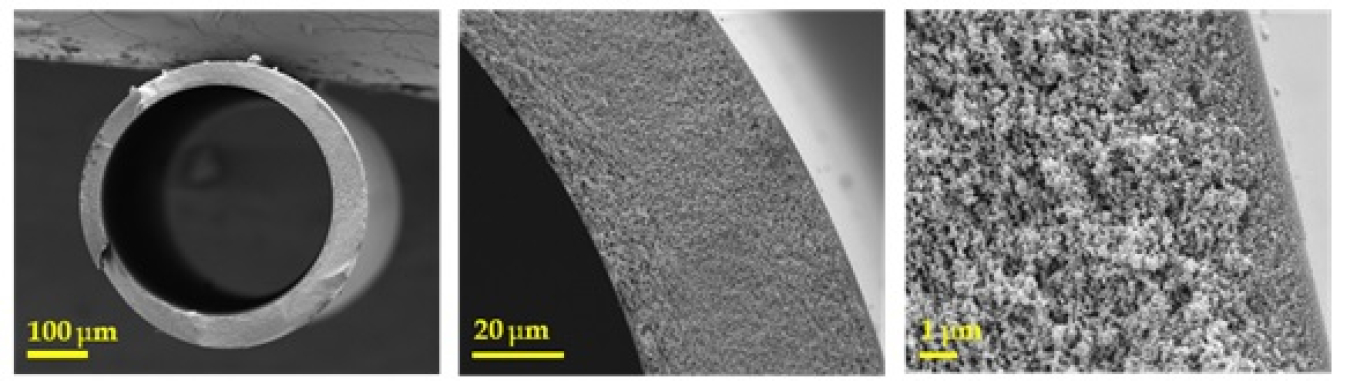
OFFSHORE CARBON STORAGE ASSESSMENTS
Quantitative estimates of regional geologic storage resources are key to advancing the widespread deployment of carbon capture and storage (CCS). Recent studies funded by DOE FECM provide improved estimates and technical understanding of carbon dioxide (CO2) storage potential in the Outer Continental Shelf in the Gulf of Mexico (GOM) and offshore along the Atlantic coast. Studies of the GOM, aided by existing subsurface data from the oil and gas industry, show a potentially vast resource for dedicated CO2 storage, including both depleted oil and gas fields and saline storage, with aggregate estimates of over hundreds of billions of metric tons of storage potential. In this area, initial characterization efforts determined the potential to develop three storage sites, each capable of storing above 30 million metric tons of CO2—High Island 24L field, High Island 10L field, and Ship Shoal Block 84 and Block 107.
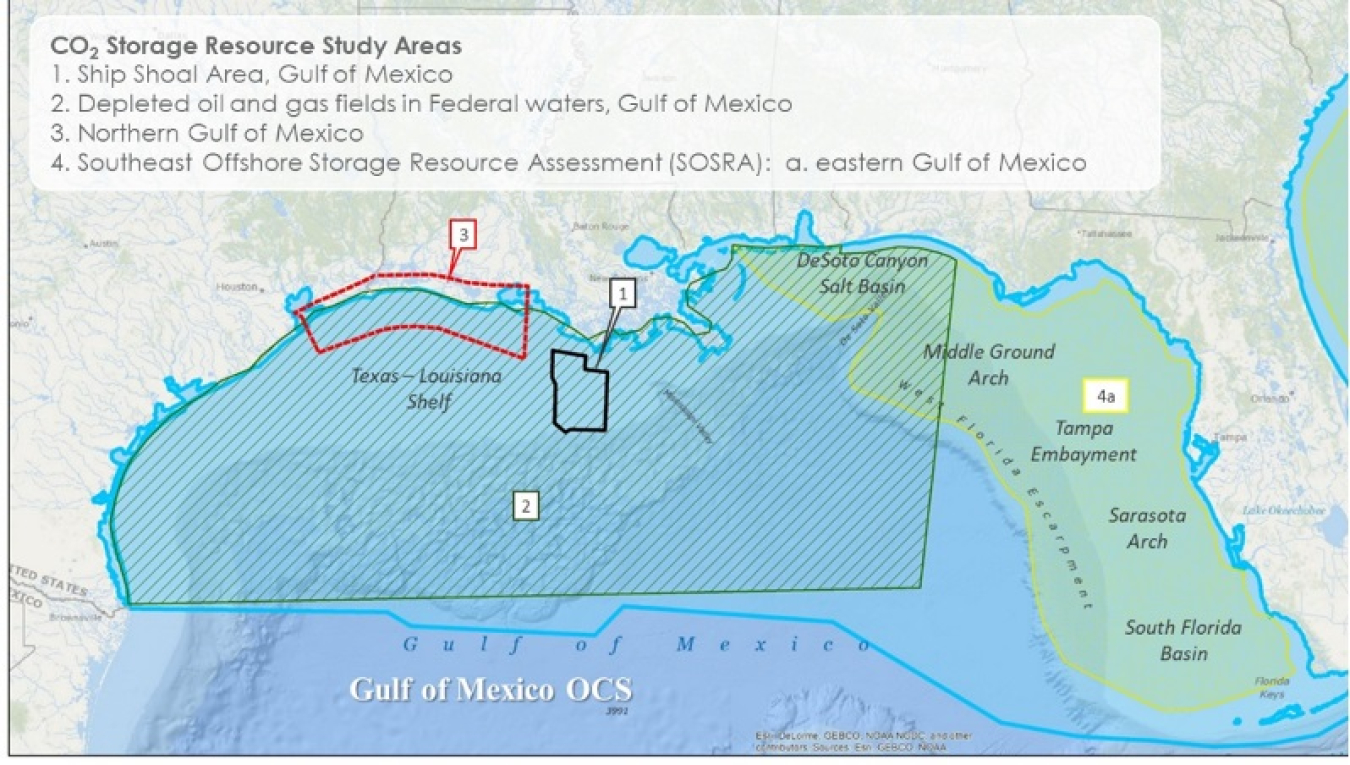
In the Atlantic, improved data-driven stratigraphic models suggest CO2 storage resources offshore of the east coast from Massachusetts to northern Florida could be over hundreds of billions of metric tons.
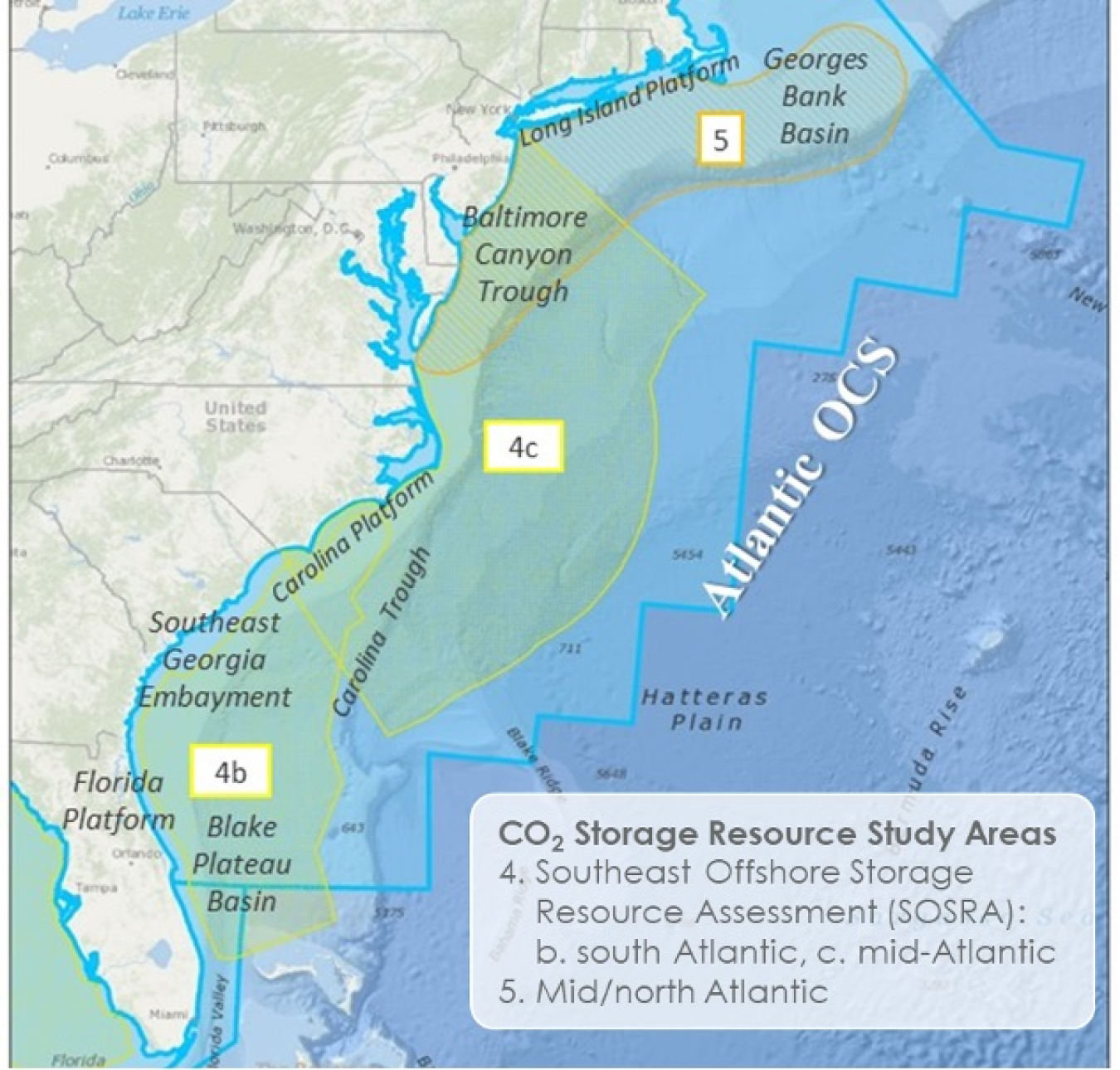
Steady Thermal Aero Research Turbine (START) facility at Pennsylvania State University
Understanding and managing key turbine performance parameters such as aerodynamics, temperature, and cooling performance are critical for designing more energy efficient turbines. Through START, a break-through design tool was developed that allowed for first-of-a-kind data acquisition on these key turbine performance parameters. The design tool will help accelerate deployment of low emissions, higher efficiency turbines in the future. The START facility also houses the National Experimental Turbine (NExT), a turbine testing platform designed in collaboration with four turbine manufacturers and focusing on US technology advancement. While all turbine geometries are highly proprietary, the goal for NeXT is to provide a modern turbine design that can be used by companies quickly and cheaply to do proprietary research in the future. NExT is fully booked through early 2023 for proprietary component development projects.
Advanced UltraSupercritcial (AUSC) Component Testing (ComTest)
The Advanced Energy Materials Program recently completed the $27 million AUSC ComTest project launched in 2015. This program is truly crosscutting, as the nickel superalloys developed under this program have been used in the STEP demonstration project, and they are applicable to concentrating solar thermal plants, nuclear plants, and combined cycle plants. Achievements included:
- American Society of Mechanical Engineers (ASME) code case approval for Inconel 740 and Haynes 282, gamma prime precipitate strengthened nickel superalloys approved by the ASME for use in boilers and pressure vessels. The ASME code stamp is required and is a mandatory requirement of many insurance companies across much of the U.S. and in more than 100 countries.
- Fabrication and field erection of full-scale versions of selected key components made of nickel-based alloys. The photo below shows the field erection simulation of the headers and tube sections fabricated under the program.
- Demonstration of welding, bending, heat treatment, forging and casting processes for Inconel 740 and Haynes 282. Photo of Haynes 282 casting of turbine shell below.
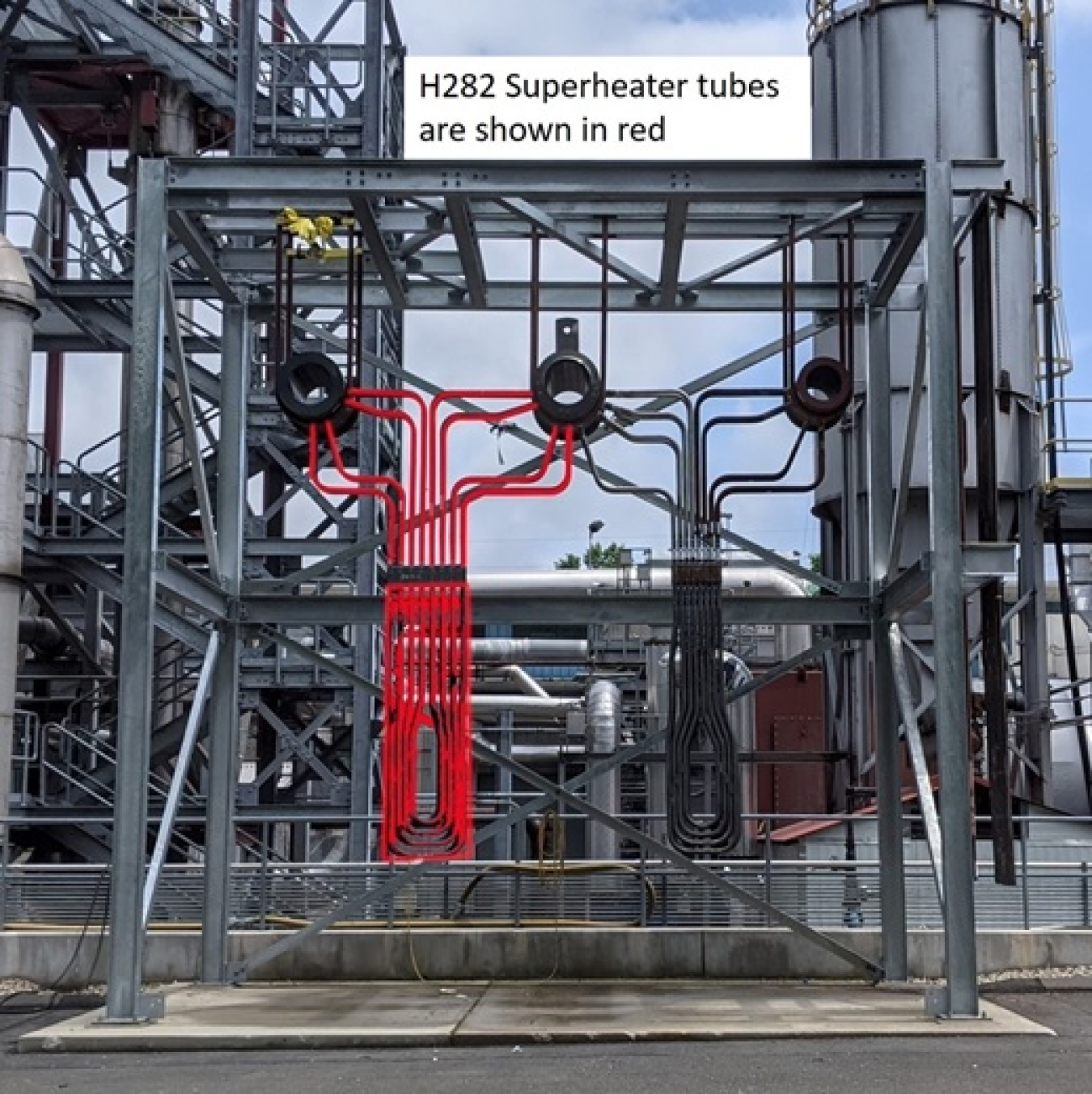
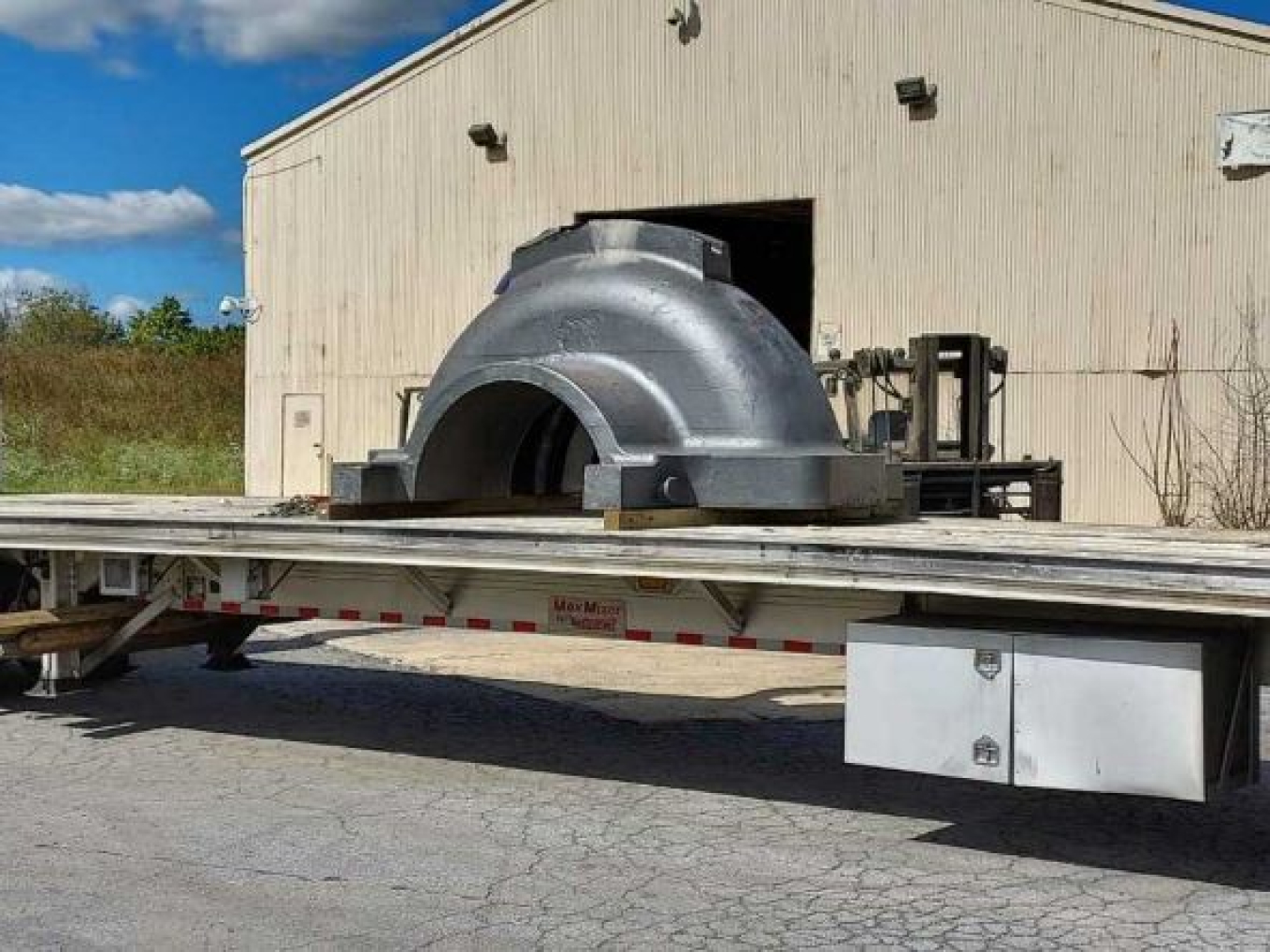
Novel Temperature Sensors and Wireless Telemetry for Active Condition Monitoring of Advanced Gas Turbines
Siemens Corporation (under DOE Project DE-FE0026348) has successfully demonstrated a first-of-a-kind, real-time wireless sensor system for turbine component condition-based monitoring using on-blade temperature measurements. The $4.7M project, sponsored by the FECM Crosscutting Research Sensors & Controls program, was completed in FY21 and has achieved a series of technological breakthroughs in the extremely harsh operating environment encountered in combustion turbines including:
- Novel, rugged spray-on blade thermocouples operating at temperatures >1100°C
- On-blade electronics to wirelessly transmit the thermocouple data via radio frequency at temperatures up to 500 °C
- Wireless power transfer of up to 5 watts to supply the rotating electronics circuit board at temperatures up to 600 °C
Siemens successfully tested the fully packaged, proof-of-concept wireless sensor system on an operating utility combustion turbine at a Duke Energy power plant. This technology is also directly transferrable to future hydrogen turbine applications.