Design, manufacturing, and transportation option assessments show how “supersized” blades could increase energy, affordability, and site viability.
Wind Energy Technologies Office
May 20, 2019Research helps inform and prioritize DOE R&D opportunities for long blades
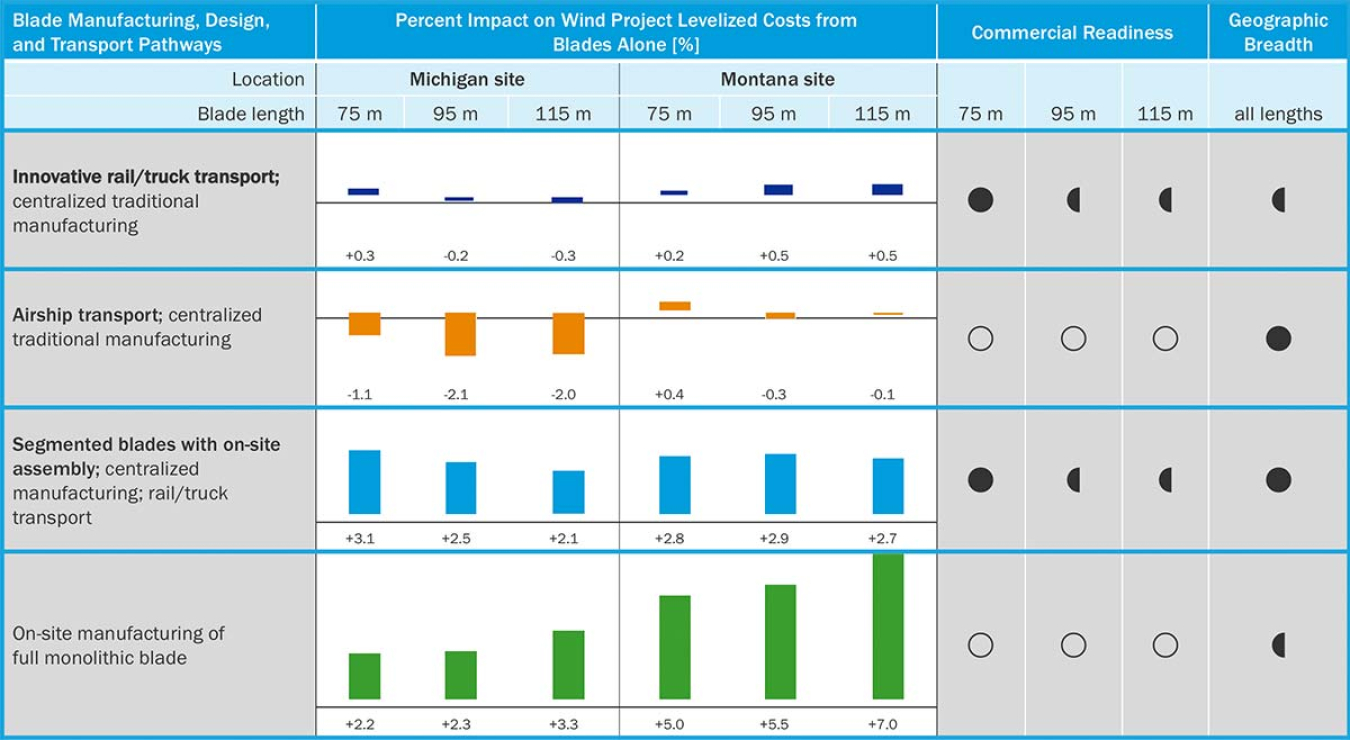
Summary of supersized rotor analysis findings, highlighting key results and trade-offs among the four pathways assessed. Figure by DNV GL
The move toward progressively longer wind turbine blades has been a lasting trend in the industry and has helped reduce the cost of wind energy. But without additional innovation, transportation challenges could curtail further blade growth opportunities.
Lawrence Berkeley National Laboratory partnered with DNV GL Energy USA, Inc. (DNV GL) to study key design, manufacturing, and transportation options to advance long, “supersized” blades for cost-competitive land-based wind energy and to inform DOE prioritization of potential R&D opportunities. These larger blades make it possible to increase energy capture, potentially reducing the overall cost of wind energy nationwide and opening up lower wind-speed sites for potential development.
The study focused on blades with lengths of 75 to 115 meters (m), compared to the current U.S. average of 55 m for newly installed wind projects. Currently, blades up to 67 m can be transported over rail and roads using typical transport methods.
Building on input gathered by DOE in a workshop and via a public request for information, researchers analyzed four possible innovative design, manufacturing, and transportation pathways that might enable these supersized blades:
- Rail and truck transportation of full blades that, with longer blade lengths, includes controlled bending of the blades
- Air transportation of full blades with lighter-than-air cargo airships
- Traditional rail and truck transportation of segmented blades with on-site assembly
- Full on-site manufacturing of complete blades.
Based on available data and two hypothetical project sites, each pathway was assessed quantitatively, estimating the cost of delivered blades (considering the cost of the equipment and transportation) and the contribution of the blades to system-level levelized cost of wind energy (LCOE). Trade-offs related to commercial readiness and the geographic breadth of applicability were also discussed.
The analysis results summarized in the figure show that the use of lighter-than-air cargo airships or controlled blade bending (i.e., bending of blades to navigate curves) in rail transport may present the most promise for delivery of supersized blades to project sites at a neutral or reduced overall system LCOE. Because lighter-than-air airships are not yet commercially available, the analysis of that option is speculative. Moreover, rail transport with blade bending—required for rail transport with blade lengths on the higher end of the spectrum—has yet to be attempted, and there are also geographic limitations on where it might be viable.
While other pathways studied increase blade-related LCOE, requiring cost reductions in other aspects of the wind system to decrease total LCOE, segmented blades offer the unique ability to deploy supersized blades across the entire United States. In addition, turbine manufacturers already have some experience with this solution. On-site (mobile) blade manufacturing, meanwhile, faces challenges such as low equipment utilization and the expense and complexity of commissioning and operating mobile manufacturing plants.
Based on the study, industry insight, and familiarity with national laboratory capabilities, DNV GL identified a number of R&D activities that could make valuable contributions to the viable development of supersized blades. These recommendations are feeding into the DOE-funded multiyear, multilab “Big Adaptive Rotor” project to assess and prioritize technology needed to develop a cost-competitive land-based 5-MW turbine with 100-meter-long blades.