Whether by barge, truck or train, when large pieces of equipment arrive at the Waste Treatment and Immobilization Plant (WTP) on the Hanford Site, the crane and rigging team is trusted to plan and perform delivery and installation.
Office of Environmental Management
December 6, 2022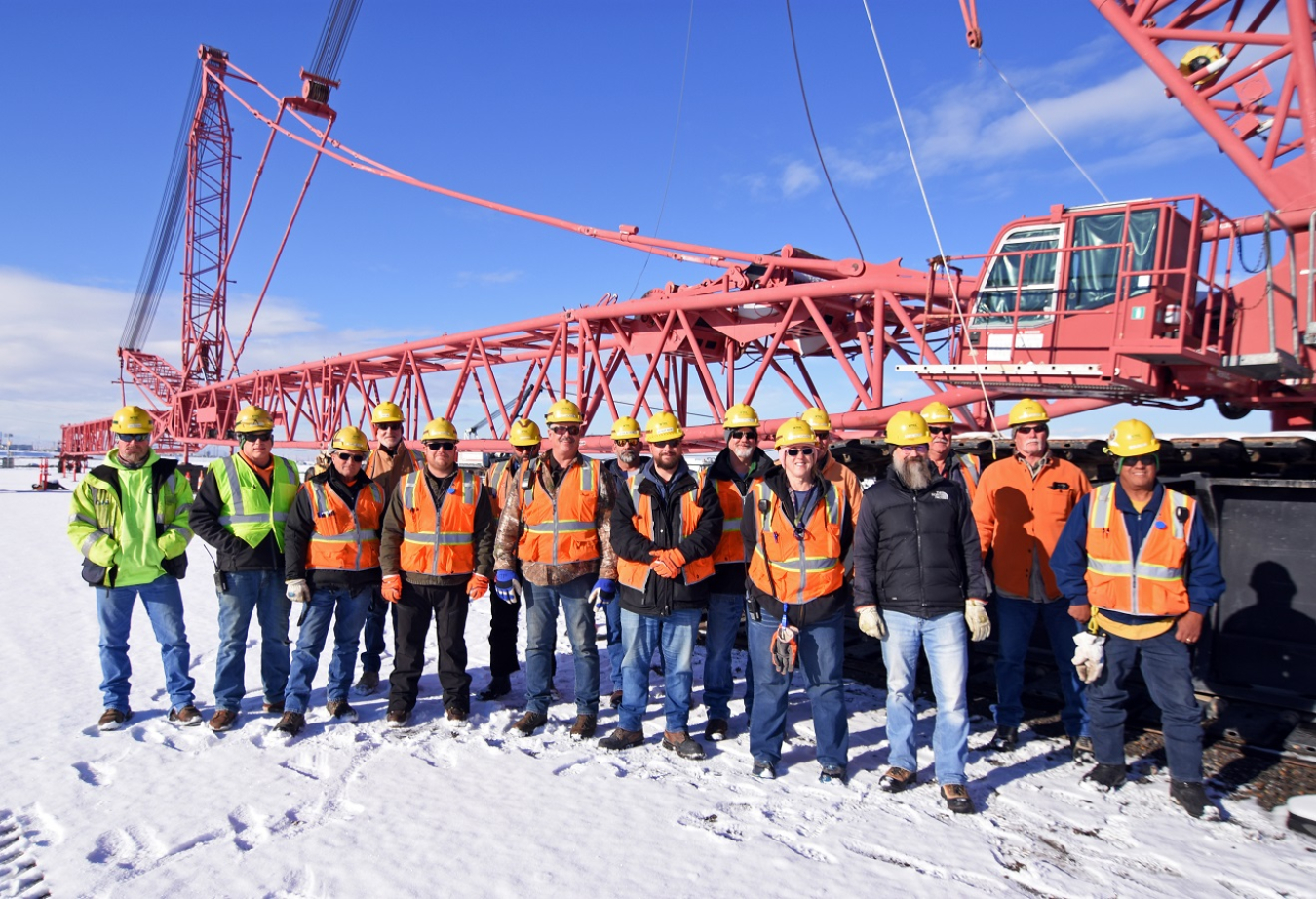
RICHLAND, Wash. – Whether by barge, truck or train, when large pieces of equipment arrive at the Waste Treatment and Immobilization Plant (WTP) on the Hanford Site, the crane and rigging team is trusted to plan and perform delivery and installation.
“We’ve been involved with the installation of just about every piece of major equipment that comes into the plant, from 300-ton melters to tower cranes and 275-ton vessels,” said Sean McGaughy, the crane and rigging team superintendent with the Waste Treatment Completion Company (WTCC), a subcontractor to project lead Bechtel National Inc. “Melters, vessels, structural steel; we’ve installed it all.”
Their work has included assembling three tower cranes and nine heavy-lift crawler cranes and, in what McGaughy calls one of the team’s most challenging projects, disassembling the low-activity waste tower crane, which the team did 200 feet in the air.
“The difference between doing work in the air and on the ground is if you pick something up and you’re a little off and it’s only six inches off the ground, you can set it back down and reconfigure,” he said. “You have to be spot on in the air.”
The size of the rigging crew used for a task varies by the job but usually includes McGaughy, who has been with WTP since 2002; Ryan Hoff, the WTCC rigging engineer who creates plans for equipment that weighs more than 10 tons or is of high value to the project; and as many as 10 operators, six ironworkers and nine truck drivers. The team creates an engineering lift plan, gathers the rigging hardware, determines which crane or equipment should be used for installation, performs load tests and safely installs the equipment.
“I look back at everything this team has done and who’s done what to get the plant up and running, and this team has been a huge part of the success,” said John Andreatta, the High-Level Waste Completion manager. “During the startup and commissioning phase of the Direct-Feed Low-Activity Waste (DFLAW) Program, the team led the way on the lift planning, load testing and testing of the low-activity waste permanent operations cranes.”
Most of the equipment arrives at the site on trucks, but the heavier, larger items — such as two massive vessels that weighed 170 tons each — arrive on barges on the Columbia River from Portland, Oregon, to the Port of Benton in Richland, Washington. There they are offloaded onto hydraulic platform trailers and transported to the jobsite at Hanford.
“Everything we do has a schedule,” said McGaughy. “We need to have our work done before the project can proceed with the next activity. We do our best to meet the schedule, but we never sacrifice safety for schedule.”
One of the greatest challenges was installing two 300-ton melters, the largest nuclear industry melters in the world, which are key to the plant’s DFLAW process.
“Our involvement with the melters has been a pretty big chunk of work,” said Hoff.
“We’ve been involved with the melters since about 2010,” said Andreatta. “It’s been gratifying to see it come to completion. This is a megaproject, and these are the team members getting it done in the background.”
To receive the latest news and updates about the Office of Environmental Management, submit your e-mail address.