Maintaining safety systems at a 70-year-old DOE site can pose challenges, but the motor shop for the EM program at Savannah River Site (SRS) has successfully addressed them.
Office of Environmental Management
March 21, 2023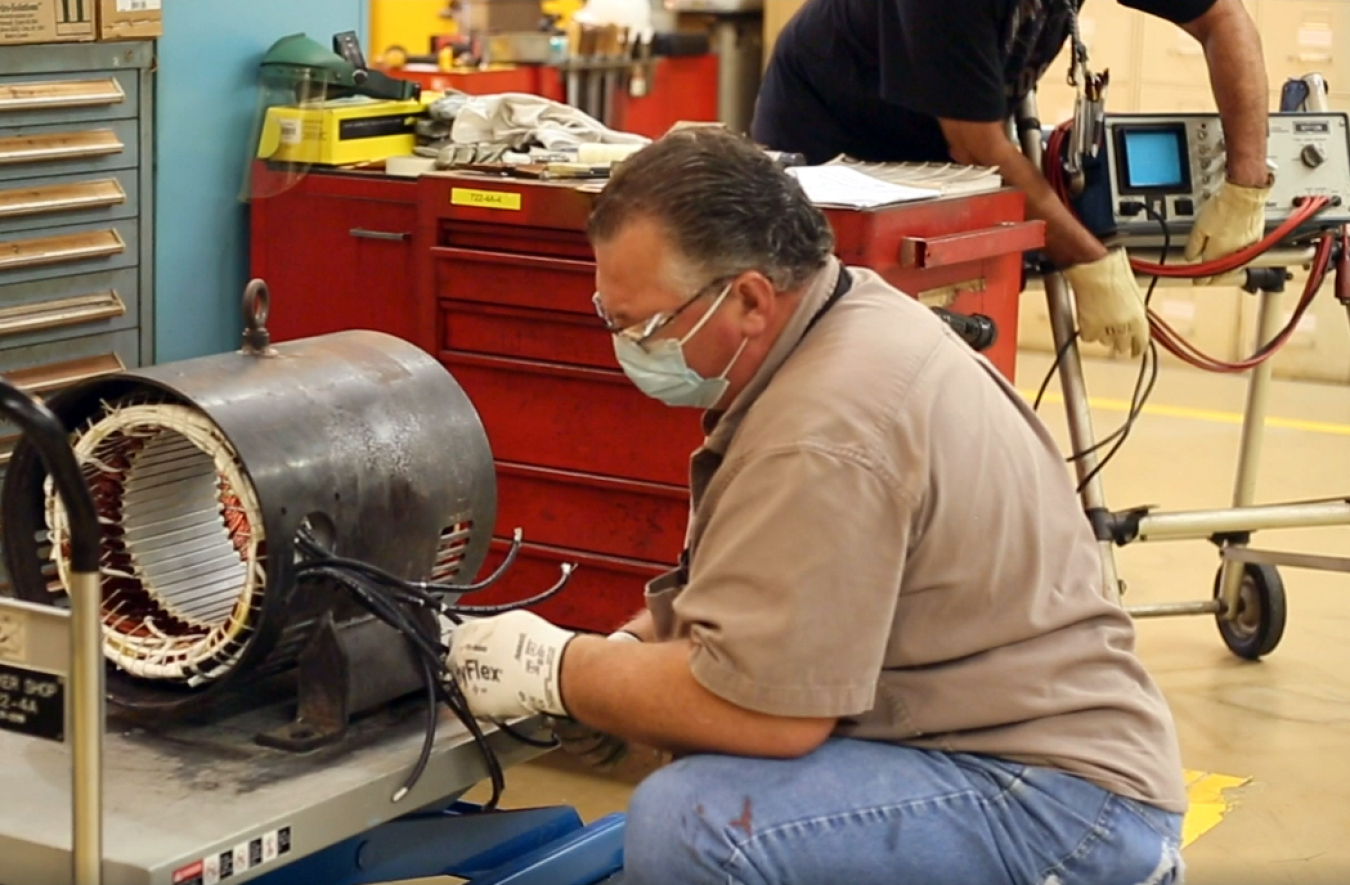
Motor Specialist James Fuller replaces long strands of copper wire — a process known as motor rewinding — found within this electric motor for the EM program at Savannah River Site. Motor rewinding is a maintenance skill difficult to find in the U.S. workforce, according to Savannah River Nuclear Solutions.
AIKEN, S.C. – Maintaining safety systems at a 70-year-old DOE site can pose challenges, but the motor shop for the EM program at Savannah River Site (SRS) has successfully addressed them.
“We have numerous highly specialized and often unique electrical motors at SRS that were manufactured decades ago for use in our nuclear production facilities but can no longer be purchased, nor parts procured for them,” said Mike Violette, manager of the motor shop operated by EM contractor Savannah River Nuclear Solutions (SRNS). “Many systems are dependent on these motors, and we simply cannot allow them to remain in place after failing.”
Experienced mechanics have repaired the motors in the past, but their numbers are dwindling as new employees join the workforce.
“There was a time when our shop had several mechanics who had the knowledge and skills to repair any of these motors as needed; however, those days are gone,” said Violette. “In fact, at this time, approximately 50% of our company’s entire workforce has less than five years of experience at SRS.”
As a result, the motor shop has two choices when electrical motors falter: search for and recruit a seasoned mechanic with the needed maintenance expertise, or work with SRNS engineers to determine the specifications needed to design and manufacture custom replacement motors.
“The choice from a financial perspective was obvious: find the right person to hire. We knew this was the best answer, but we also knew it would be difficult, and maybe, not even possible,” said Violette.
As luck or fate would have it, SRNS found motor specialist James Fuller, who possessed over 30 years of experience in the field, Violette said.
“Watching him perform his craft is amazing,” Violette said. “Rebuilding an electrical motor involves a lot more time, effort and skill than the average employee would guess.”
The repair process, known as motor rewinding, involves several unique steps. Properly removing and replacing the many long strands of copper wire found within each motor is critical to this maintenance work.
“It is imperative that we ensure safety equipment in our nuclear facilities is maintained to the highest standards and continuously available for operations,” said Mike Swain, senior vice president, SRNS Technical Services. “We have a long history of cost-efficiently and effectively doing so. We will continue to do our part within the Savannah River Site’s tradition of safety first.”
To receive the latest news and updates about the Office of Environmental Management, submit your e-mail address.