Improving processes to increase efficiency and reduce waste are vital to the Hanford Site cleanup mission.
Office of Environmental Management
June 14, 2022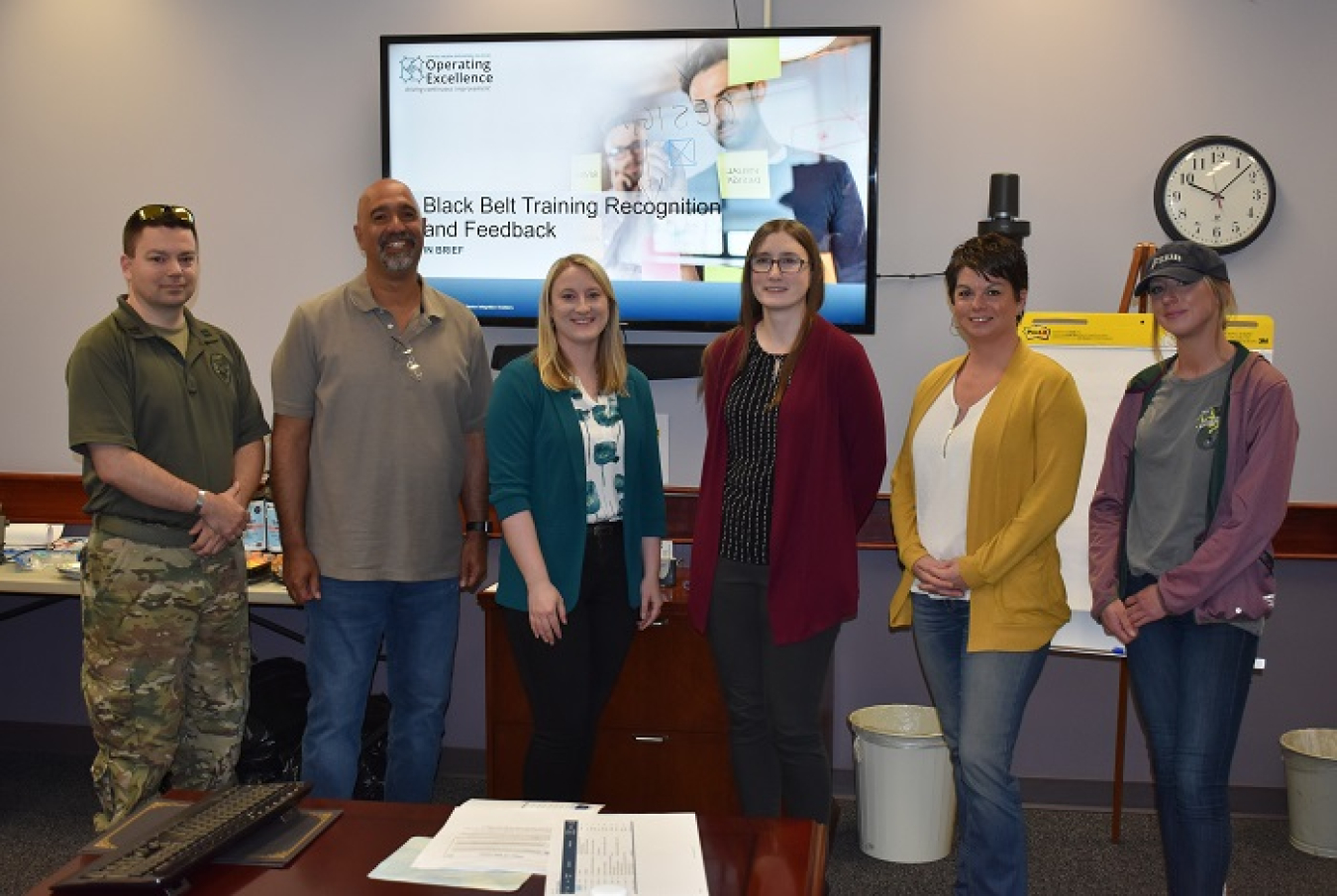
RICHLAND, Wash. – Improving processes to increase efficiency and reduce waste are vital to the Hanford Site cleanup mission.
They are also the driving forces that guide the Hanford Lean Six Sigma program, led by EM Richland Operations Office (RL) contractor Hanford Mission Integration Solutions’ (HMIS) Operating Excellence program.
The program teaches participants how to incorporate “lean” thinking and Six Sigma methodologies to identify opportunities for improvement within organizations by eliminating waste and increasing standardization. Candidates must complete 40 hours of training to earn Green Belt certification.
A cohort of certified Hanford Green Belts recently completed the next level of Lean Six Sigma Black Belt training, meeting virtually with instructors from Rutgers University for 12 weeks. The class included employees from contractors HMIS, HPMC Occupational Medical Services, Central Plateau Cleanup Company and Washington River Protection Solutions (WRPS).
“We are so proud of the work our Lean Six Sigma professionals perform throughout the Hanford Site,” said Holly Munroe, a certified Black Belt coach with HMIS. “We want each of them to encourage, instill and expand a culture of continuous improvement, to continue to move the mission forward through identifying ways we can work smarter in our everyday work processes.”
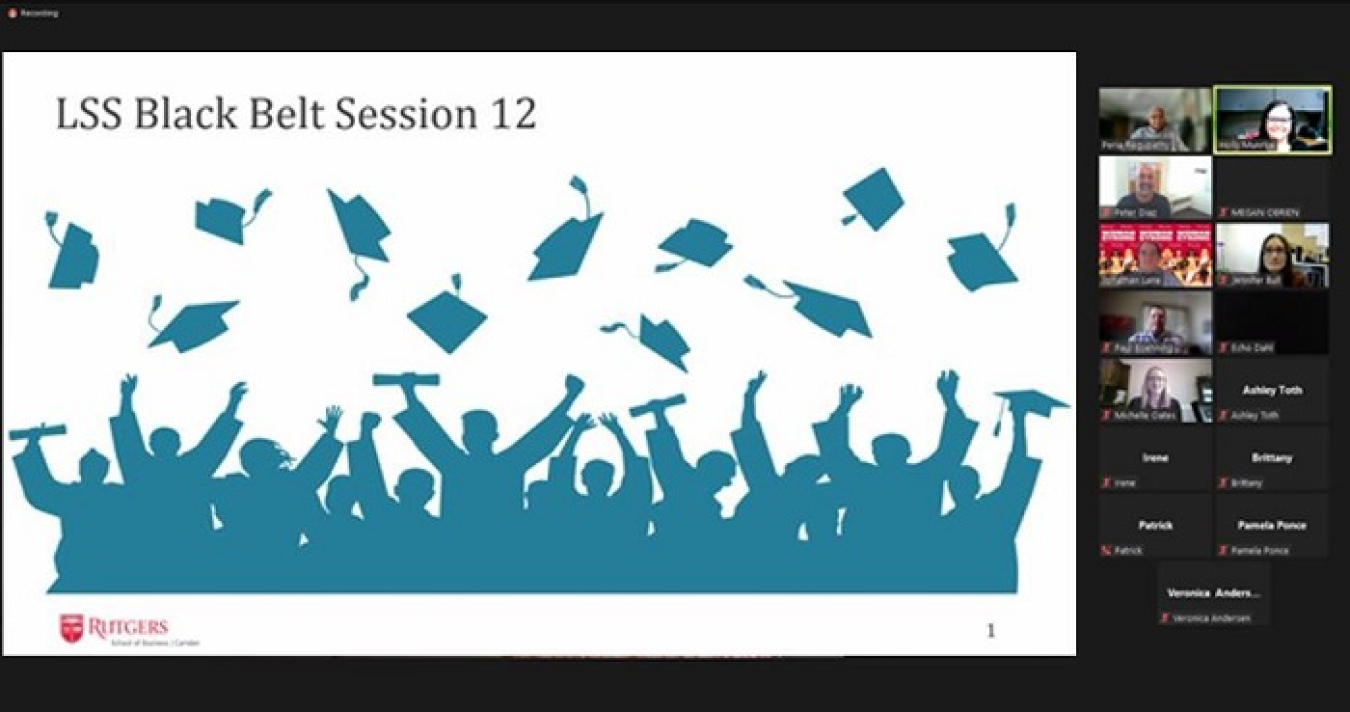
The Black Belt candidates will now work to obtain certification by mentoring Green Belt candidates and facilitating three structured improvement activities under the coaching of the Operating Excellence program, all while continuing to work in their full-time positions.
“The Black Belt training helps you assess challenges from multiple angles,” said Michelle Oates, a Black Belt candidate with WRPS. “I plan to use what I’ve learned to benefit my organization and the Hanford Site as a whole to help achieve high performance outcomes.”
Since 2015, the program has trained and certified more than 140 Green and Black Belts across the Hanford Site, including 40 EM employees.
To receive the latest news and updates about the Office of Environmental Management, submit your e-mail address.