EM’s Safety Significant Confinement Ventilation System (SSCVS) at the Waste Isolation Pilot Plant (WIPP) is rising from the desert.
Office of Environmental Management
June 8, 2021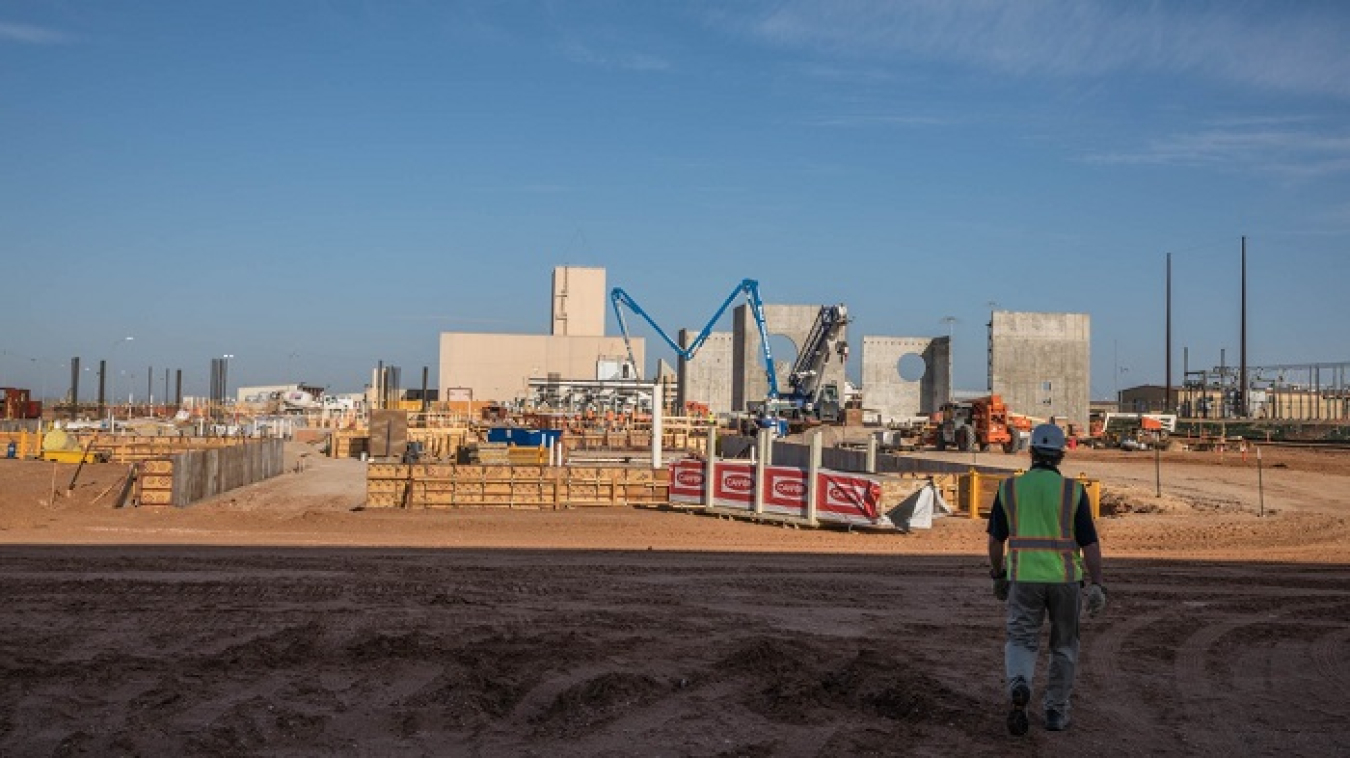
CARLSBAD, N.M. – EM’s Safety Significant Confinement Ventilation System (SSCVS) at the Waste Isolation Pilot Plant (WIPP) is rising from the desert.
The enormous project is WIPP’s largest construction effort in three decades.
“We are making great progress since the new construction contractor (The Industrial Company) came onboard,” said Sean Dunagan, president and project manager of Nuclear Waste Partnership, the WIPP management and operations contractor. “The project is really taking shape, and it will be hugely beneficial to the success of our important national mission.”
The largest containment fan system among DOE facilities, the SSCVS is a modern air supply system designed to run continuously in unfiltered or high-efficiency particulate air (HEPA) filtration mode. The system provides approximately 540,000 cubic feet per minute (cfm) of air to the underground, significantly more than the 170,000 maximum cfm provided by the current ventilation operation.
The increased airflow allows simultaneous mining, rock bolting, waste emplacement, maintenance, and experimental scientific operations. The permanent ventilation construction project is scheduled for completion in 2025.
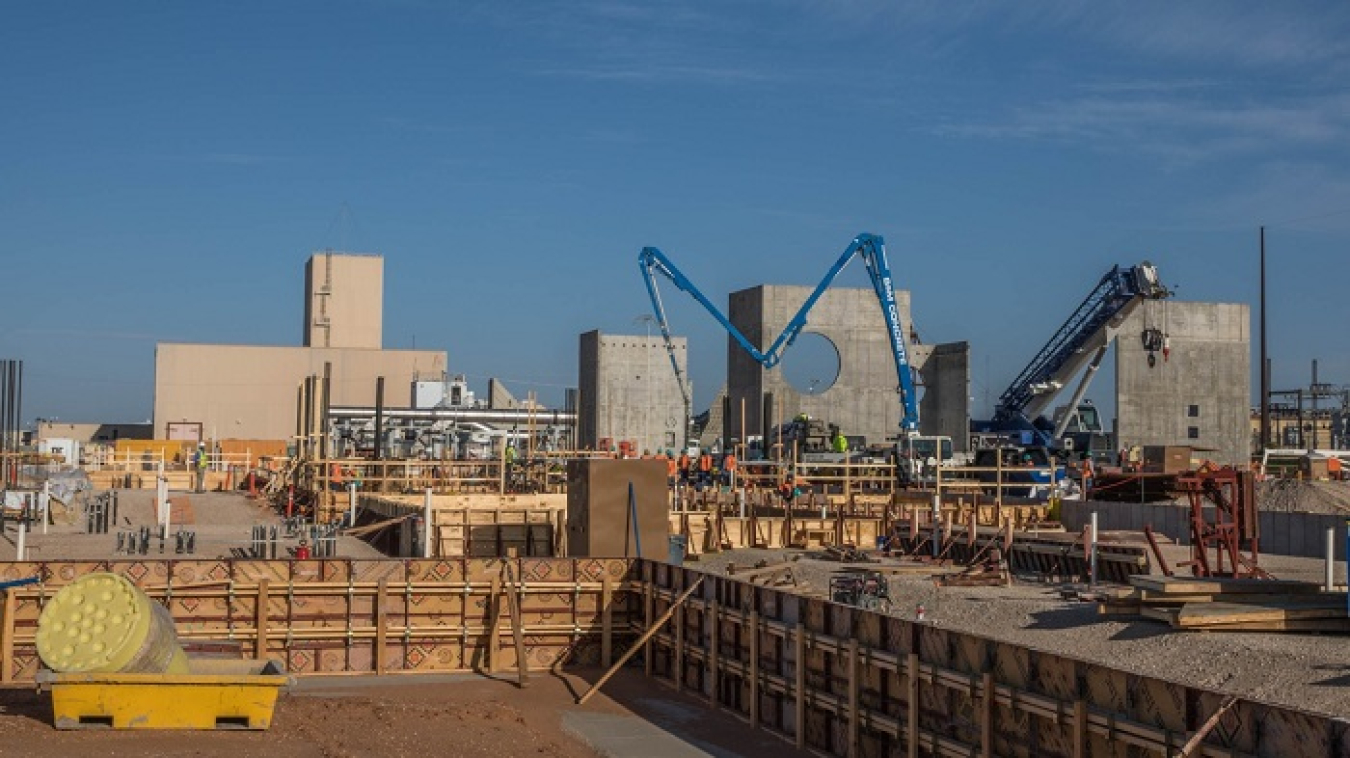
The SSCVS project includes two primary buildings, the Salt Reduction Building (SRB) and the New Filter Building (NFB), as well as support structures such as a fabrication building and trailers for contractors and staff involved with the immense project. The SRB prefilters salt-laden air coming from the WIPP underground, while the NFB has fans and HEPA filtration to further remove contaminants from the exhaust air.
The first of 44 concrete pours on the NFB foundation, known as slab-on-grade, were completed in mid-May. The concrete and rebar steel work are the first safety-significant work for the SSCVS. The pours continue through August.
Rebar coming out of the ground at the building indicates where shear walls are located. The shear walls are load-bearing walls that precast panels attach to.
The shear walls for the SRB, 41 feet in height, are already in place and support prefabricated walls under construction. Those prefabricated walls are slated to go up starting in July. Columns, beams, and side panels are added next, followed by roof panels to complete the building.
The SRB is scheduled to be enclosed by the end of this year. Completion of construction of the SRB is an EM 2021 priority.
The building’s salt reduction units have started to arrive. The cleansed air coming from the SRB next heads to the NFB, which has four 1,000-horsepower fans pulling the air through HEPA filtration before it exits through a 125-foot stack.
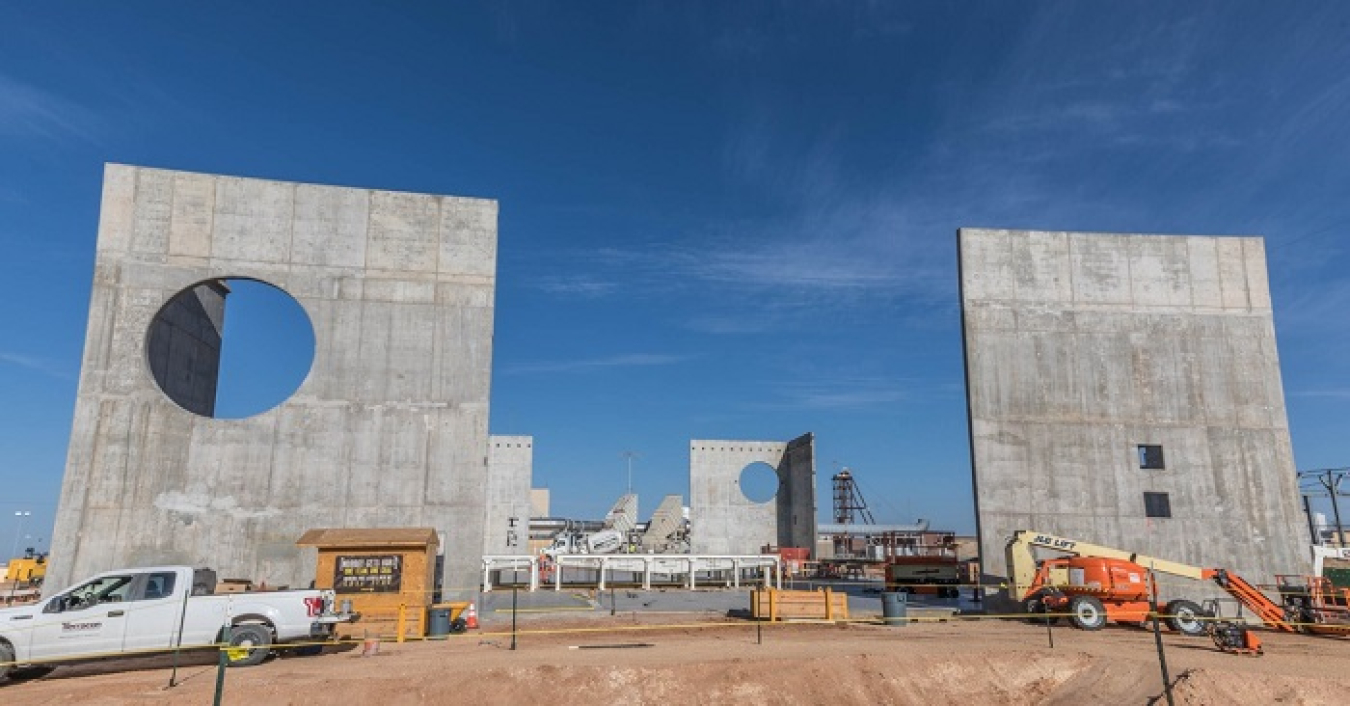
Fifteen of 20 HEPA filter units are stored in shrink-wrap in the fabrication building, with the remaining seven scheduled to arrive by Sept. 30.
Located in the northernmost part of the Chihuahuan desert, WIPP doesn’t get much rainfall but when it does, it’s mostly in the form of massive summer thunderstorms. The underground stormwater runoff system, which includes drains, pipes, and runoff ponds, is essentially complete. Good thing, too: it was put to the test recently by heavy storms that rolled through the area.
Workers have finished installing thousands of feet of electrical conduit, running from a nearby substation.
WIPP is also gaining a new fire water system, including storage tanks, larger mains, and an alarm system. Part of the system loops around the SSCVS.
During the week of May 24, the entire south section of the loop was installed at once, a leap toward completion of the project’s underground work.
The SSCVS and other major infrastructure improvement projects help ensure WIPP can safely continue its mission of transuranic waste disposal for decades to come.
“We are pleased to see the resumption of significant work activities using a deliberate approach,” said Reinhard Knerr, manager of EM’s Carlsbad Field Office. “This critical project allows us to increase the amount of air into the underground, supporting more efficient emplacement and mining activities.”
To receive the latest news and updates about the Office of Environmental Management, submit your e-mail address.