Percheron Power of Kennewick, Washington, recently concluded an initial round of prototype testing for their Composite Archimedes Hydrodynamic Screw.
December 17, 2018Percheron Power of Kennewick, Washington, recently concluded an initial round of prototype testing for their Composite Archimedes Hydrodynamic Screw (CAHS) turbine at Utah State University’s Water Research Lab in Logan, Utah. Percheron improved the design by performing computerized fluid dynamics (CFD) modeling and using a unique composite material to achieve 90 percent turbine performance efficiency. As the first composite screw-turbine to be tested at full-scale in the U.S., Percheron’s device produced close to 35 kilowatts of power, enough to potentially power several homes. The composite design also showed a low risk for potential environmental impacts and reduced deployment costs, which are encouraging signs for scaling-up and deploying the technology to existing sites in the U.S.
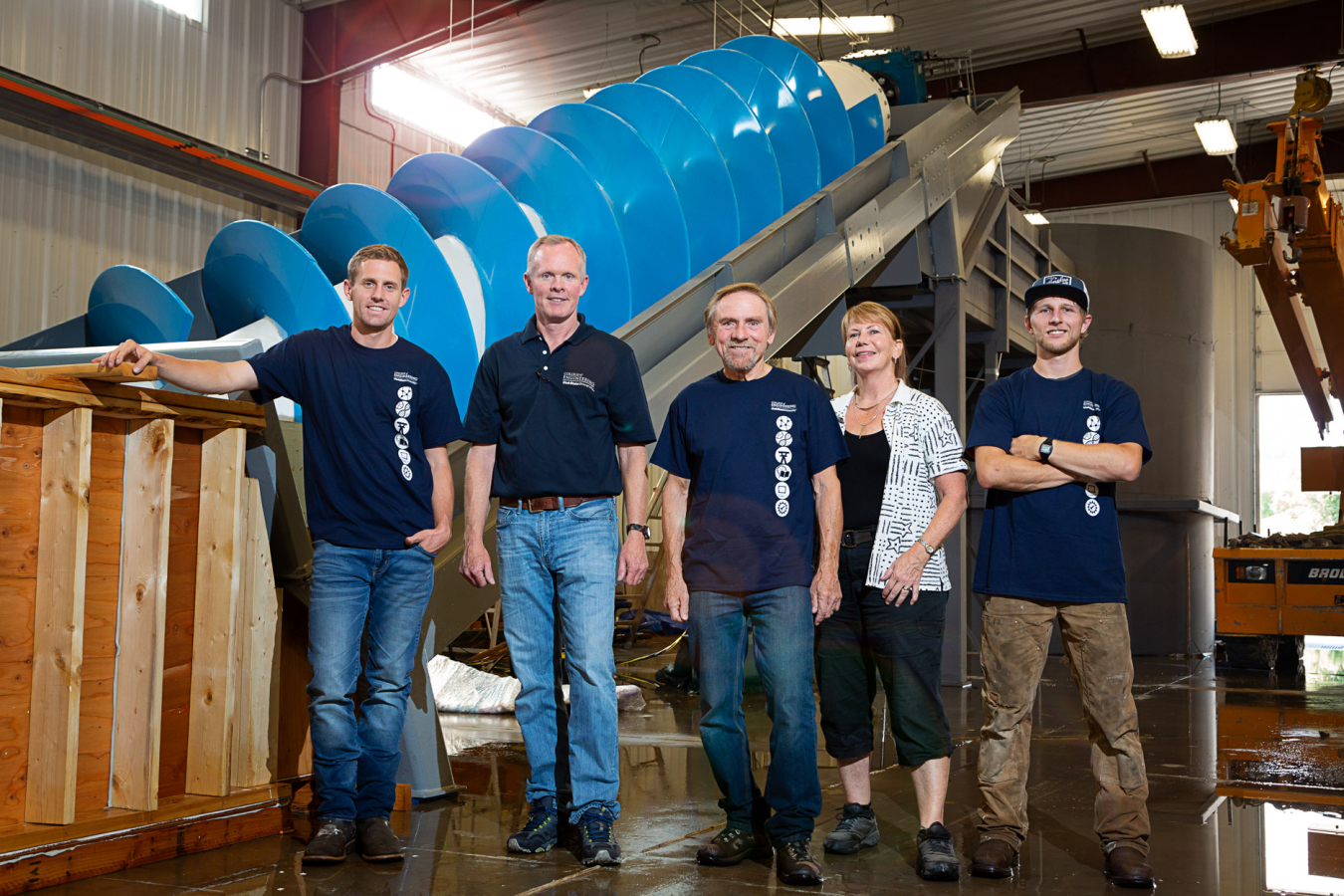
Photo credit: Utah Water Research Lab
While Percheron's technology presents a new development and manufacturing approach, Archimedes Hydrodynamic Screw (AHS) turbines have been used for decades, particularly in Europe. AHS turbine designs are derived from the Archimedes screw, which has been used since ancient Egyptian times as an irrigation tool. AHS turbines are now typically installed at sites where an elevation difference causes water to flow downward, which pushes on a set of turbine blades and causes rotation. The energy generated from blade rotation is then captured by an electrical generator tied to the main shaft of the screw. Due to their low rotational speed and wide diameters that prevent pressure buildup, AHS turbines support efficient downstream fish passage.
Though AHS turbines are an established technology, most designs are constrained by size and potentially costly to construct using expensive steel. Transportation is another challenge, as AHS turbines are not currently manufactured in the U.S. and have to be transported from overseas as one large, pre-assembled piece of steel. Percheron's technology is composed of composite materials that are made from an advanced manufacturing technique known as Light Resin Transfer Molding, which results in lighter components that are easily replicable. CAHS turbines can be shipped in pieces and put together on-site, which can greatly reduce transportation and capital costs. The company has a pending patent application on its design, which if successful, could enable developers to base component size considerations on hydraulic optimization, rather than facility fabrication and transportation constraints and costs.
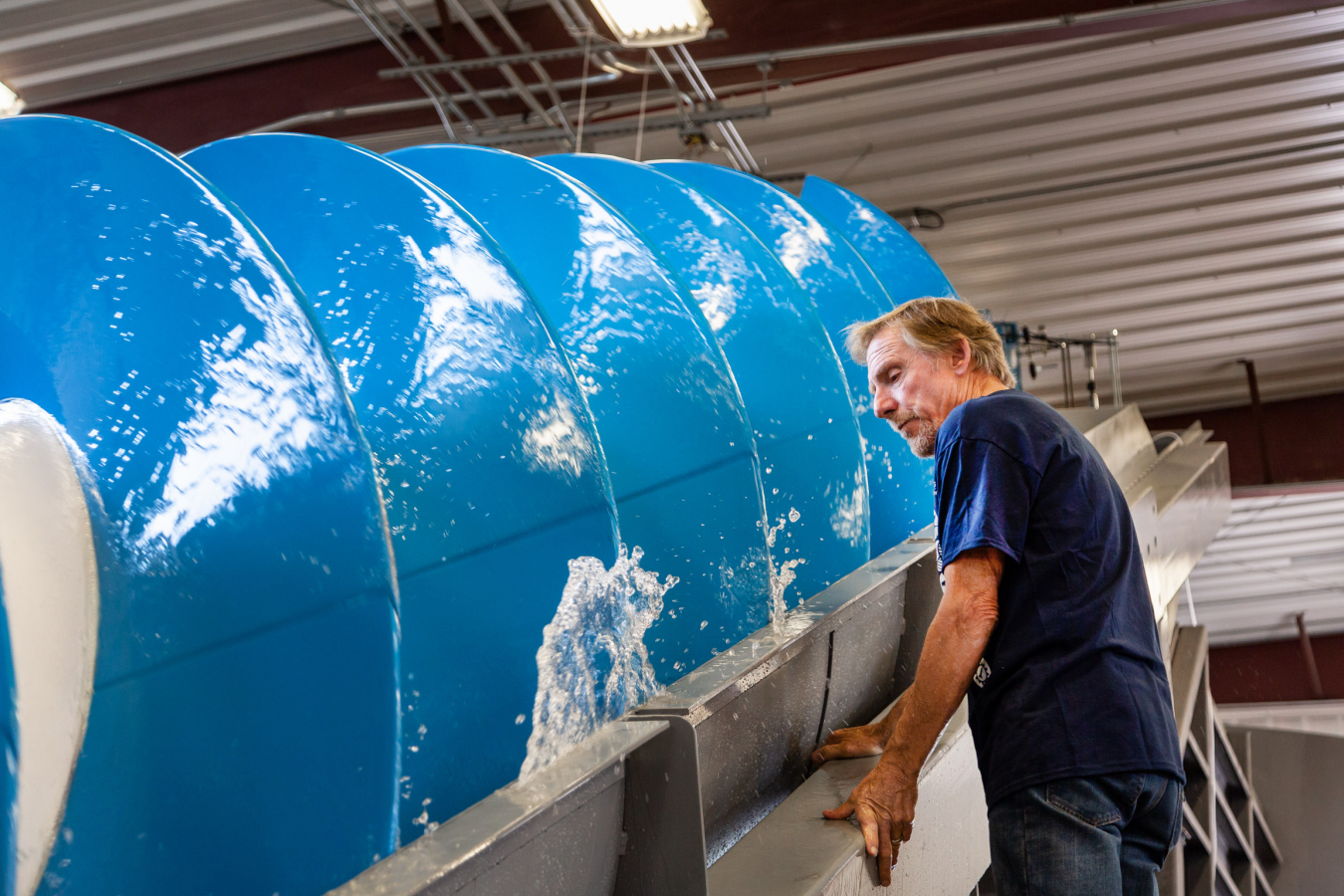
Photo credit: Utah Water Research Lab
Prior to manufacturing and testing the CAHS prototype, Percheron received assistance from Pacific Northwest National Laboratory through the first round of the Energy Department’s Small Business Voucher Program to optimize and validate the CAHS blade shape and design. With continued support from the Water Power Technologies Office, Percheron is conducting an extensive evaluation of existing man-made structures such as dams, canals, and weirs in hopes of field testing a full-scale version of their design in the near future.