WASHINGTON, D.C. – EM Safety, Security, and Quality Programs Deputy Assistant Secretary James Hutton recently spoke with EM Update about the EM program’s improvements in safety culture.
March 31, 2016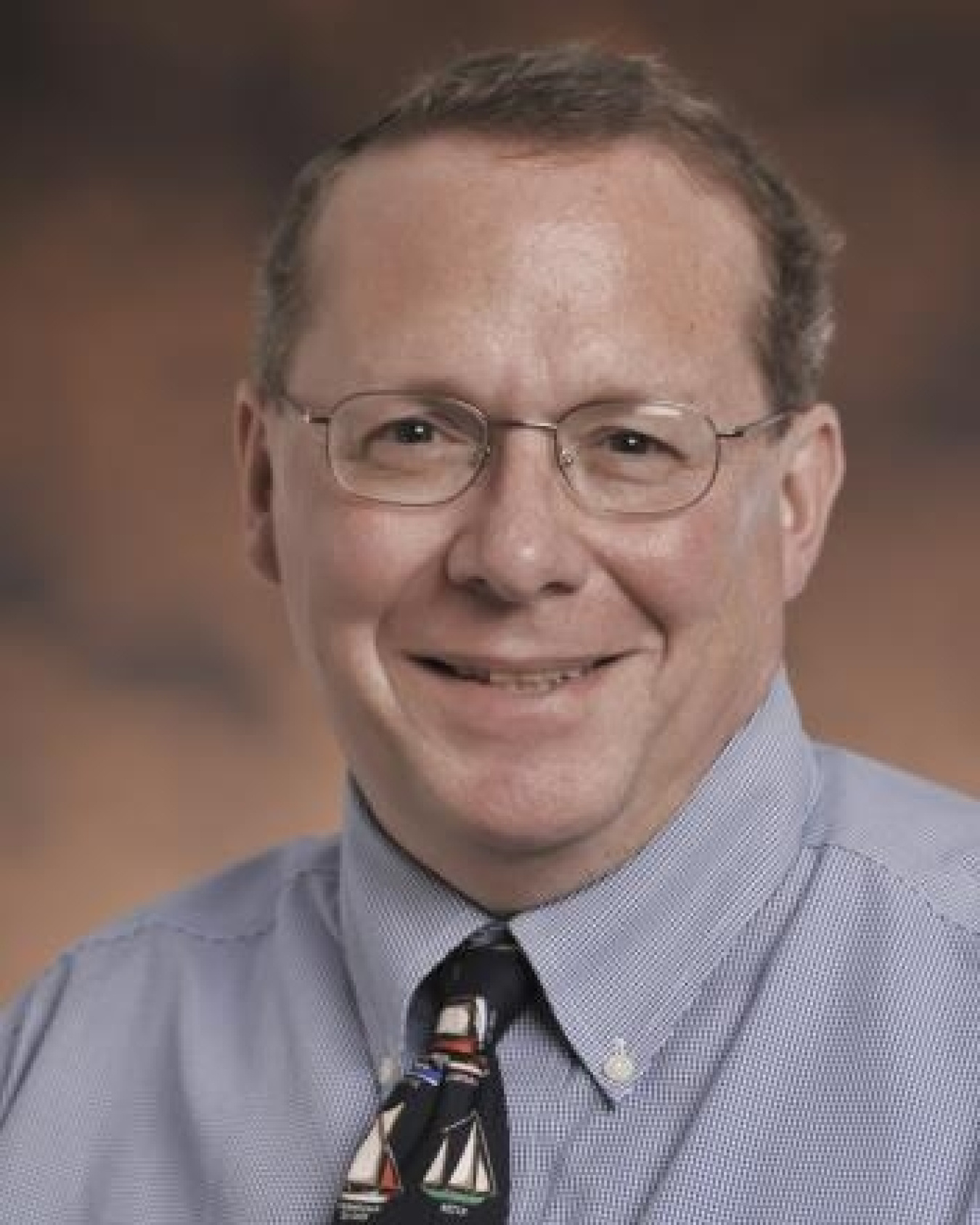
EM Safety, Security, and Quality Programs Deputy Assistant Secretary James Hutton
WASHINGTON, D.C. – EM Safety, Security, and Quality Programs Deputy Assistant Secretary James Hutton recently spoke with EM Update about the EM program’s improvements in safety culture.
1. It's now almost five years since the Defense Nuclear Facilities Safety Board raised the visibility of the topic of safety culture by issuing DOE a formal Recommendation calling for improvements. What actions has DOE taken since then to make improvements?
The Department has taken significant actions to strengthen the Department’s overall safety culture because it’s the right thing to do. First, the Department described just what it expects in terms of senior leader behavior by issuing the Integrated Safety Management System Guide, attachment 10. The Department took on an unprecedented training effort based on this leader behavioral guidance, starting at the top. Well over 2,000 DOE and contractor senior leaders have attended a course in Leadership for a Safety Conscious Work Environment (SCWE).
To provide endurable and sustainable changes, the Department has strategically imbedded the expectations for safety culture and SCWE within the existing Integrated Safety Management System (ISM). The Secretary and Deputy Secretary have also made a personal commitment to health and safety.
The Department’s Safety Culture Improvement Panel (SCIP) was established in May 2015. The panel, made up of representatives from across the Department, has been tasked with strengthening contractual language associated with safety culture; working with the National Training Center in developing training for federal and contractor first-line supervisors and employees; establishing of performance metrics and methods; and evaluating Departmental trends that may have an impact on safety culture and SCWE.
As cited by the Secretary in one of the recent all-hands meetings, significant improvements in safety culture have been made across the Department. However, this is about continuous improvement, and the Departmental and EM efforts will continue to remain a focus area to strengthen and improve safety culture and the concept of a safety conscious work environment.
2. What steps has EM taken to improve safety culture at its sites and at headquarters? Going forward, what other actions, if any, are seen as needed?
A total of 11 EM sites and 21 contractor organizations have developed comprehensive Safety Culture Sustainment Plans that identify improvements in the organizational culture and safety culture areas, as well as SCWE in the areas of leadership, employee engagement, and organizational learning. Each site will be required to update their plans as part of their periodic ISM Declaration — about every 18 to 24 months — meaning this continuous improvement effort will endure over time.
EM has played an integral role in these improvements in headquarters, as well as in the field. EM has recently incorporated safety culture in our oversight activities. In addition, EM leadership has sponsored activities to improve organization and safety culture, as well as SCWE.
EM is leading and supporting the DOE National Training Center’s delivery of senior leadership training and development of the frontline leadership training on safety culture. In addition, EM, in coordination with DOE’s Office of Environment, Health, Safety and Security, has developed a two-hour Safety Culture Fundamentals Workshop for employees, which has been piloted for over 1,100 federal and contractor employees at Oak Ridge, Carlsbad, and Idaho, and is being presented this week at Hanford’s Office of River Protection.
EM will be presenting the two-hour Safety Culture Fundamentals Workshop for all EM headquarters employees, which will provide tools and resources for each employee to positively influence their day-to-day organizational culture.
3. Are there factors at EM headquarters that make it more, or less, difficult to sustain a strong safety culture than in the field?
There are not necessarily factors that make it more or less difficult to sustain a strong safety culture at headquarters or the field. The goal is to implement safety culture and SCWE concepts consistently across EM, while providing the flexibility to tailor the sustainable actions to those that a specific organization needs.
The Department’s definition of safety culture is “an organization’s values and behaviors, modeled by its leaders and internalized by its members, that serve to make safe performance of work the overriding priority to protect workers, the environment, and the public.”
There is a misperception that “safety” culture is only about industrial safety and that the concept of safety culture applies only to the field elements and contractors. The term “safety” is not narrowly defined; rather, the ISM requirements emphasize that the definition of “safety” is broad and is applicable to every individual in every capacity within EM.
EM recognizes that in order to be successful in positively influencing the safety culture, efforts must also be focused on improving the organizational culture and SCWE. It is really not possible for the concept of SCWE to be implemented in the organization if the overall organizational culture is weak. And it is really not possible to have a strong safety culture if the concept of SCWE is not implemented in the organization. Thus, EM headquarters is focusing continuous improvement efforts in all three areas — organizational culture, safety culture, and SCWE, with special emphasis on the Safety Culture Focus Areas of leadership, employee engagement, and organizational learning.
4. How does EM know that it is making improvements in safety culture? How can these improvements be sustained over the long term?
We know we are making improvements in safety culture because we are seeing leadership behaviors that demonstrate a strong safety culture. We see senior leaders that do not hesitate to stop work to address safety issues. We’ve seen that at all our sites — Savannah River, Idaho, Hanford, the Waste Isolation Pilot Plant, Oak Ridge, the Portsmouth/Paducah Project Office, the Separations Process Research Unit site, and Moab. When performance issues occur, these leaders take action to take control of the situation, prevent additional events, and take the time necessary to investigate, identify causes, formulate corrective actions, and effectively implement those corrective actions.
That is what a strong safety culture looks like. These work pauses are a sign of a strong safety culture, just like an individual worker stopping to question a step in a work plan.
Questioning, acknowledging performance deficiencies, taking effective corrective actions, stopping when uncertain — these are signposts of strong safety culture — and leading indicators of strong future performance. Paradoxically, when we slow down and take time to do what it takes to achieve operational excellence, we find that we get done sooner, and with much less complication and rework.
We’ve also seen improvements across the Department in terms of participation in the Federal Employee Viewpoint Survey, which is administered to federal personnel only. In 2015, DOE achieved a 68 percent response rate, or an increase of 18 percent over the previous year. In 2015, EM achieved a response rate of 70 percent. Within EM, there was a statistically significant increase in the positive responses to the statement, “I can disclose a suspected violation of any law, rule or regulation without fear of reprisal,” with 70 percent of participants having responded positively.
Improvements are also being seen in the federal workplaces at the sites, with substantial improvements being seen within the Hanford Office of River Protection, as well as the other federal site offices.
5. Lastly, what is EM's message to its workforce — both federal and contractor — when it comes to safety culture?
To sustain long-term improvement in safety culture is hard work, every single day. It is work that will never be “done.” It takes concerted, deliberate, and continued efforts by each individual within the EM organization. It is up to each one of us to positively influence the culture to support an open and collaborative work environment.
In the end, the same behaviors and habits of excellence that improve safety culture affect all aspects of our performance and lead to overall operational excellence.